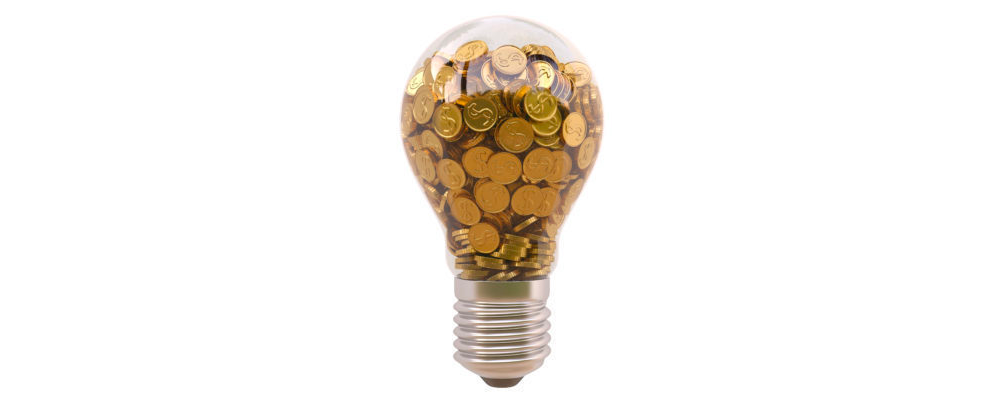
Maintaining a healthy cash flow to fund innovation is increasingly important as new technologies continue disrupting the status quo.
So, how much of your R&D budget do you think is actually spent on innovation? And how can you effectively increase this?
What is the Innovation Budget and why does it matter?
To set the stage, the Innovation Budget does not equal the R&D Budget. It is not even a real budget. It is a virtual one, representing how much money is available for true product innovation.

Think about the R&D spending that many companies promote. It is not uncommon with budgets of 10-20% of total revenues. However, the reality is that far from all this money is invested in innovation. But in a myriad of different costs that may or may not positively impact the company’s future sustainability.
The goal is not to spend money on the R&D organization but to spend them on actual Research and Development. Simply because this is what generates new ideas and products where the real future comes from.
So, to avoid confusion, we will refer to this spending as the Innovation Budget.
How does Manufacturing Intelligence contribute to the Innovation Budget?
There are many available levers to Increase the Innovation Budget For Electronics Manufacturers, one important lever is Manufacturing Intelligence (MI). It is a well-proven framework that will allow you to reduce costs associated with data management, various kinds of debugging, manufacturing labour, warranty claims, quality issues, and many more.
To explain how Manufacturing Intelligence can increase your innovation budget, we will use a simplified financial report for a fictive company. ACME Inc.
We will look at how TDM helps the individual cost categories in ACME in both the short and long term.
ACME has an annual financial statement that is very simplified, looks like this
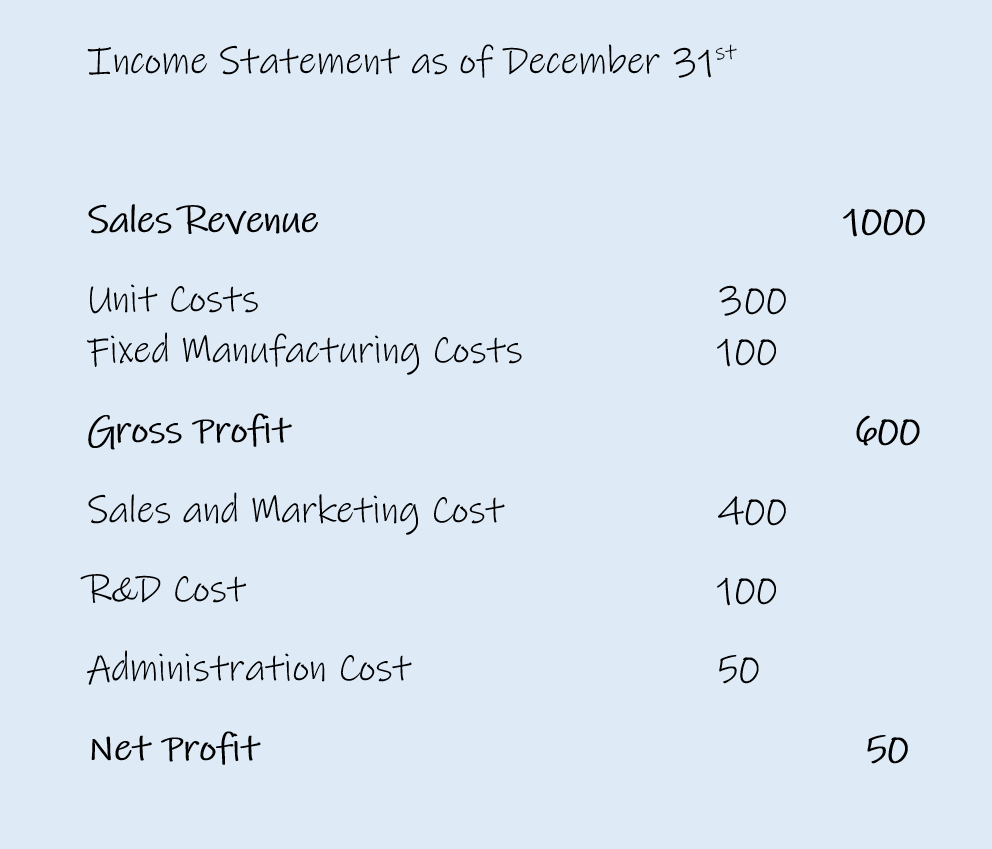
The R&D expenses are on a budget at 10% of the revenue. An R&D target is quite common for companies in the technology sector. But if we break the R&D costs down into more granular cost items, many non-innovation items will appear.
