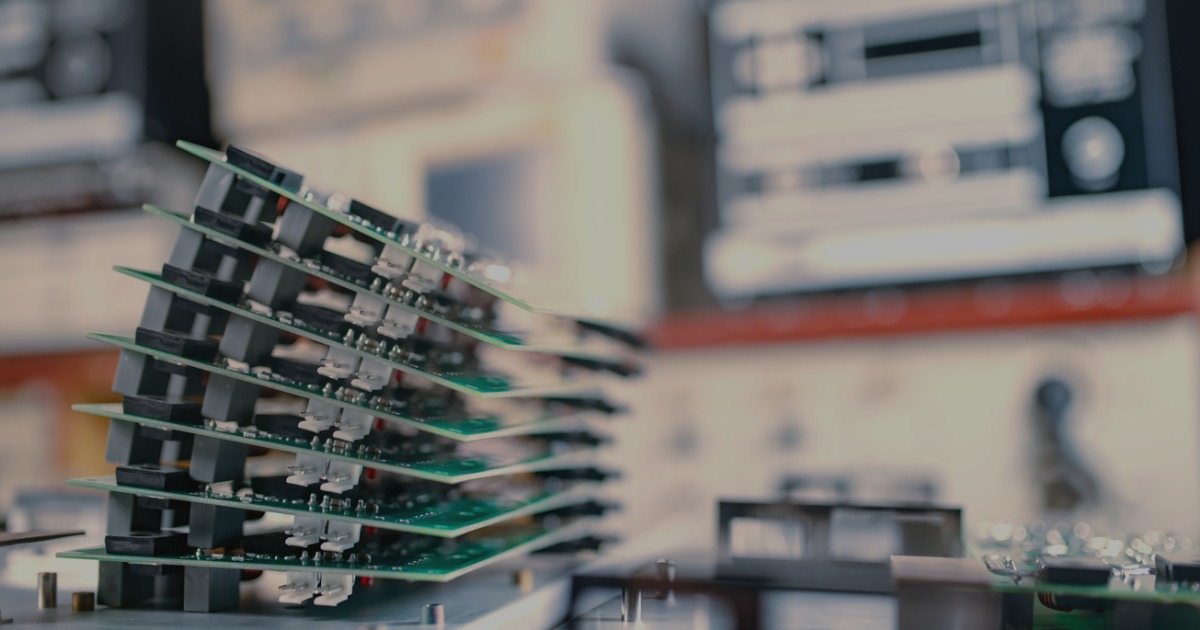
This article describes why many electronics products are retested repeatedly during a typical manufacturing flow and some problems associated with this behavior.
It also serves as an introduction to our Retest Cost Calculator, which will provide you with a ballpark estimate for the costs that go into retesting, and how it relates to unit costs and affects test system utilization or throughput.
Finally, we show you how you can use the WATS Cost Analysis Tool to estimate and monitor your cost of retesting.
Is retesting a problem?
It is a well-established fact that most electronics manufacturing companies retest their products more than what is ideal. It is a very familiar scenario for companies with outsourced manufacturing but also for OEM companies with in-house manufacturing. Unfortunately, it is also a problem that also is almost invisible.
One of the use cases of Test Data Management for Electronics Manufacturing is to make these occurrences and trends explicit. So that you can use this data to make informed decisions.
We have seen many new customers uncover and reduce re-testing cost within the first months of using WATS, some even in the trial period. Due to improved and real-time access to their test data.
The consequences of retesting
The consequence of retesting is both expensive and potentially damaging. Excessive retesting represents two overall problems on a spectrum from less severe to more severe:
Overall Problems with Retesting:
- Reduced test asset utilization
- Increased cost
- Quality implications
On the less severe end of the spectrum, the only consequence of retesting a product is that it takes time and steals bandwidth from the test throughput. It could be something as simple as the test operators’ impression that the test system itself is the source of the problems. If a test fails, it is only natural to test it repeatedly. Hoping that whatever problem they suspect will ease off.
