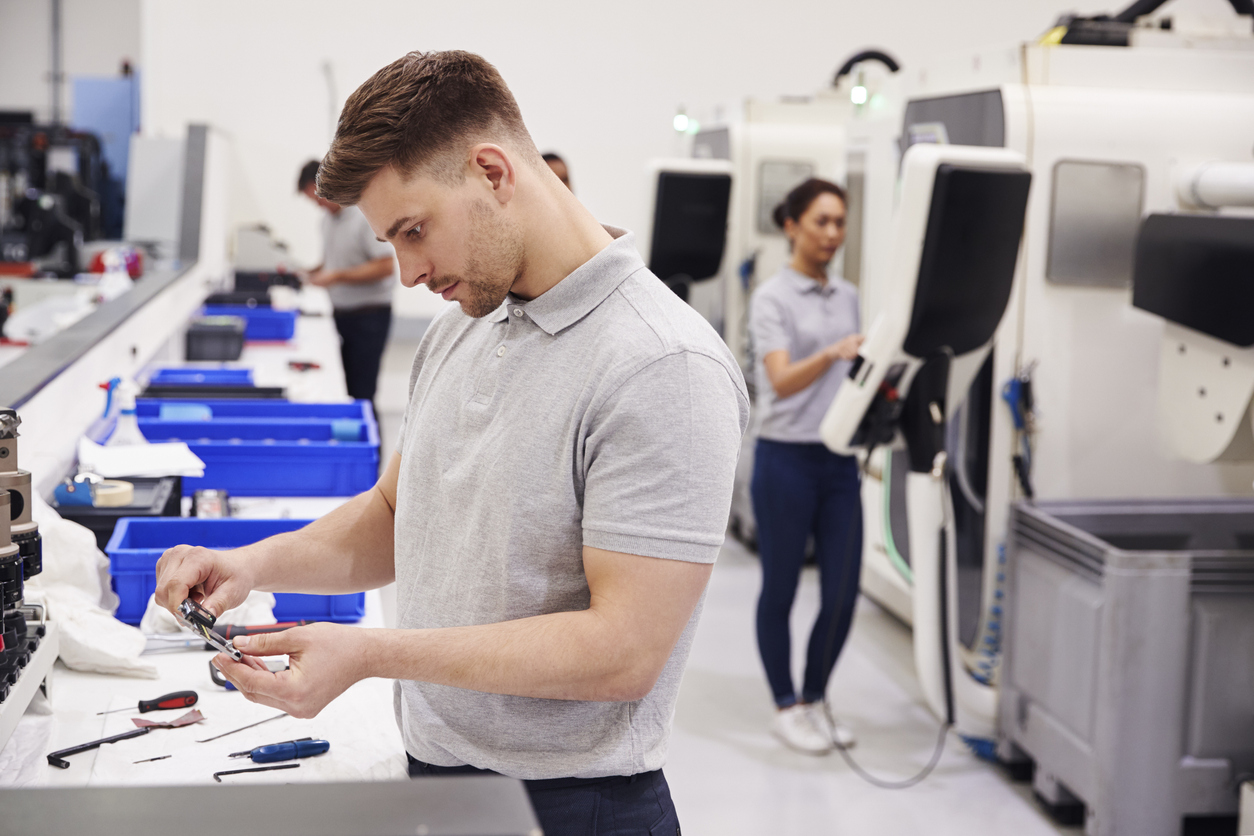
Production issues aren’t just costly mistakes. Their wider ramifications can topple even the biggest giants. Remember Takata Airbags? The business went bankrupt over a flaw in airbag production, causing tens of millions of vehicles with their product to be retracted.
Whatever you’re building, constant testing and inspection is essential. You need to ensure your production line delivers the way it should. The test process, even for smaller components, has to be precise.
This is why standard automated tests are so useful. They provide in-circuit testing and automated optical inspection; as well as PCBA, module, and system level testing. They’re also evidence of how well-oiled your production flow is. After that, the formal evaluation can begin to determine product viability.
However, many manufacturers still perform inspection tests manually. Not only that, but they record the data in the same way – using a static Excel spreadsheet or good old-fashioned pen and paper.
They’re clearly missing a trick by doing so.
Data From Manual Inspection should be easily accessible
Often products will go through dozens of manual checkpoints. But once complete, the data gets forgotten. It remains hidden – most likely never to be used again. This is a huge mistake. Data kept in isolation is worthless. When it’s combined with other sets, so much more becomes apparent.
For example, if you’re making blue LED lights and some turn-up green. OK, great, there’s a documented fault. But what if 3% of all the manual inspections detect an issue with the LEDs? There may be issues with your PBC board – but to find out, you need a way to go back and see exactly where things went wrong with these units.
Automated Testing Streamlines Processes
Bringing together accurate testing and manual inspection data in a system like WATS, gives you a holistic view of information from all sources – including all of the faults and the correlations between them. This overview gives you the ultimate foundation to maximize yield, gauge productivity, and run with proficiency.
Finding faults early in the process is also critical. The further down the line a failure is identified, the cost increases tenfold. With a proper analytics system in place, you can discover upstream faults before they cost money – and better understand where things went wrong.
Rather than risking human failure in manual inspections, digitized inspection sequences also bring you accurate and consistent results you can trust.
With full data accessibility, you no longer have to search for what you want endlessly. WATS lets you see the exact process every product went through, including all workflow stages. Scan the product bar code and see its entire journey – all information is there, ready for you to streamline your operations.
Manual Inspection Module in WATS
The Manual Inspection Module in WATS features a sequence builder where you can graphically design the test flow, along with a web interface that guides the test operator through all the necessary steps. All history of manual testing is thus collected in the same system, in an easily accessible format.
Learn more about the Manual Inspection Module