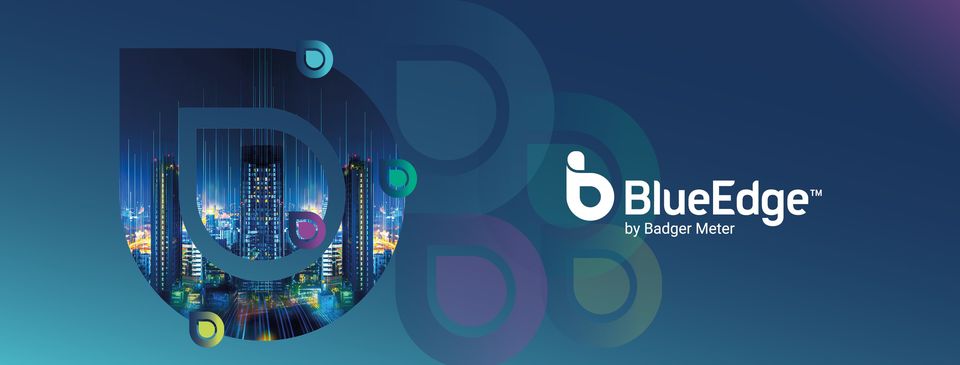
With more than a century of innovation and strong, stable growth, Badger Meter helps organizations around the world minimize the waste of one of the world’s most precious resources: water. They chose WATS to help them become even more data-driven, and since doing so have made their test processes even stronger. We sat down with Joe DeVries and Kenny Kreitzer from Badger Meter to get the full story.
Introducing Badger Meter
Badger Meter is an innovator in flow measurement, water quality, and control products; serving water utilities, municipalities, and commercial and industrial customers worldwide. Their smart water metering solutions provide actionable intelligence that enables customers to optimize the delivery and use of water, maximize revenue, and reduce waste. Badger Meter offers smart solutions for a wide range of customer applications through its global network of manufacturing facilities, including nine dedicated sites in North America alone.
“WATS has changed the conversations in the production department and across the wider team. As a result, everyone in the plant is smarter about how we operate. Delving deeper into the data was always the best approach, and WATS has been key in making that happen.“
Joe DeVries, Director of Operations, Badger Meter
Looking for Greater Access to Better Data
A few years ago, Badger Meter had a similar setup to many other leading manufacturers – great teams and modern production environments – but were now looking for an additional edge, and they had their eyes firmly set on data. They already had a suite of production dashboards that they had built internally, but they weren’t as streamlined or easy to use as they needed them to be. Seeing that having greater access to better data was key, they looked for a solution.
The Switch
In 2022, Badger Meter embarked on a trial with WATS, collaborating to post-process and import existing data into the WATS platform, while evaluating the potential benefits. Seeing immediate benefits from this initial work, by early 2023, they fully committed to WATS, marking a significant shift in their approach to a data-driven approach.
With nearly 100 testers now submitting data to WATS, including from some of their component manufacturers that operate abroad, test data has become significantly less fragmented and siloed. Now, there’s a single source of truth that doesn’t need a lot of manual work to arrive at and it’s easy to understand for every department.
“Being able to see the data in the way we now can helps us see issues we didn’t know we had. The same goes for communicating with component manufacturers because data is a language everyone can speak. The price you pay for the great service – paired with the limited effort you have to put in to get actionable data out – is much better than other solutions.”
Kenny Kreitzer, Principal Test Engineer, Badger Meter
Transformation and Growth
Joe and Kenny have seen firsthand the transformative impact of WATS on production at Badger Meter. In essence, WATS has simplified data access, analysis, and sharing. Now, production supervisors and planners have started using the dashboards in WATS to drive their decision-making. There’s been a cultural shift – one where the core five-person team of test engineers is now helping other teams make gains in their own areas of production.
The test engineers themselves get the most day-to-day benefit, logging into WATS every day to pull out the data they need. That includes analyzing data from their component manufacturers, who now have a way to feed test data back to Badger Meter – with no input needed from them. That helps conversations around testing happen much more quickly; using up-to-date information – a critical aspect of improving production.
“Instead of fighting through the same issues day after day in production, we now use WATS to understand the issues and develop countermeasures that truly address the root causes. As a result, we’ve seen tangible improvements in our outputs.”
Joe DeVries, Director of Operations, Badger Meter
The Next Steps
From a test perspective, Badger Meter wants to continue exploring features that they haven’t touched yet. A part they’re particularly interested in is the asset monitoring functions so they can improve maintenance performance on testers, as well as roll out WATS to more testers across their sites. Perhaps the best badge of honor from our work with Badger Meter is during the interview for this case study when asked for final thoughts, Joe said: “If Kenny needed to cut into planned production to give us greater insights out of WATS to improve our operation, he’d get it”. Now, if that’s not an endorsement, we don’t know what is.
Learn more about Badger Meter at badgermeter.com