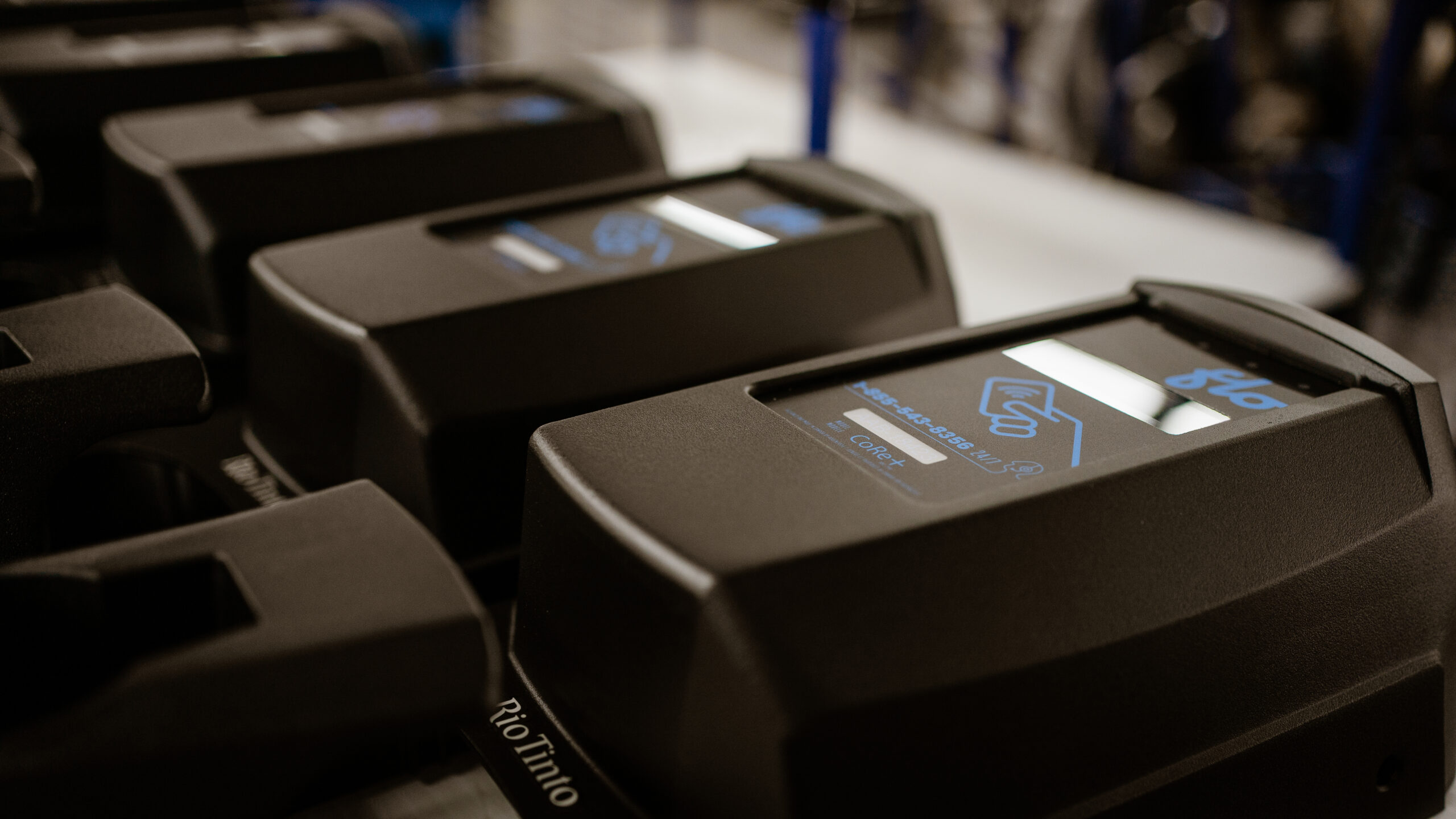
As a leading North American provider of electric vehicle (EV) charging solutions, FLO is dedicated to delivering high-quality, reliable chargers to support the shift toward sustainable transportation. With facilities in Canada and the U.S., FLO operates in a fast-paced, evolving industry where efficiency and traceability in production are critical.
To support its growing operations and meet increasing demand, FLO wanted to find better ways of working, so it turned to WATS. We spoke with Julien Pierrat, a Specialist in Manufacturing Systems, to learn how WATS has transformed FLO’s testing processes and improved production outcomes.
A need for greater traceability and insights
FLO has been on a rapid growth trajectory, continuing to introduce innovative products to further service its growing market share. But, with new product development comes new challenges – particularly in production testing. Staying on top of traceability, being able to identify failure points, and improving First Pass Yield (FPY) were top priorities.
Previously, FLO relied on Excel spreadsheets to track testing data, but this system had significant limitations. Only a handful of employees could access the data, making it difficult to gain a full picture of production performance and, as production scaled, the need for a more powerful and accessible data solution was clearly needed.
“Releasing a new product with a higher productivity rate was a very tough challenge, especially to identify the main improvement to do. This paradigm change required an easy-tracking and monitoring system. With WATS, it was easy to pick up the most relevant issues and fix an integration plan on our firmware and electric performance ”
Julien Pierrat, Specialist Manufacturing Systems, FLO
The WATS Solution
FLO implemented WATS in 2023 to enhance visibility across its manufacturing sites in Canada and suppliers. With WATS, FLO’s test data is now centralized and accessible to around 40 users – nearly half of the engineering team and direction.
This was a big leap from the handful of people who previously had access, and this shift has enabled a deeper understanding of test performance across multiple teams, leading to significant improvements across a variety of areas.
Key Outcomes:
- Greater traceability for all teams as they can now analyze test data at every stage of production, helping pinpoint recurring failure patterns and prioritize corrective actions.
- Improved R&D collaboration has meant that engineers working on printed circuit board assembly (PCBA) test benches now have clear visibility into testing outcomes, something that was previously lacking.
- Better manual inspections because of improved data capture means FLO has been able to refine manual inspection processes to catch defects earlier in production.
On top of that, WATS has helped FLO refine its internal data policies, meaning that more valuable insights can be extracted and leveraged across teams rather than information becoming siloed.
Transforming production performance
One of the most significant success stories from FLO’s WATS implementation is its impact on the production of FLO On chargers. As demand for these units surged, FLO had to increase daily production from 30 units to 150. But with that big spike in demand, initial FPY rates were only at 60% which wasn’t cost-effective or sustainable.
Increasing FPY from 60% to 90%
With WATS, FLO could quickly analyze failure trends in firmware and testing processes. This allowed the team to implement targeted improvements, increasing FPY from 60% to 85% – a huge jump for any manufacturer. The financial impact underlines how much WATS was able to help, with FLO reducing the weekly cost of failed FPY by around 70%. The company is now also on track to reach a 90% FPY.
Beyond FPY improvements, WATS has enabled FLO to refine its second-pass testing strategy, making re-testing more efficient and further compounding the value of the platform.
Looking ahead
FLO has been very positive about their experience using WATS so far, but the team is eager to explore more features, particularly in improving test functionality and further streamlining data collection. One area of focus is enhancing compatibility with TestStand to ensure seamless analysis of sub-units at the end of the production line.
As FLO continues to expand its footprint in the EV charging industry, WATS will remain a crucial tool in ensuring the company maintains its high standards of quality, efficiency, and innovation.
Learn more about FLO at flo.com