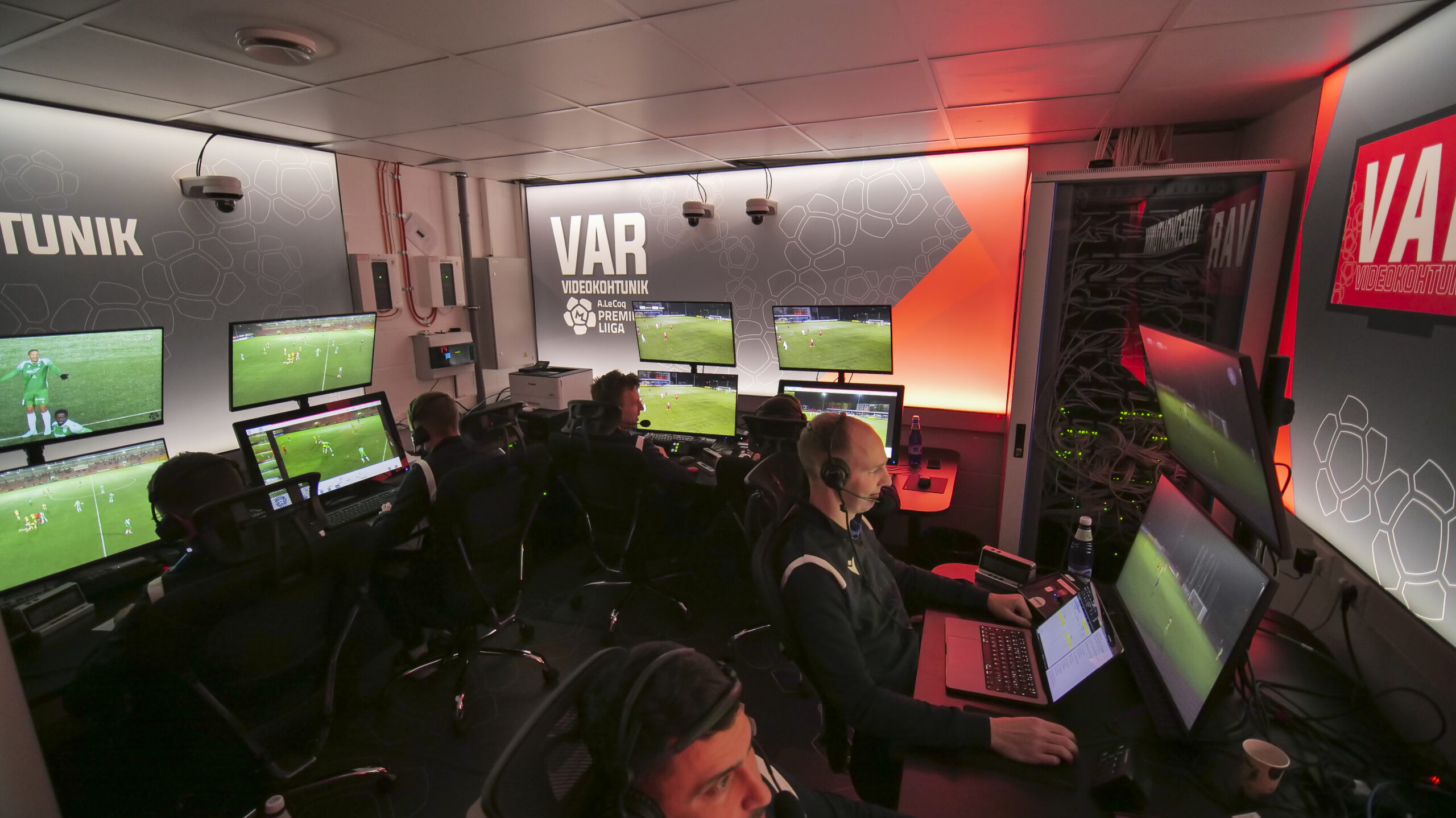
Since 2013, VOGO has established itself as a Sportech innovator, delivering cutting-edge audio and video solutions to the world of sports. The company has also extended its expertise into industry and audiovisual applications. VOGO’s secret? Constant innovation and a sharp focus on quality: which is why they needed a partner like WATS.
Video Assistant Referee (VAR)
In the world of professional sports, VOGO is especially renowned for its contributions to Video Assistant Referee (VAR) systems. Their innovative solutions support referees with real-time video replay and decision-making tools, ensuring fair play and boosting the accuracy of officiating during critical moments of the game. Beyond sports, VOGO extends its expertise into sectors like construction, energy, railways, and noisy industrial environments, offering robust audio communication systems designed for safety and efficiency.
Integrating NI TestStand with WATS
In collaboration with Mesulog, WATS’ partner in France, and through integration with NI TestStand, VOGO partnered with WATS to bring greater clarity and consistency to their test data. We have spoken with Fabien de Barros from VOGO to learn more about how WATS is helping them level up operations – both in-house and across their supplier network.
“We use WATS extensively for supplier production monitoring. It allows us to monitor the number of products tested, failure rates, scrap rates, and nature of the main failures, among other things. We update suppliers regularly and ask them to take action when a defect is recurrent.”
Fabien De Barros, Technical Manager, VOGO
Test data that travels
For a company like VOGO, which works closely with electronics manufacturing services (EMS) providers, test data can easily become scattered or hard to trace. That’s why one of the biggest quick wins with WATS lies in improved supplier monitoring. With a joined-up view of the test process across different production environments – even when subcontractors are testing with their own components – VOGO gained a high level of transparency.
Now, they can easily track quantities tested, failure rates, scrap rates, and common defects. Regular meetings with suppliers are backed by solid data, which means discussions about recurring issues are informed and actionable.
One product, one story
WATS has become an essential tool for understanding each product’s lifecycle – from PCBA testing to full product assembly, all the way through in-house configuration. With serialized tracking where possible, every step of a product’s testing journey can be documented, making it easy to follow.
Even in cases where traceability is managed by batch rather than serial number, VOGO is exploring ways to expand its use of WATS. One area of focus for the year ahead is input control – guiding operators through inspections and storing those results for deeper analysis later.
“This tool also enables us to remotely understand what is happening much more easily, adjust the test bench, and verify that there are no issues with the test sequences. We feel much more reassured regarding potential non-conformities reported by clients, as we have access to the entire product history.”
Fabien De Barros, Technical Manager, VOGO
Beyond the Bench
Some types of testing – like audio – don’t lend themselves easily to automated systems or spreadsheets. At VOGO, that’s where things used to get tricky. Subjective tests like listening checks were difficult to document consistently, especially across many different product lines. WATS is helping bridge that gap, offering a more structured approach even for these more human-centric, qualitative checks.
Detecting Outliers
Being able to access detailed test results has also helped the team uncover rare issues – problems that only crop up in one product out of every few hundred or thousand. With WATS, those outliers are no longer invisible.
The Next Steps
VOGO is still early in its WATS journey, but from expanding input control to exploring new ways to integrate test data from its growing network of subcontractors, the possibilities are huge. And with some of VOGO’s suppliers already using WATS themselves, the ability to share knowledge and accelerate learning is ready to be tapped into.
Learn more about VOGO at vogo-group.com