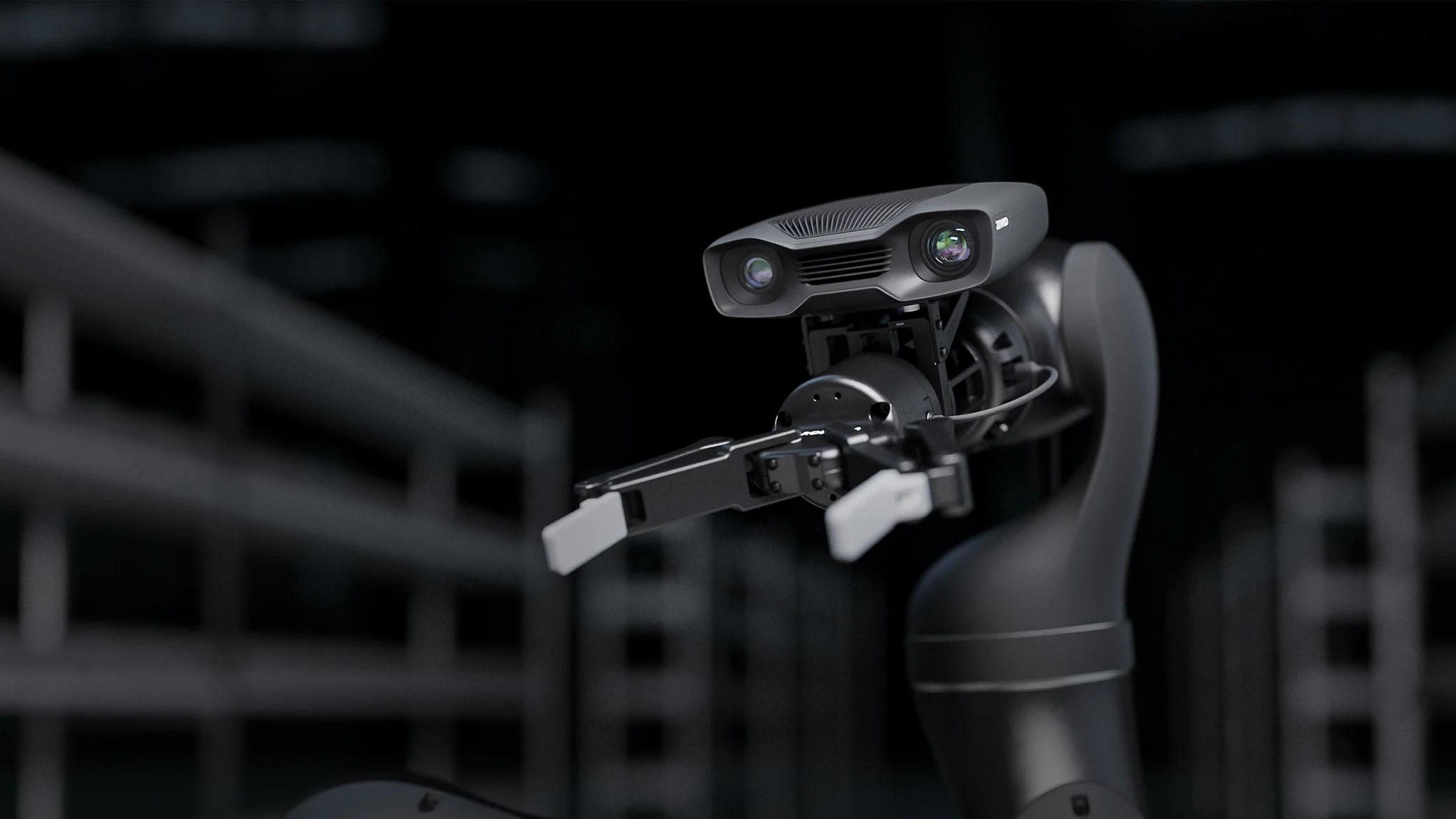
Zivid, a pioneer in the 3D camera industry, is known for developing some of the most advanced 3D imaging solutions on the market – integral to industrial automation. These imaging solutions are pivotal for tasks such as product inspection, bin picking, piece picking, and palletization.
In an effort to stay on top of that unparalleled precision, Zivid has been on a journey of expansion and refinement of its calibration and testing processes, with help from WATS. Learn how in this case.
“The WATS solution has been a game-changer for us. It’s streamlined our calibration and testing processes to a level of efficiency we hadn’t experienced before. We’re not just pleased with WATS; we’re deeply impressed by its impact and the exceptional support we’ve received, which has been pivotal in our successful expansion phase.”
Tor Magnus Briskodden, Production Test Lead, Zivid
Increased scale of production
The Production test & Calibration team at Zivid acts as a key link between Engineering and the supply chain. They needed to enhance testing, calibration procedures, and the necessary jigs to match an increasing scale of production which was a significant step that required serious consideration and implementation.
The Challenge: Lack of Consistent Data and True First-pass Yield
Prior to the integration of WATS, Zivid faced challenges with an internal tool for test management that lacked consistency and the ability to track true first-pass yields. The blending of data from internal development testing and production testing made it virtually impossible to scale testing. This was a real pain point for Zivid, compounded by the resource-intensive nature of maintaining and updating an internally developed tool. As we always say: DIY is not the way.
The Solution: Live Dashboards and True First Pass Yield Data
We stepped in to streamline Zivid’s testing landscape. By adopting a number of WATS modules, Zivid focused on improving first-pass yield and addressing issues lowering the roll throughput yield. Live dashboards created transparency and helped cultivate a culture of awareness, allowing both the production team and operations to monitor and discuss yields daily.
With test sequences developed and deployed through WATS, the contract manufacturer needed minimal intervention to proceed, exemplifying an efficient and flawless workflow. Connection and execution time reports, along with product manager features such as defining groups and BOMs, helped facilitate analysis and repair reports for Zivid. The implementation of KPI targets with alarms and the addition of production equipment requiring maintenance or calibration to WATS also helped to enhance asset management.
The Results: Streamlined Testing That Scales with Growth
The implementation of WATS has been a catalyst for Zivid, significantly improving test management and the efficiency of assessing manufacturing performance. This strategic partnership has enabled Zivid to focus on the most important issues first, dramatically optimizing their production process. With WATS, Zivid has not only elevated its testing and calibration processes but also ensured these processes are scalable as their business grows.