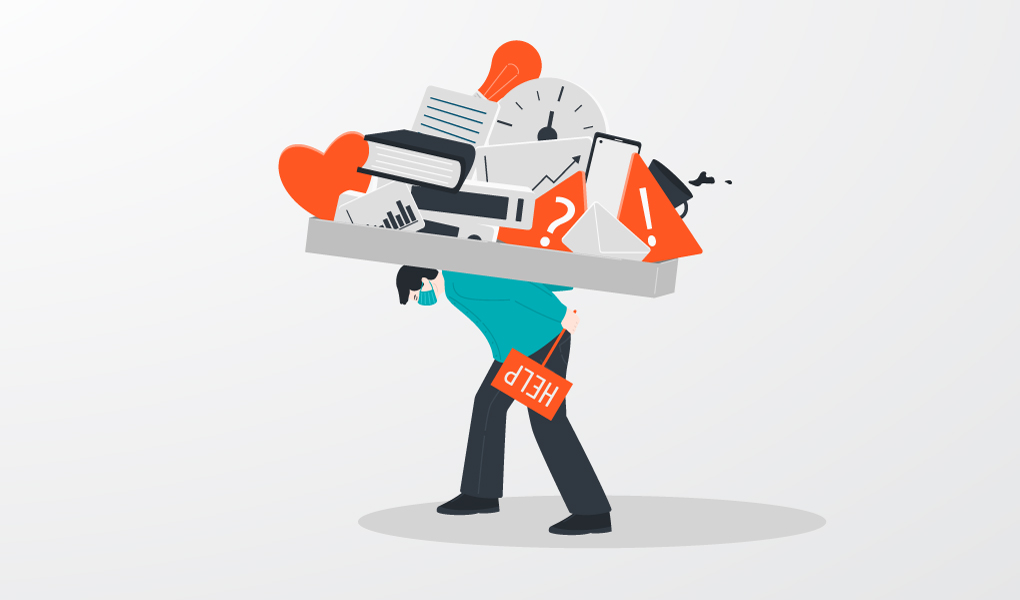
Statistical Process Control (SPC) is great for basic products. But for complex electrical manufacturing, it doesn’t cut it and could cost you time and money.
There is no one-size-fits-all when it comes to creating a test environment. Whatever you create needs to give you the right data. That data is going to give your business insight which it can use to make better decisions – saving time and money. Focusing on irrelevant, or even incorrect data is a trap that many companies fall into – but there is a better way.
Information Overload
SPC is still found in continuous manufacturing processes and is used to calculate control limits and find misordered process parameters. But it’s a set of controls that don’t meet the complex demands of modern electrical manufacturing.
If you’re using statistical process control in order to find problems in electronics manufacturing, then because of the complexity of what you are making and all of the factors that impact it there are going to be trends, alerts, and warnings on every data set that you look at that will cloud what you really need to see.
Let’s use a simple example, if one of your tests brings back fail and it’s clear that it was a component fault, you swap it out and retest. The problems start when it fails again because so many other factors could be causing the issue. Temperature, humidity, different machine operators, and test equipment calibration all impact electrical manufacturing and testing. It could even be on a software level there have been updates that impact reporting.
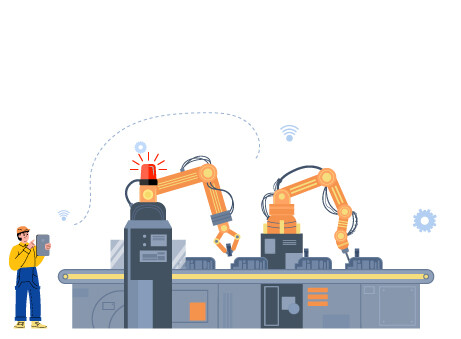
The point is that you need test data that you can trust and take action on. If you’re told something is wrong incorrectly at every stage of testing, eventually your testers are just going to ignore the notifications they receive – they’ll be desensitized to them. When you’re producing at scale, it takes too much time to look into each and every issue if they’re reported more often than needed, and this can also cause backlogs in testing.
Knowing What’s Important
Some manufacturers limit what they investigate to an arbitrary number of key performance indicators (KPIs), such as power output, response time, bandwidth etc. These are key measurements of how well the product is working, but because only a handful of existing tests have been chosen, you’ve thrown away a heap of other information. If you’ve done that to make the number of errors you receive more manageable, you’re potentially ignoring faults elsewhere in the testing process.
Beyond ignoring data creating too much noise, it also means you can mistake one result for another. Perhaps you have an alert that goes off for one test procedure to advise it’s over the set threshold. You need to answer, “why is that happening?”. The problem you have by stripping your results down is that now you can only see results through that one lens.
What you really need is a test data solution that shows you all the right information at all times – that’s what WATS is for.
Need a test data solution you can trust? Look no further than WATS.
Book a Demo to see WATS in action
Subscribe our Newsletters
Don´t miss any of our articles.