Some relevant contributors to the ACME R&D spending
R&D expenses in this example include salaries for ten people, representing 90% of the total R&D costs.
The remaining 10% is 2 in miscellaneous equipment costs and 8 for travel expenses.
Five out of the ten people in R&D spend roughly two days each per month on manufacturing data-finding and debugging activities. Meaning that the salary-cost related to manufacturing performance assistance is also 8.
Now, you obviously would not cut this cost. But you can shift these resources into other high-value activities. Activities included in the Innovation Budget.
Generalizing R&D expenses and the Innovation Budget
In fact, NPI/Manufacturing debugging activities and associated travel expenses represent some very common R&D costs.
If we break down the proposed R&D expenses into more details, a likely scenario would look something like this:
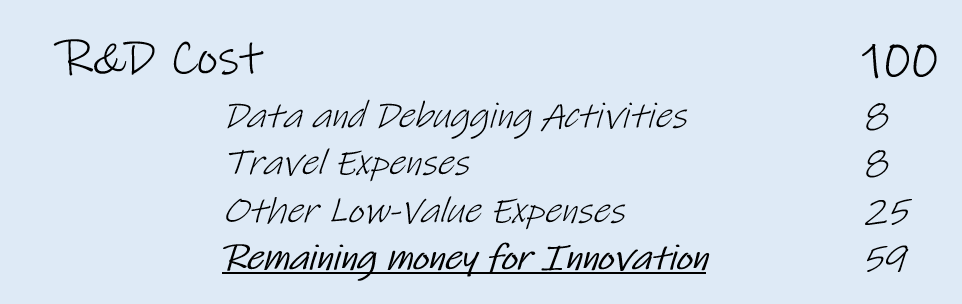
As we can see, ACME’s real R&D Innovation Budget is not 10% of revenue. It is 5.9%.
And there are some of these very common R&D expenses that WATS and Manufacturing Intelligence can significantly impact. You likely guessed it already: data-finding, manufacturing debugging and travel expenses.
A key reason for this is that the data becomes easily available. When problems occur, there is no need for a rigorous data-finding project. The data is already easily available. And the native analytics can quickly help you form a hypothesis of what is causing the issue.
And when a problem appears at a factory in a different country, the data is still easily available. You don’t need to physically travel there to help find out what the cause is.
The factory also has access to the same data and reports. In other words, your ability to collaborate remotely skyrockets.
Reducing R&D Costs in ACME
Let us say that you can reduce these costs by 50%. A reduction that is far from unachievable. This means that you free up these 8 for innovative, high-value activities. So, your available Innovation Budget goes up from 59 to 67 (or from 5.9% of revenue to 6.7%).
