Compliance and regulatory requirements, contracted expectations of product performance, and increasing global competition from low-cost competitors means that the margin for error for product failure in industrial electronics is unforgiving.
Rigid, reactive quality assurance
A typical protective measure is the implementation of rigid quality assurance controls before a product is shipped. Although this has the potential to avoid the most critical product failures, it completely fails to facilitate continuous improvement and manufacturing effectiveness. This type of quality assurance also fails to recognize that problems are introduced at different manufacturing stages and should be detected and fixed where they take place. The result is that your product introduction and industrialization processes bleed money through inefficiency and lack of transparency.
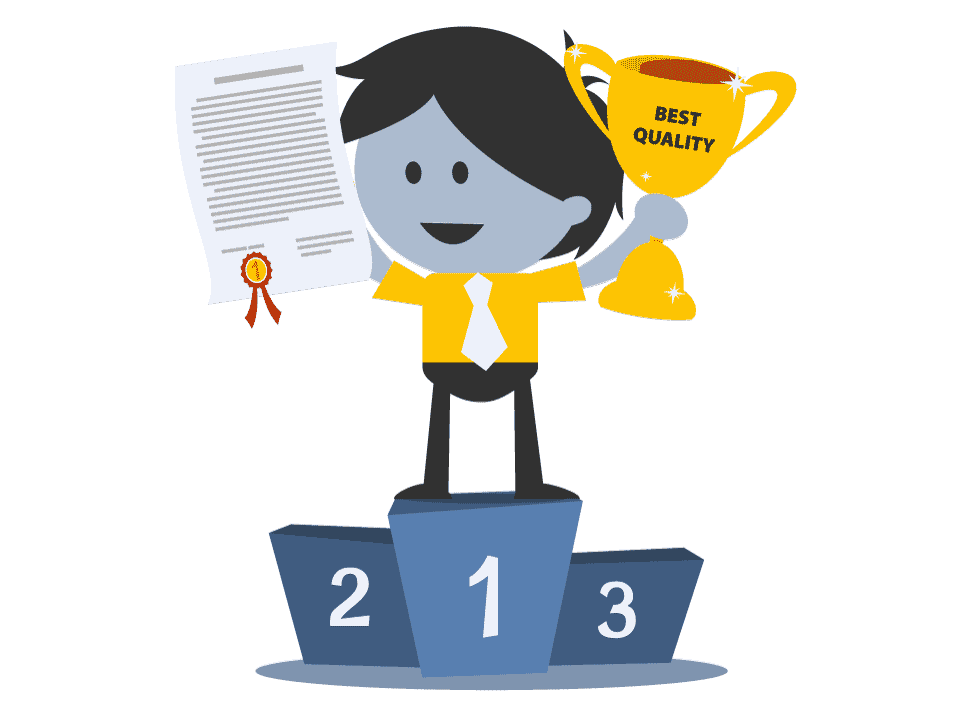
Read more”When we use WATS, it’s like it does some magic, and then the data we need is suddenly available. It is unrivaled in its ability to monitor our testing and empower us to improve our production environment.
Svein Olav HusebySenior Industrialization Engineer, Q-Free
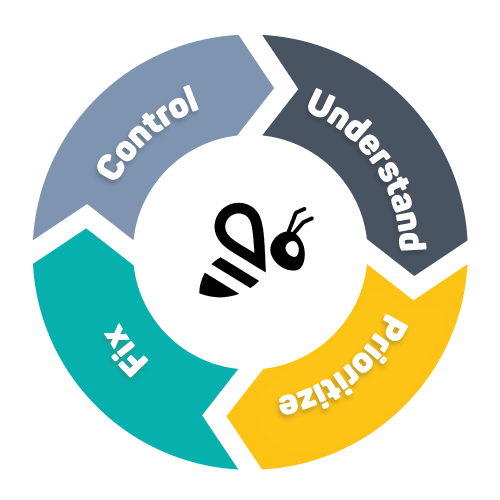
Better Manufacturing Intelligence
WATS enables the flow of mission-critical data related to manufacturing and field failures. By ensuring that data from testing, repair and RMA is given to those best equipped to evaluate its severity and required response. It is the perfect example of how companies making Industrial Electronics can add software technologies for Digitization and Industrial IoT on top of their regular activities, to understand their strengths and weaknesses better.
WATS helps organizations understand what is causing their products to fail during manufacturing or in the field – both real failures and false failures. It can then help find fixes, and record their results – enabling continuous improvement.
Read about the WATS top-down approach to quality management.
”By selecting WATS we will gain real-time information from our production sites globally. We can easily investigate issues that occur by analysis tools and reports provided in WATS
Jonas NilefellEMS Quality Manager, ABB Control Technologies
Total product traceability
When a product is finalized, the data accurately reflects the story of how that exact unit came to be. As time goes by, and the inevitable product failures occur, you can use that data to understand the commonalities of those failures, to make sure product recalls become a thing of the past.
