The use of manufacturing test data to document FDA compliance is an absolute necessity. But this usage does nothing in terms of evaluating and optimizing efficiency. A proactive, high-level approach to manage and analyze this data helps medical companies supply electronics products to the market at a far lower cost.
The Cost of Quality Management
Quality Control, compliance and profitability are not natural companions. In regulated industries, such as the medical electronics industry, a heavy burden falls on those required to ensure compliance. But compliance doesn’t equal efficiency or effectiveness. Ensuring compliance of individual units doesn’t give you anything in terms of business intelligence, continuous improvement and reduction in unit manufacturing costs – unless you use WATS.
Read about the WATS top-down approach to quality management
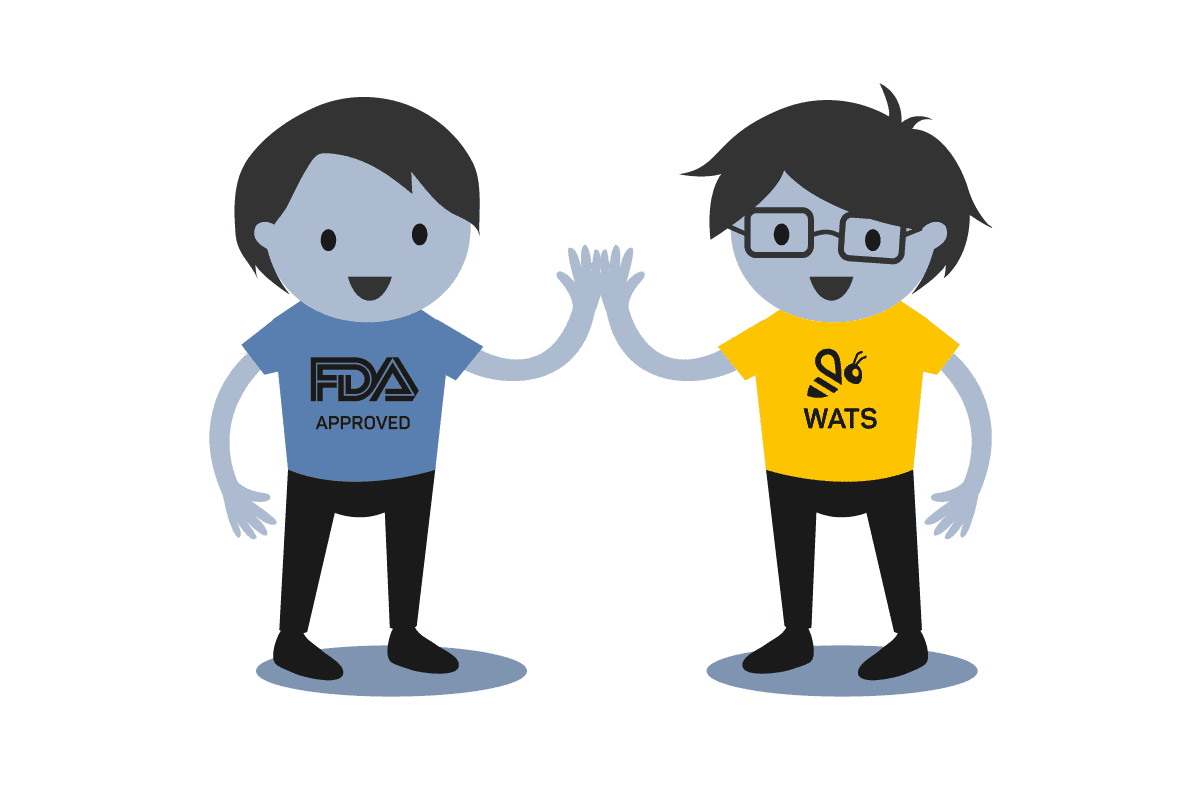
”WATS, is a great tool, also for engineers. Easy to monitor test steps, product yield, and test yield. I especially like the capability to see all CP and CPk’s in a single view of a particular board. In everyday work, WATS improves test equipment, in the long term, WATS eliminates tructural failures.
Marco GeerligsTest Engineer- Nedap
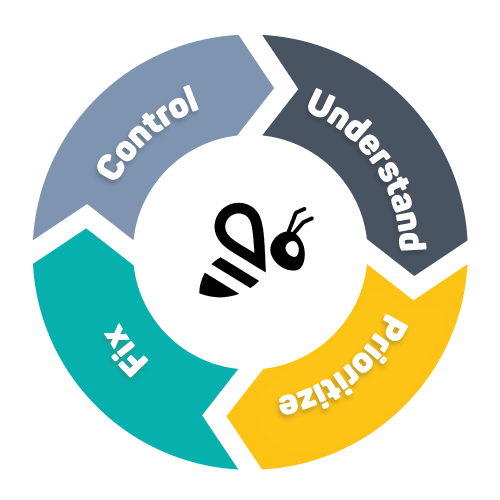
Balancing Quality and Efficiency
WATS helps ensure that the quality of the internal processes doesn’t suffer under the burden of compliance. It provides a high-level view that informs where you have the most significant room for improvement, and what activities and anomalies cost you the most money. This means that the time it takes to break even with your certification investments gets shorter, and that new product introduction comes with less financial risk.
WATS Lives in Parallel to your FDA systems
WATS Test Data Management becomes a parallel implementation to your FDA systems. One is intended to allow you to sell your products, and the other one helps you to make sure that the cost of producing and introducing these products is optimal.
Data-Informed Continuous Improvement
WATS helps organizations understand what is causing their products to fail during manufacturing or in the field – both real failures and false failures. It can then help find fixes, and record their results – enabling continuous improvement. This transparency is one of the core principles of effective Continuous Improvement designs.
It is the perfect example of how companies making an audio device can add software technologies for digitization and industrial IoT on top of their core processes to improve product quality.