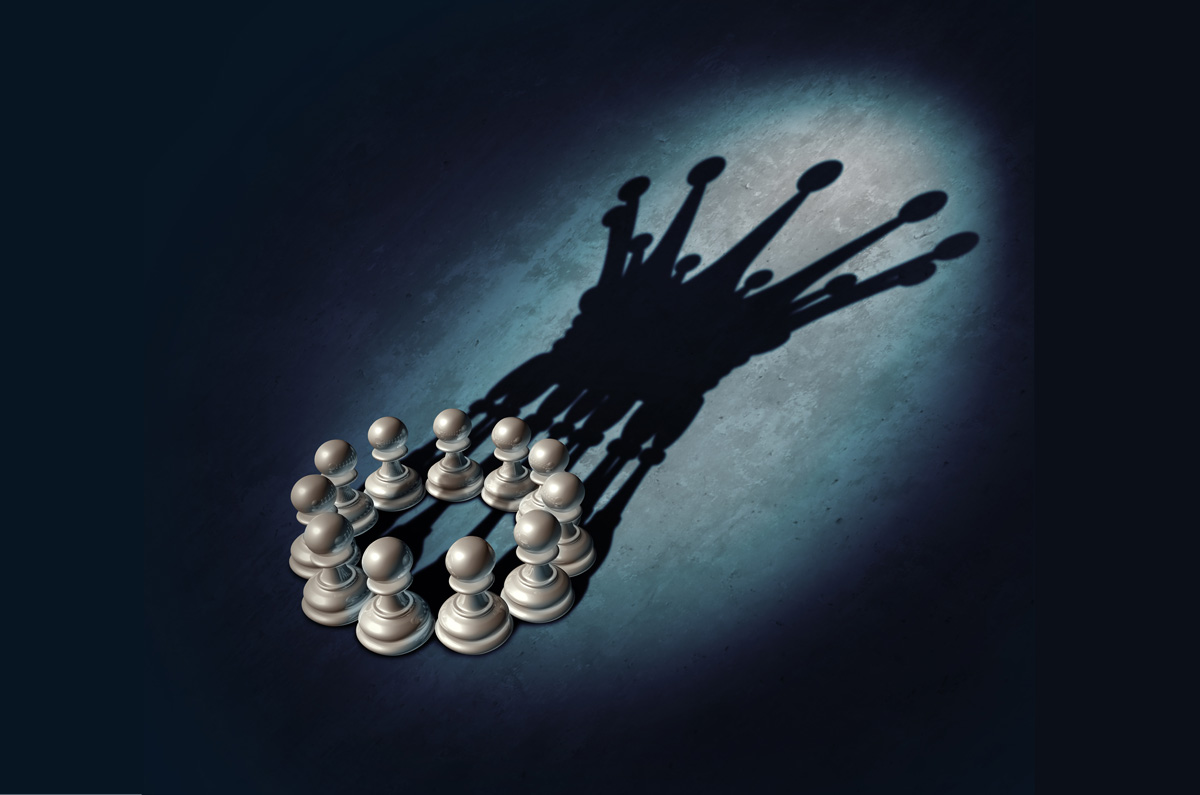
As manufacturers everywhere work hard to shave costs amidst a broader picture of economic challenges and supply chain inflation – some businesses want to bring software together. This certainly makes a lot of sense, it’s potentially cheaper, and can make working with data easier, but is it always the right move? Let’s explore the topic further.
Why Would You Consolidate Software?
Software consolidation in manufacturing businesses is like weaving lots of separate threads into a strong piece of rope. It enables companies to link their assets, creating a single, verifiable source of truth. Why would they do that? Because it helps create optimized, automated processes, and empowered decision-making with fewer errors. That’s cost-saving and quality paired together, which is hard to argue with.
Smart manufacturing platforms can bring about end-to-end visibility and foster cross-device connectivity – that’s laptops, tablets, mobile devices, and HMIs (Human Machine Interface). This access enhances response time and helps drive continuous improvement. By offering comprehensive production visibility, tracking, and asset and machine condition monitoring, operations can actually be improved while also reducing the overhead of multiple software packages.
When business systems aren’t consolidated, there’s a high potential for error. These errors are further compounded as critical data is shuttled from one system to another. Siloed data can lead to poor reporting, which can lead to bad decision-making, and that will only reduce product quality and drive up costs.
Because of all this, software consolidation CAN be transformative, but surely it has its limits? Yes, it certainly does.
Where Consolidation Falls Down
While system consolidation offers lots of benefits, it is equally important to acknowledge that not all operations can be squeezed into one system. Attempting to do so could strain your resources, lead to inefficiencies, and potentially negate the very benefits consolidation is supposed to provide.
A common mistake is to force too many processes into too few tools, especially those not designed for it. An ideal example we use is our customers’ reliance on a combination of databases and Excel for their test data management before they used WATS. Sure, it’s “possible” to use these tools, but while it might save a small amount of money, it’s a much less robust package. In reality, a lot of suggested consolidation can lead to inefficiencies and inaccuracies.
Understanding this, it’s important to strike a balance in your consolidation efforts. Use comprehensive systems where they provide the most value, and employ specialized tools for specific tasks. This dual-pronged approach ensures you can maximize your operational efficiency without compromising on the quality or integrity of your systems.
The journey of system consolidation is less about juggling multiple software and more about managing them in the right way, never stretching a tool beyond what it’s designed for. Software consolidation in manufacturing is about enhancing efficiency, improving visibility, and making informed decisions. Funnily enough, those are also some of the benefits of using WATS. So before you go out and try to cut corners, invest in solutions that get you exactly where you want to be.
Interested in unlocking all the benefits of 24/7 test data visibility in your manufacturing? WATS is the leading solution and the only one you need, so get in touch with us today.