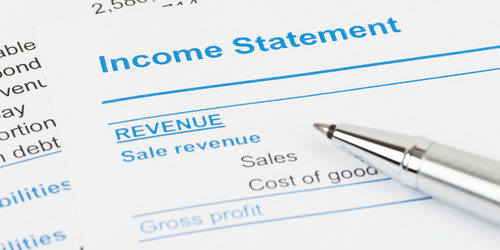
It is not unusual to consider the question of how to increase profits in manufacturing to be a problem for higher management. Leading you to accept that the ultimate objective of a Test Data Management for Electronics Manufacturing (MI) solution such as WATS, or Statistical Process Control (SPC) solution is to improve product quality. Or to improve internal efficiency in some areas.
Although this is not an entirely wrong assumption, it is not fully accurate.
At the end of the day, your company and you are likely in the business of building a long-term stream of profit. Both to pay back your lenders, owners and to invest in future growth opportunities.
In this post, we will look at MI from a higher perspective than what we usually do. And discuss how it has superior potential, compared to traditional methods such as SPC or in-house-developed data management tools, to increase profits in manufacturing.
And how MI provides critical support for your ability to continue product innovation.
We will use the traditional Income Statement to exemplify how this is achieved.
What is the Income Statement?
Before we go into WATS Manufacturing Intelligence details, let’s outline the main components of a simple Income Statement. Also known as Profit and Loss Statement.
First off, you have the Sales Revenue. This is the money from sales your company have made in the given period.
Cost of Goods Sold comes next. It tells what the actual costs associated with building these products were. If you subtract this from the revenue, you get the Gross Margin. The money you have available to pay for R&D, sales and marketing, corporate expenses, lenders and your owners.
Manufacturers often consider this Gross Margin number a Key Performance Indicator. Either as an absolute number or as a percentage of revenue. If the percentage drops, it might trigger serious consequences. If the percentage goes up, it can contribute significantly to increase profit in manufacturing.
Cost of Goods Sold has multiple sub-components. Variable Material Costs and Variable Labour Costs are typically directly related to the number of units sold.
Fixed Costs are typically manufacturing support staff and manufacturing management, equipment, factory expenses, and so on. Things that do not change within a certain range of units made. The depreciation of test systems is a relevant example of a fixed (at least semi-fixed) cost. You have invested in it to meet your needed throughput.
Non-manufacturing Expenses
Moving further down, you have Sales and Marketing costs. This obviously consists of salaries and promotional costs. But it also contains all the warranty claims that your customers have.
Next down the list are Research and Development expenses, followed by Administrative Overhead expenses. (Admin costs are often combined with sales expenses in a category called Sales, General and Admin Expenses)
The Gross Profit, less these expenses, give you the Profits Before Taxes.
If you are an accountant, you would probably say that far more details describe profits in manufacturing. And that is true. But then again, if you were you would probably not be reading the WATS Blog.
WATS MI in Action – Improve Profitability
With that background, how does WATS and Manufacturing Intelligence contribute to increasing Profits Before Tax?
“WATS customers have reported winning contracts with huge enterprises, that they claimed they never would have a chance to run for before adopting a WATS supported Continuous Improvement program”
Can you expect an increase in Revenue?
The impact Manufacturing Intelligence has on revenue is not a direct one. For some, it might be non-existing in the short term. There are two realistic scenarios to exemplify this. One is the impact improved product quality has on your brand recognition. This in turn impacts how well you are able to sell your products. The second, similar in nature, is the ability to win large contracts in the B2B market by having solid quality management policies. We have experienced this first hand. Where WATS customers reported winning contracts with huge enterprises that they reportedly never would have a chance to run for before adopting a WATS supported Continuous Improvement program.
How WATS helps improve Cost of Goods Sold
The impact on COGS is more tangible and direct. If you look at the Variable Material Cost, WATS will be directly contributing to this by helping you reduce the number of scrap units over time.
A significant portion of the Variable Labor Cost in today’s factories are test operators. We know from experience that retesting units are a common phenomenon. In fact, we have a calculator that lets you estimate how much money you spend on this.
WATS is a critical tool for any manufacturer looking to reduce this cost component as it helps inform you what the causes of these retests are. We have also written a more detailed post on product retesting.
Tools to address this includes traditional CPK analysis, also found in Statistical Process Control. But in WATS it assumes you start the analysis at a higher level than measurement analytics.
WATS also help expose several waste elements of Fixed Costs, in two primary ways. The first is that the manufacturing support and management staff have the necessary data to make effective decisions faster. They no longer have to perform as many tedious, manual exercises to get to the root of a problem. The second component is that you free up the bandwidth of your existing test systems by reducing the amount of retesting you do. So, as you scale up your volumes of units sold, you can delay investments in additional test systems.
Gross Profit
At a minimum, you can then expect an improvement in your Gross Profit Margin expressed as a percentage of revenue. As costs go down. It is also then plausible to expect that the total Gross Profit from manufacturing also will increase.
Sales and Marketing
Remember that Warranty Claims is a part of the Sales and Marketing cost center.
The same Continuous Improvement initiatives that reduce your scrap cost and retesting will also reduce factory escapes. Warranties can often be expensive. It is not only the units themselves that drive the cost. Shipments and RMA tickets must be handled, at times manufacturing itself must perform RMA analysis to document what was wrong. Sometimes you even lose a customer who was not happy with how things played out, which again impacts Revenue.
If you compare the framework for Manufacturing Intelligence that we advocate through WATS to traditional Statistical Process Control, the theoretical impact of the latter is in reality only aimed at this cost center. To stop defect units from leaving the factory. You can read this article explaining why Statistical Process Control is not suitable for monitoring electronics manufacturing.
Research & Development and Administrative Costs
This is a big cost center for many, with many different costs. Manufacturing support is one of the activities taking place here. This might be during New Product Introduction, or debugging problems happening during normal operations. It is common that R&D or Industrialization staff must travel to the factory to take part in these fault-finding projects. Often at different countries or continents than they normally work and live. Needless to say, these overhead costs can be significant.
Data-finding, sorting and analysis is also a common part of these activities. Manufacturing Intelligence aims to control this cost by providing real-time, unified and global data access. From anywhere in the world, you can access information on a specific incident that just happened. It helps reduce the time needed for data finding and has the potential to significantly reduce the resolution times. Often eliminating the need to travel. The real beauty however is that the system contains all the meta-data needed by different groups. So, it is a single source of data and insight, applicable to many stakeholders.
Effective Collaboration
This meta-data is critical for you to communicate in a “common language” internally. Or with sub-contractors. The same reasoning applies to admin staff working within this domain. The system provides them with business-level information to make faster and more effective and meaningful decisions. WATS for instance calculates many metrics useful for product costing analysis.
In summary
WATS and Manufacturing Intelligence applied to electronics manufacturing test data aims to provide you with a practical and complete framework to increase profits in manufacturing in the discussed areas. It differs from, and excels compared to traditional tools such as Statistical Process Control, in that its approach has economic thinking as a core element rather than limit itself to subsets of manufacturing problems.
The resulting improvements in profits add huge value to leading tech companies dependent on channelling money back into their R&D teams to keep up the innovation.