The proactive use of real-time aggregated test and repair data from the entire manufacturing supply chain has the potential to significantly improve product quality and internal efficiency for companies in the automotive industry.
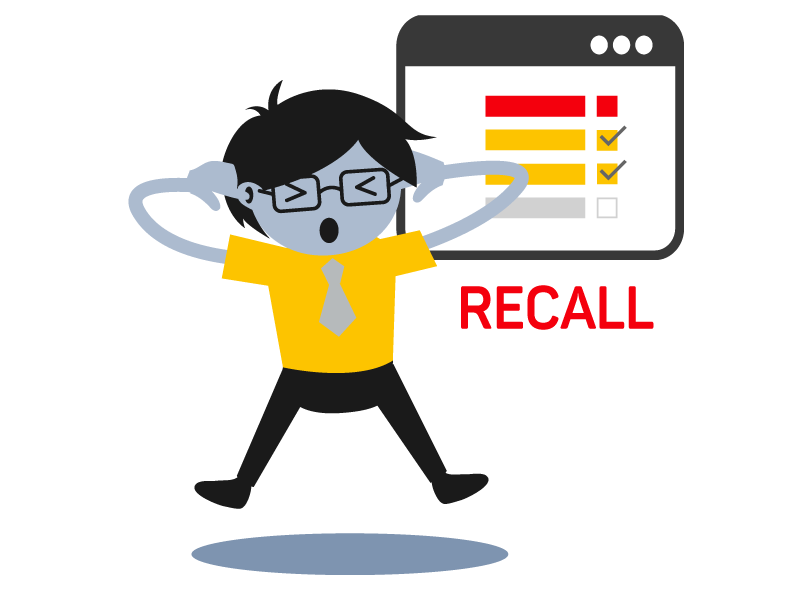
The cost of upstream failures
Defects, warranty claims and recalls can cause serious damage to automotive companies. The combination of high volume, high complexity and highly competitive markets require state-of-the-art data availability, process monitoring and lifecycle learning. Every step in the manufacturing process is a potential source of costly problems, and if these problems are allowed to reach the field, the cost can be catastrophic.
The need to monitor all processes
But, the need to remain competitive puts s heavy strain on the need to stay efficient. Keeping a balance is no longer sustainable, as the dynamics of the industry require you to learn and adapt constantly. As every step in the build process has the potential to introduce new problems, you need a system that allows you to detect the issues where they originate, rather than thorough monitoring of specific measurements late in the build process.
Learn why traditional SPC may be obsolete for monitoring electronics manufacturing.
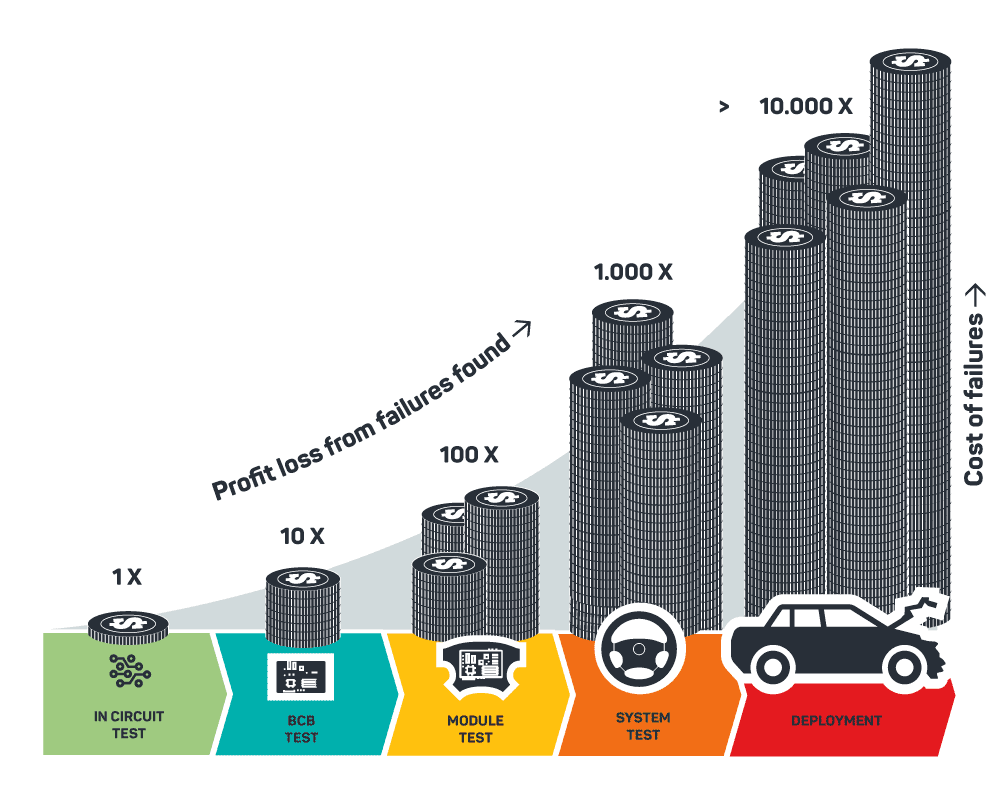
”Etteplan has integrated WATS into several existing test stations. It has been a pleasure to find out how easy the commissioning can be done. WATS has the functionality for analysis and quality improvements. Virinco guys are always listening to the customer and improving the WATS SW based on the feedback collected.
Tero LeppänenDirector, Software and Embedded Solutions, Etteplan Oy
First Pass Yield and Test Data Management
WATS offers an ideal blend of quality control and performance data to boost efficiency. The ability to monitor and contextualize the throughput performance of your manufacturing process, together with field and warranty data, provides a competitive advantage by improving quality assurance, lifecycle learning and supply chain management. The ability to understand specific yield performance in combination with analytics designed to optimize test coverage means you can implement global test monitoring without facing the risk of drowning in false warnings and alarms.
Learning from past incidents
Because WATS enables you to combine manufacturing test and repair data with field failure data, you get the unique ability to correlate failures back to their point of origin. This enables you to prioritize based on frequency and severity and ensure that any implemented fix has the biggest impact possible.
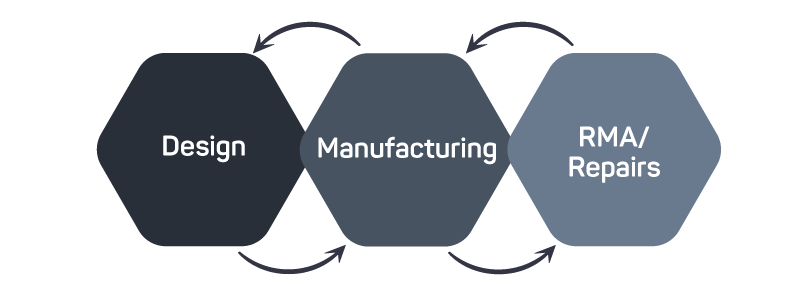