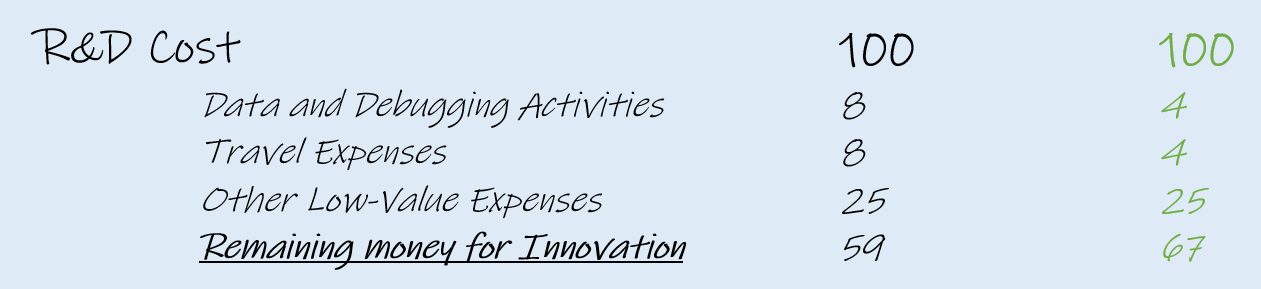
We have amended the short-term effects of WATS as an alternative budget, highlighted in green.
This is an increase of 13,5% from something as simple as having access to data. The extra money is fully accessible by the R&D organization since it already belongs to their budget.
But there are far more short-term savings available than just these. In other words, the potential to increase the innovation budget even further. We just got to raise our focus outside of R&D.
To make the comparison easier, we’ll assume that the proposed alternative budgets (numbers still highlighted in green ) are alternative “today” scenarios. As if ACME had been using WATS Manufacturing Intelligence for a short or longer period.
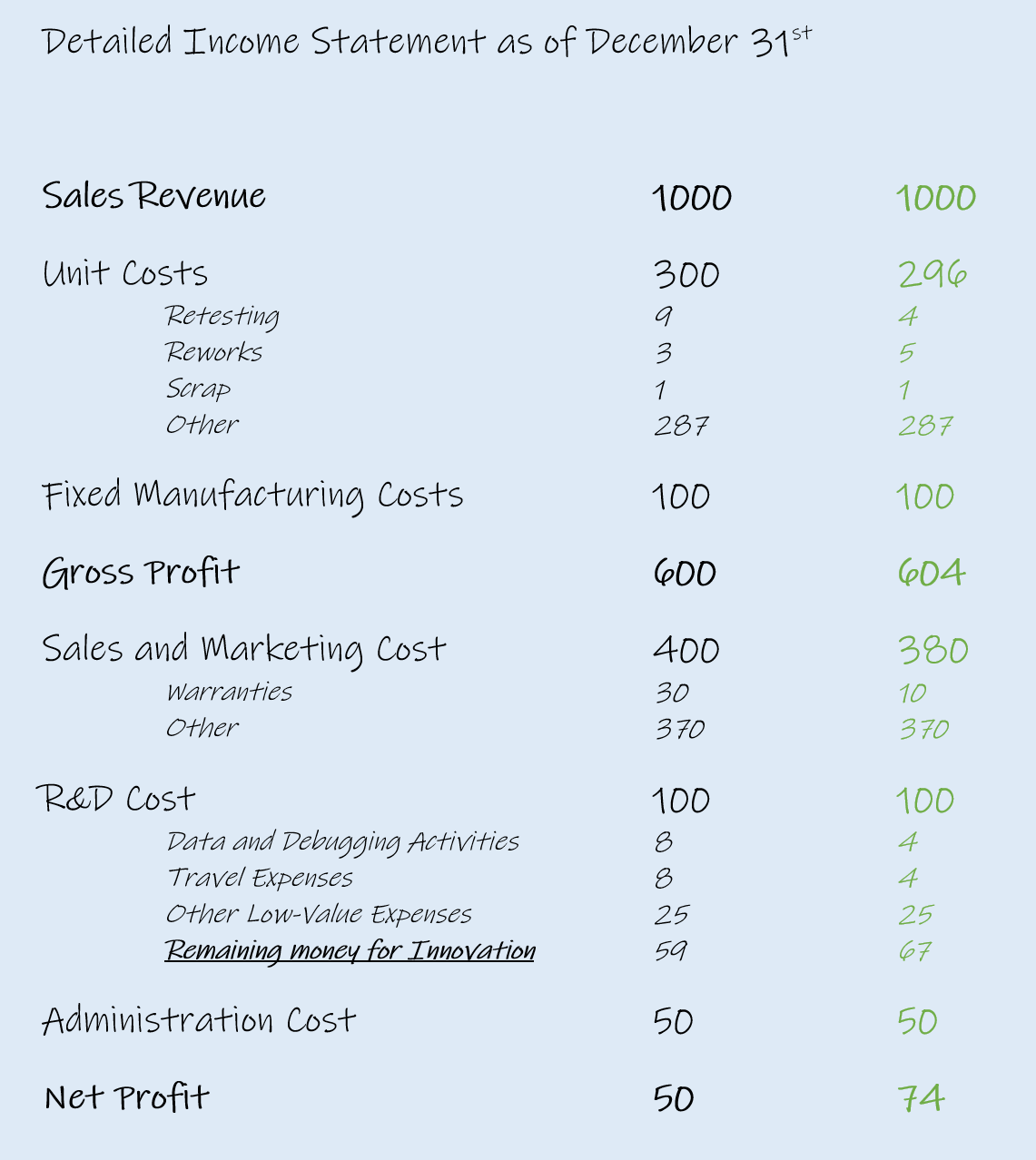
Accessing Saving from other parts of the organization
If R&D management in ACME plays their cards right, the increase in the Innovation Budget can far exceed the “local” savings from R&D.
