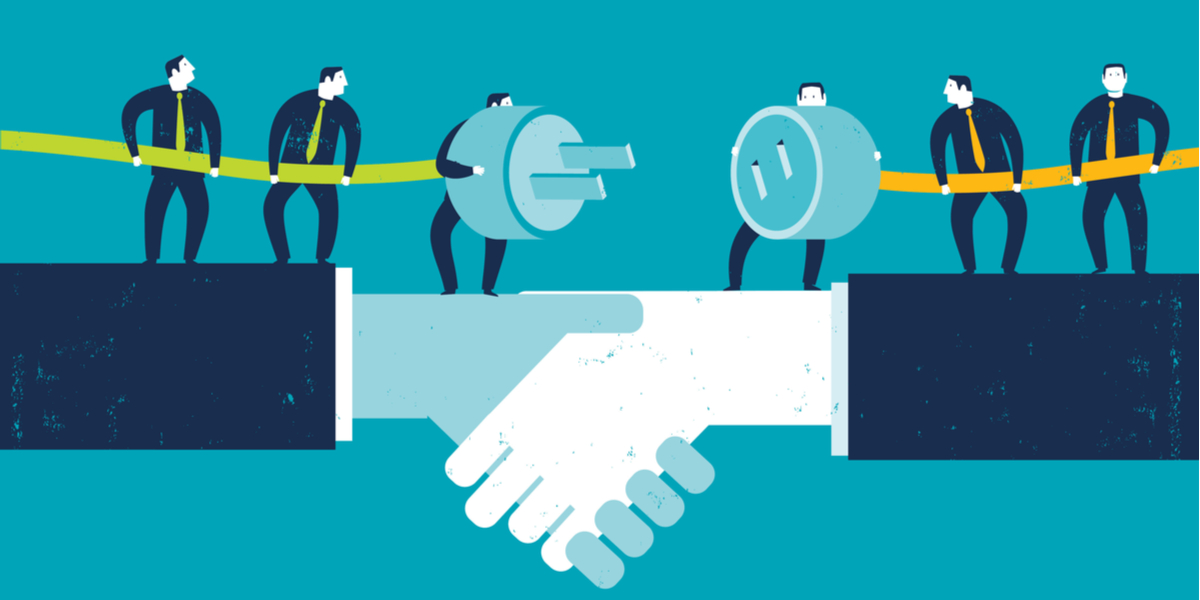
Many companies believe they don’t need real-time test data from their subcontractors because, as they’re paying for something, they expect it to be perfect in terms of quality. However, as the product owner, they are ultimately responsible for the quality and so seeing subcontractor test data helps meet customer expectations as well as save time and money.
Mistakes Are Expensive
The common argument we hear from manufacturers is that “we’re paying a subcontractor so they should take care of everything, we don’t want to spend time managing their testing.” But that’s a flawed argument. If they spend 3 months doing extra work because there are issues, you (as the purchaser) will still get the bill, or at the very least you’ll cause problems for your own customer.
Every manufacturer should be interested, and invested, in setting quality standards for the components and assemblies they are subcontractor manufacturing. Retesting is expensive too so test equipment should be maintained to a schedule and correctly calibrated. It could even be that the firmware you are installing on a product you purchase is impacting its quality. In this case, you need to have ways of communicating with your supplier and seeing their test data before the product arrives with you.
If there are quality issues with a product a manufacturer can’t point their customer in the direction of the subcontractor responsible – they have to take responsibility themselves. Quality issues reduce the chance of repeat business and generally just damage the reputation, so avoiding them at all costs is crucial for business survival. Because of that, it just makes sense to measure quality at every stage of a product’s construction and that includes each assembly that goes into it.
Relationship Building
So far we’ve spoken about catching issues through testing – but this isn’t about pointing the finger at your subcontractors. WATS is a platform that gives everyone the visibility over test data that they need – that includes subcontractors. When everyone understands the facts it creates a much better space for discussion and issue resolution. Ultimately, WATS helps to facilitate these discussions.
Sometimes the pushback of getting a subcontractor onboard with sharing test data is the cost of implementation and who is going to foot the bill. But Implementing WATS isn’t a big deal for subcontractors because setting them up to communicate with your installation is relatively simple.
It might sound a little strange but real-time access to test data can actually help build relationships between manufacturers and their subcontractors. Most B2B relationships break down either due to cost or quality, both of which WATS helps you improve. The relationship between a manufacturer and their subcontractors is an important one because the better they work together, the better the product, and this all helps the end-user experience.
Do you want to work with your subcontractors to create better products? It starts with WATS – contact us today.
Book a Demo to see WATS in action
Subscribe our Newsletters
Get updates on Test Data Management for Electronics Manufacturing.