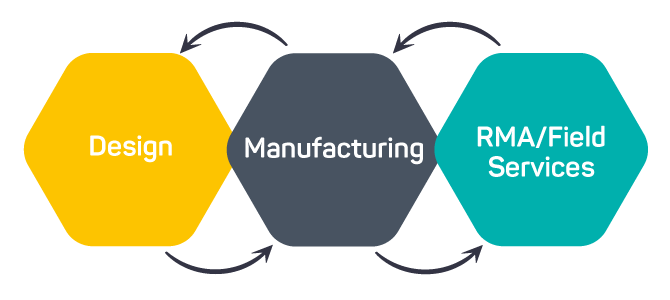
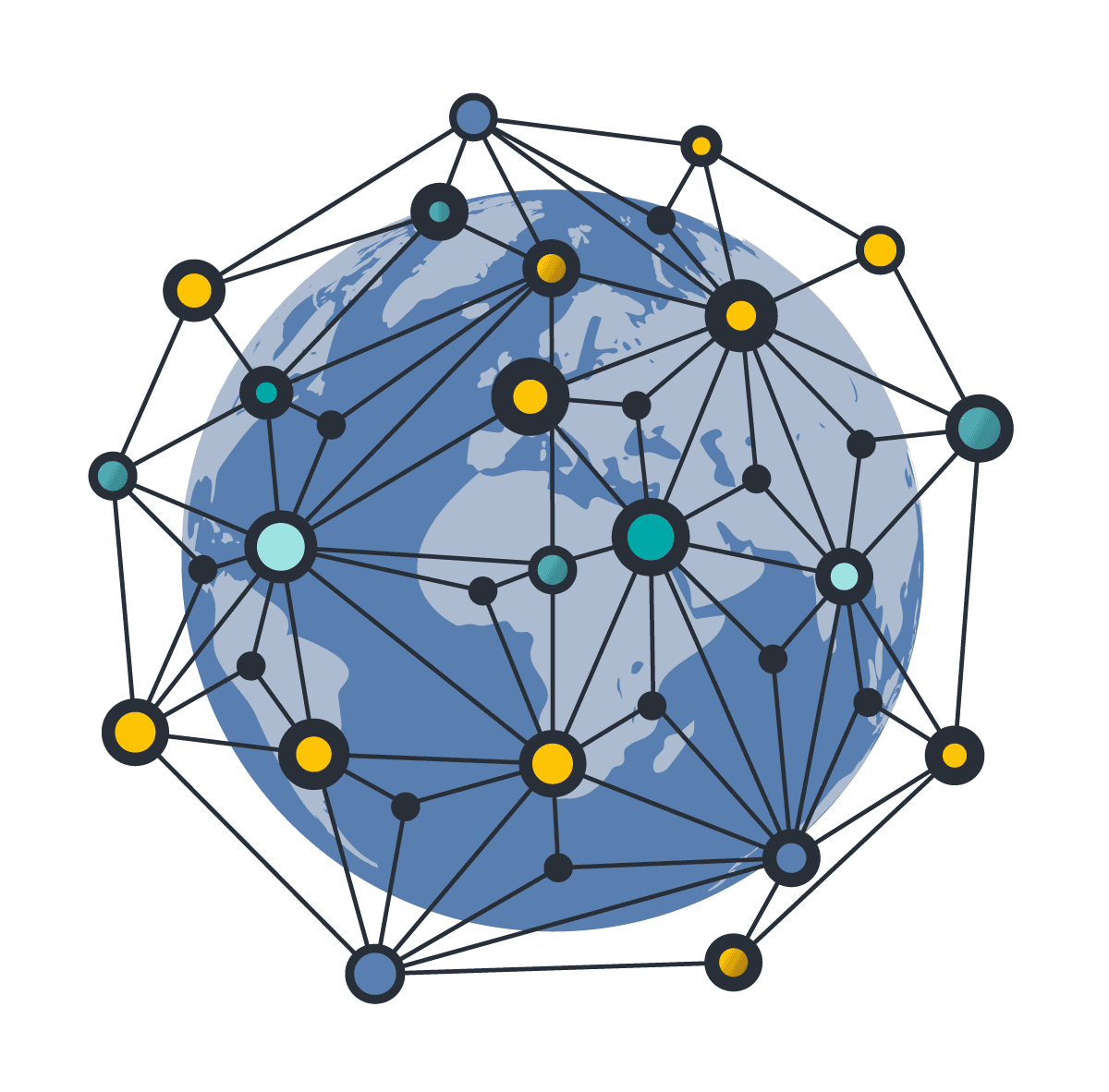
Effective control of global manufacturing and supply chain
WATS helps collect data from any factory worldwide, including your subcontractors. Not only does it help you understand your data, but it also enables you to optimize important activities that often are the root causes of detected and undetected failures. Poor control of test software versions or unit firmware currently in use leads to expensive rework. Uncalibrated or poorly maintained test systems cause false failures and unnecessary downtime in manufacturing. With WATS, all of these problems are effectively managed by standard off-the-shelf functionality.