Why?
Because the impact of Manufacturing Intelligence is far greater and touches on sales and manufacturing expenses as well.
Why R&D budget is a “leftover” budget
To better understand how these other savings help contributes, it is important to point out that the money available for R&D is typical “leftovers” from after normal operating activities (sales, manufacturing) has been paid, and the owners and banks have gotten their share. It is a somewhat simplified allocation model. But it is at least reasonably accurate in the longer run.
Payments to the owners and banks will likely not change significantly from increases in profit. At least if your company has good financial governance and strategic vision. In other words, savings from manufacturing and sales can be passed on to R&D. Inside R&D, the non-innovative overhead costs should not change much based on additional money becoming available. So, the added money can go directly into the Innovation Budget.
That is the theory at least. It is perhaps not very likely that sales management will be willing to give up on their total budget just because warranties go down. Or that manufacturing management is willing to take a cut because test failures decrease, and the first-pass yield goes up.
So if R&D wants to get money from other groups, you need to have awareness of how these other costs can go down. And use this to build your case for an increased budget from the start of the Manufacturing Intelligence implementation.
Add savings from Warranty Claims to the Innovation Budget
Warranty is a cost from under Sales and Marketing. In the example above, the warranty claims have been reduced from 30 to 10 simply by improving the test coverage during manufacturing. No improvements in design or the manufacturing process have taken place yet.
You would likely be surprised how many tests are far too forgiving to catch most of actual failures.
But improved test coverage does not deal with the underlying issue that something likely went wrong during the manufacturing process. Either a design flaw or a build issue. Therefore it is not unreasonable to expect that the scrap and rework costs in manufacturing will increase slightly because of this.
The “10X Cost Rule” indicates that the cost of detecting these failures at the latest stage in manufacturing is 1/10 of the alternative warranty cost. So, if the warranty cost goes down by 20, then manufacturing cost can increase by up to 2 in the short term. It would likely be less, as test coverage would be improved throughout the entire process, and some failures would be caught earlier.
Changes in Manufacturing Costs
The example we’ll show covers three basic costs and activities for Manufacturing.
Retesting, reworks and scrap.
In the short term, getting a better understanding of the primary causes of test failures will help you to avoid most of unnecessary retests. The kind of retests that comes from something as simple as a test limit not being changed for a new product revision where the relevant component has slightly different characteristics. Fixing this can also help reduce the cost of the rework as the number of No Failure Found repairs goes down.
As mentioned earlier, the cost of scrap and real reworks might increase slightly because you get better test coverage. In the long run, you will better understand the underlying causes of these failures. Meaning that both scrap and rework costs go down.
The actual increase in available Innovation Budget
As the example shows, the short-term impact of Manufacturing Intelligence was a 13.5% increase in the R&D Innovation Budget. From local savings. And an increase in company earnings of approximately 50%. But if we assume that the 5% profit margin (profit of 50 from revenue of 1000) was the target, company management will likely calibrate the strategic expenditures to this target.
And what is more strategic than innovation?
