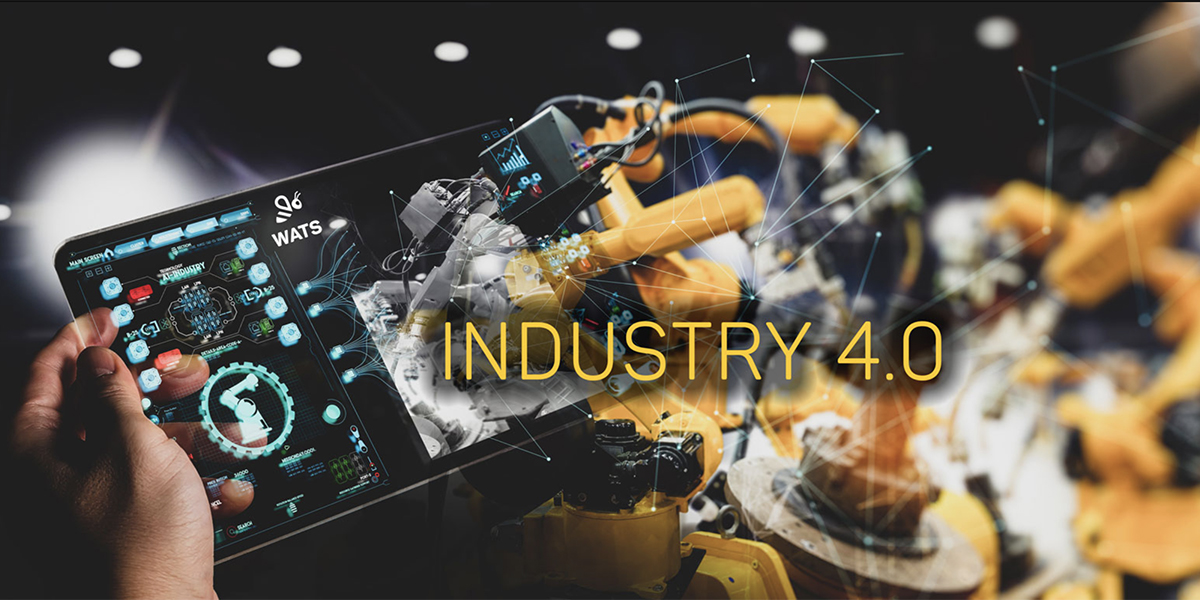
Have you pushed the re-set button on your life and business? The global pandemic has given many pause for thought, but no one can stand still in today’s highly competitive world.
This century has not only ushered in the dramatic results of climate change (negative) and disruptive technology (largely positive), but witnessed the dawn of the 4th Industrial Age – more often dubbed as Industry 4.0.
Of course, the challenge with terms that so often slide into careless use as buzzwords is that they can be interpreted depending upon your definition, and they can potentially become a shortcut to those who wish to pay lip service to the next big thing in the global business scene.
But Industry 4.0 is no buzzword.
Defining Industry 4.0
So, what’s the definition of Industry 4.0 and what should we do with it? Why is it important?
4.0 is the digital transformation of manufacturing/production and related industries and value creation processes. As the saying goes, you’ve got to be in it to win it, but before we dive into Industry 4.0, it makes sense to understand the evolutionary steps marked by industry 1.0, 2.0, and 3.0.
- Industry 1.0: The first industrial revolution happened between the late 1700s and early 1800s and involved the use of water power and the invention of the steam engine to replace manual labour.
- Industry 2.0: In the early part of the 20th century, the world entered a second industrial revolution with the introduction of steel and use of electricity in factories, and invention of assembly line and mass production.
- Industry 3.0: Starting in the late 1950s, a third industrial revolution slowly began to emerge, as manufacturers began incorporating more electronic – and eventually computer – technology into their factories, with early stage automation and increasing reliance on computer programmers and engineers.
- Industry 4.0: This is all about connectivity. It focuses heavily on interconnectivity, automation, machine learning, and real-time data and is also sometimes referred to as IIoT (Industrial Internet of Things) or smart manufacturing. Pretty much all machinery is interconnected using IOT network protocols, sensors and control mechanisms that talk to each other.
All Devices Should Be Able To Communicate With Each Other
At WATS, we see ourselves as an integral part of this transformation of industry. We connect the test station to enterprise data networks – data, calculations, bringing information forward automatically. With the information we provide, business leaders can make better informed decisions.
But, admittedly, the tech needed to make broad automation work is still in its infancy. The networks need to be in place and all devices need to be able to connect to the same networks to share data. Also, functions and measurements from different devices need to be able to send the same information in a standardised way.
Our Customers Want Choice & Multiple Systems
Integration depends on letting other devices integrate with other systems. WATS allows this through a REST API – an architectural style and approach to communications often used in web services development. This means that other systems can query us and can authenticate the system to access a specific type of information.
There may be some resistance for companies to embrace interoperability and free access but in our experience – a few years ago – whilst you could get everything from the same vendor, this tied users into exclusive and tied relationships which could prove to be an expensive route.
Now we’re seeing that our customers want choice, and multiple systems with the right information already made available off the shelf. That’s why they use WATS, and if necessary we can integrate into any other software.
Trying to do everything yourself will cost a lot of time and money. Trust the experts to figure out the calculation. The infrastructure is there. The data is there. The software is being developed and manufacturing companies just need the technology to extract it.
That’s what WATS can do – and can also embed machine learning and rules to follow. AI technology can predict machine failures, schedule preventative maintenance, and much more. That’s the promise of Industry 4.0 promises, and we’re proud have a role in helping to develop those intelligent systems.
You don’t have to have everything on one system – you can achieve a faster result through interconnected devices, helping to future-proof decisions and business operations.
Curious to learn more about Industry 4.0? Drop us an email and we’ll be glad to explain how WATS is leading the way!
Sign Up Today for your free trial
Discover what WATS can do for your testing and manufacturing processes.