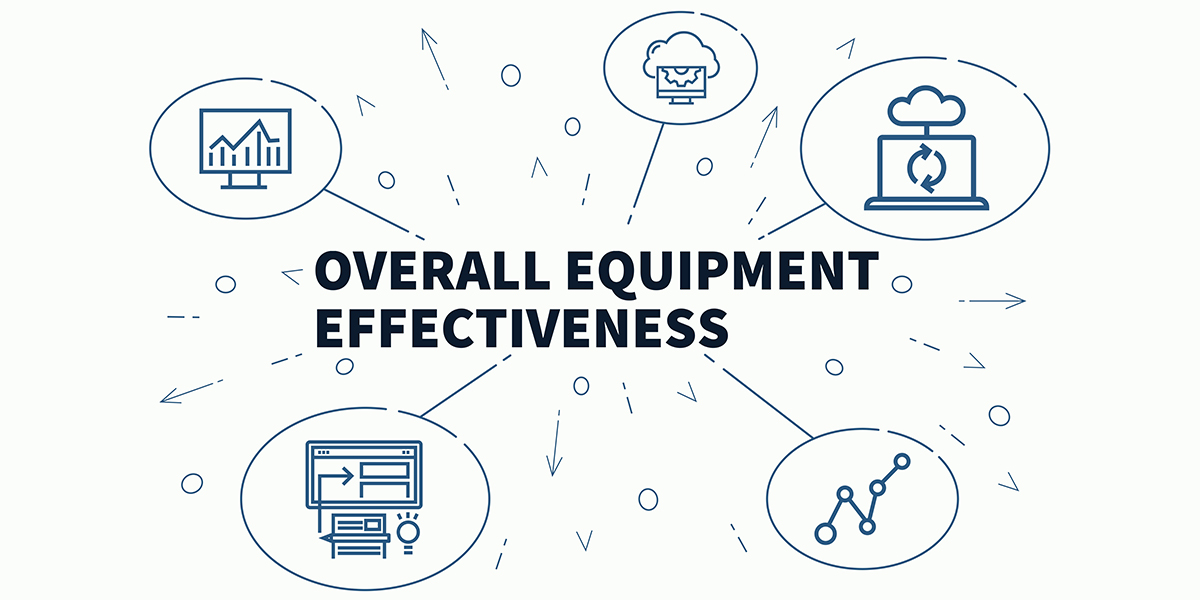
OEE is the Gold Standard for Measuring Productivity
The manufacturing industry gold standard for measuring productivity is Overall Equipment Effectiveness (OEE). Simply put, it identifies the percentage of manufacturing time that is truly productive. An OEE score of 100% means you are manufacturing only good parts, as fast as possible, with no stop time. By measuring OEE and the underlying losses, you will gain important insights on how to systematically improve your manufacturing process.
OEE is a critical metric for
- identifying losses,
- benchmarking progress,
- and improving the productivity of manufacturing equipment.
Through the WATS feature, users are empowered to set target output
Given that efficiency is a self-evident driver, how does an OEE process add value? Through the WATS feature users are empowered to set target output and gain easy access to OEE calculations that combine availability scores, output performance, and quality metrics. The report allows you to see if you are performing up to your true production capacity, or use history to compare periods and set availability of resources/time.
A number of factors to add to the considerations of efficiency
So, for example, we can set some targets and monitor the performance of your production – within a period of, say a week or day – to establish if you are producing the capacity that you are capable of delivering. For instance, if your systems can test 10,000 units per day, and you’re only testing 9,000, you are performing up to 90 percent of the available capacity. Put another way, it is measuring how much is being utilized versus how much free time is available.
Of course, there are a number of factors to add to the considerations of efficiency – such as what happens if this goes to maintenance? Or if I have to calibrate? If I need additional capacity, I can’t just run at 99 percent and then think there is nothing to concern me. Perhaps there is a need to factor five to 10 percent spare capacity? Or perhaps a test station needs to be on constant standby?
Much depends on the industry; if you are operating in a very high cost component manufacturing environment, that will dictate the cost base and the use of testing processes.
WATS takes the guesswork out of efficiency and capacity planning
Another example of how OEE can benefit a user is resource planning enabling you to address such concerns as,
- Do I have any bottlenecks?
- How are these factored into the process?
- Do I need to expand my capacity?
If you are producing 1,000 units per day and you’re not going to produce any more and your capacity is running at 30 percent, that means you have too much additional capacity. But if you’re running at 110 percent capacity then it means you’re stretching, and potentially vulnerable to unforeseen problems – such as production down time. Essentially, the WATS OEE feature takes the guesswork out of efficiency and capacity planning.
The user can justify target figures, such as:
- what is the optimum output
- how productive is the machine
- how much time do you need per task
- establish costs versus output to monitor profitability
Manufacturing is more complex than just switching a machine on or off. Knowing what the parameters are, the context in your business, comparative costs and use of resources all add up to increased efficiency and ultimately profitability in the competitive world of electronics manufacturing.
See how easy our platform is to use
Book a Demo with us today
Learn how WATS can access your test data and let you have a real-time overview of your manufacturing.
Request a Demo