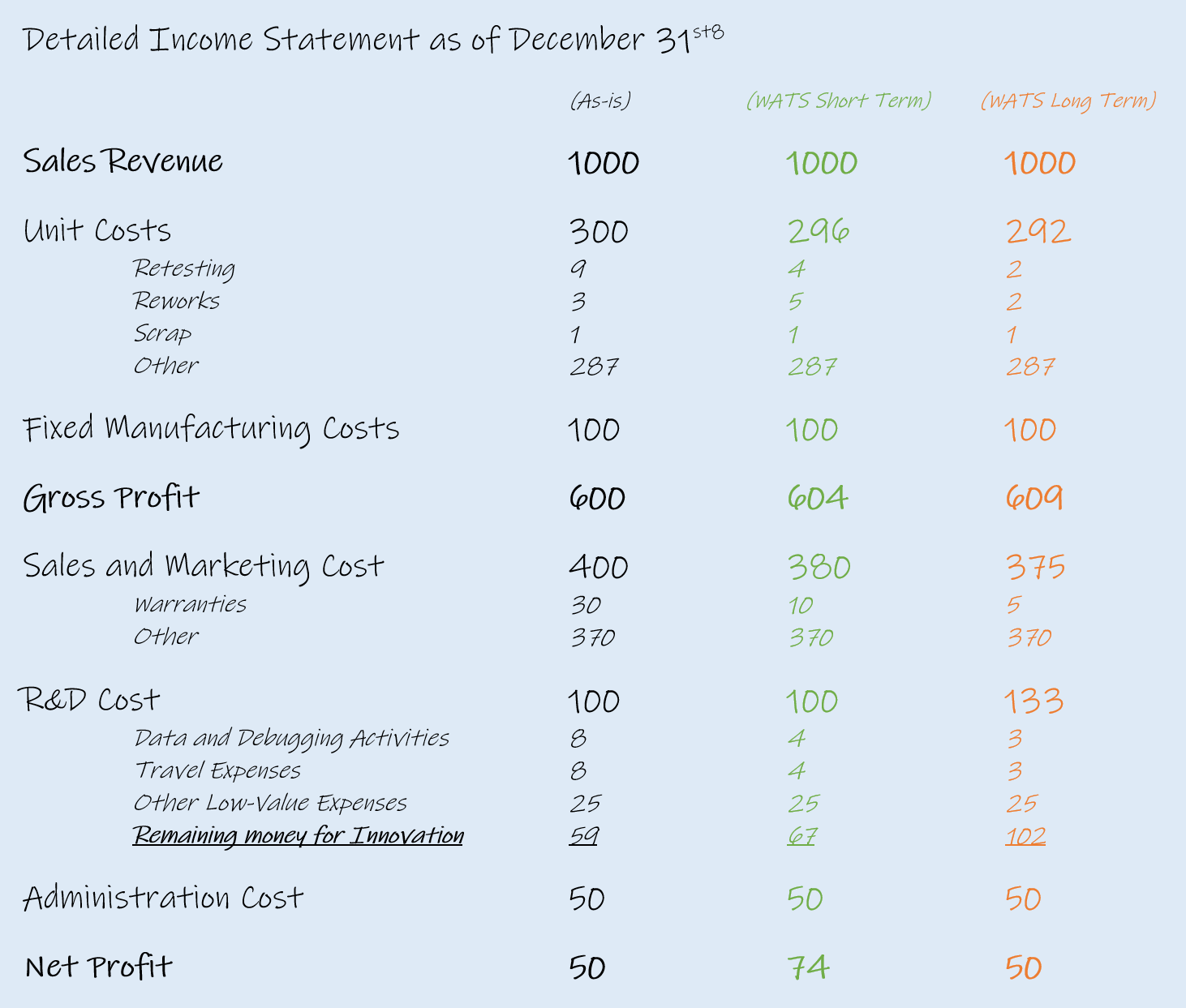
We have amended the longer-term effects of WATS as an alternative shown in orange.
So, in the long run, ACME will experience a gain of 43 from the Manufacturing Intelligence initiative. Eight from Manufacturing, 25 from Sales & Marketing, and ten from R&D.
If this money is channelled back into R&D without causing an increase in low-value activities, the money available for innovation will increase from 59 to 102.
That is an increase of nearly 75%!
In reality, the real gain from WATS in this example would be higher. There are other savings not addressed here to avoid the example becoming too complex. Such as Manufacturing Overhead, Test Asset Utilization, and Admin Costs, to name a few.
Translating this example to the real world
At the end of the day, this Innovation Budget example is a play with numbers. Several potentially relevant factors have been simplified or left out.
All the money would likely not be re-invested in R&D. Rest assured that Sales and Marketing would ask for their share of the pie. Reducing headcounts in Manufacturing might not be possible. At least if you operate your own factories.
But the savings are still there.
What if only one-third of these new savings from sales and manufacturing went back to R&D? That would give you a short-term boost for innovation of 13.5% and a long-term boost of more than 30%.
And a 30% increase in innovation capacity might very well be what takes your company to the next level. Or what one day will save you from bankruptcy.