Maybe the test limits are sat incorrect, and the average measurements are operating very close to one of the limits. Perhaps the operator suspects that there is poor connectivity from the test interface board, so he or she applies some force to the board. A trick they have picked up over the years has worked many times before. And behold, the product passes the test. Ready to move to the next stage. Or out to the customer.
When retesting becomes concerning
You will find the exact same scenario on the more severe end of the spectrum. The product is failing. All of the accumulated experience of the test operator says that this is because of the test system. Retesting it is the obvious action to that. And again. And again. Apply some pressure, then test again.
The problem now though is that there is nothing wrong with the connectivity of the interface board. It is one of the capacitors that is not properly connected. As the test operator applies pressure to the system, the capacitance reaches just the right value to allow the unit to pass.
You would think that these scenarios are rare. You might think that the operators can distinguish between a faulty unit and a poor test system.
Our experience, working with several industry-leading companies in this sector is that this is far from rare. It happens all over the place, from high volume consumer electronics to FDA regulated products. They lack the insight provided by the Retesting Chart found in WATS. They simply lack the necessary data to bring the problem into the light.
You could think that implementing Forced Routing will fix this. But unless you have good control of your test systems accuracy you are likely to be wrong.
How to Calculate the Cost of Your Retesting
The cost of retesting is an important metric in test data management and knowing your cost of retesting is vital if you want to improve. We introduce you to two ways of estimating this, one for non-users of WATS and the other one with the use of WATS:
- Use our Retest Cost Calculator
- Use WATS Cost Analysis Tool
Retest Cost Calculator
If you are a non-user of WATS you can check out our Retest Cost Calculator. This tool provides a ballpark estimate for the costs involved in retesting and illustrates how these costs impact unit costs and affect test system utilization or throughput.
WATS Cost Analysis Tool
Another way to find out the cost of your retesting is to use WATS to get a real-time overview of your retest costs. With our Cost Analysis tool, you get the estimated cost based on your actual manufacturing data. WATS users can constantly monitor their cost of retesting and see how they improve.
How to Fix and Transform a Retesting Culture
Fortunately, though, the two sides of the severity spectrum are very entangled. In simple terms, the common behavior is a tendency to deploy manufacturing test systems and not continuously optimize their accuracy. This in turn allows this undesired culture to manifest.
New Product Introduction is a golden opportunity to make this improvement, to ensure that your limits are well suited to the actual unit specification. But before the high volumes kick in. Before your focus shifts to other product releases.
In our top-down approach to quality assurance, the natural tool for this set of problems starts with Process Capability Analysis. In an early stage.
- Make sure that you don’t have big rooms for measurement outliers.
- That your measurements are not clustered towards one of the limits.
- And that when a product fails the test it is most likely a product issue.
Only then can you make sure that you have solid grounds to kill the retesting culture and stay ahead of the curve.
How to Reduce Retesting
The cost of retesting is a time-intensive task that often is representative of 10-30% of the total time spent testing. The impact is reduced test asset utilization. You might need to add new testers as you increase output volumes, and it takes a paid employee to operate the tester. Test equipment often comes at a high cost, so there is no need to say that reducing re-testing is a good business case.
A specific Test Data Management benefit from WATS is that you can address retesting in two ways. First, you have full visibility into how many retests your products have. You can drill down and dissect this data as you need, to figure out what is the likely reason. If you collect repair data, you can cross-correlate these. You can even receive automated notifications if products are retested more than a threshold.
Second, WATS also features a Software Distribution Module. You can use this to centralize the distribution of software and firmware packages. So that when a test initiates it checks the latest version on the server against what it is running. If it is outdated, the operator can choose to upgrade directly.
If you suspect that extensive retesting is a problem in your organization, make sure to sign up for a free trial to see what your test data looks like.