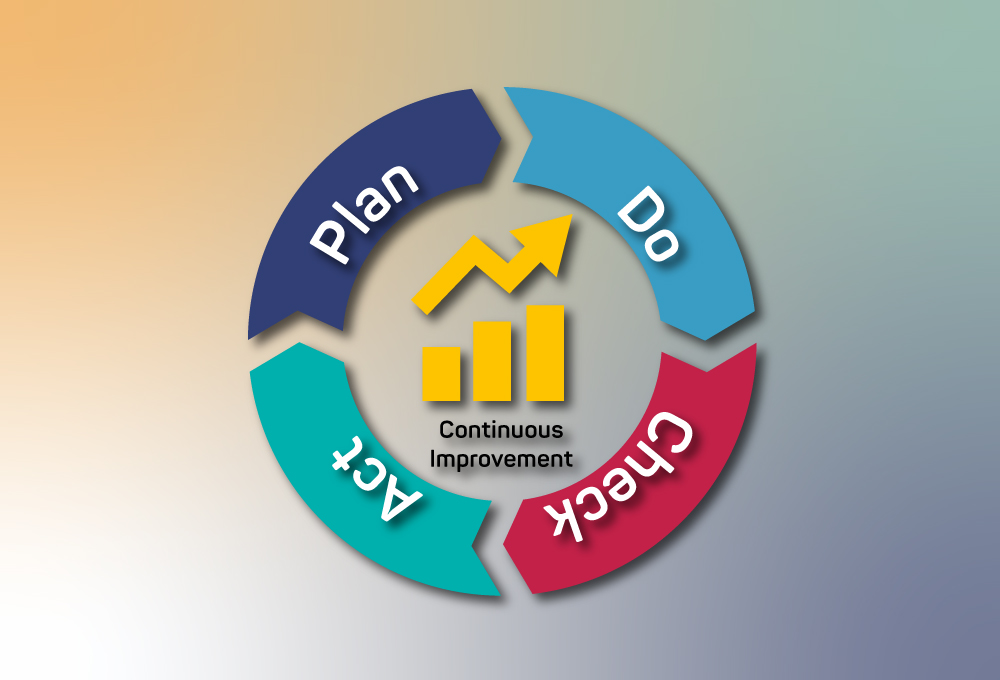
Just recently, we sat down with Steve Seiden of ADS, who provide technology solutions across the engineering lifecycle, and we had a great chat about all things improvement. The conversation flowed so freely that we thought it warranted a blog – so here it is.
Continous Improvement
Kaizen is a word you may well be familiar with. It speaks to continuous improvement from top to bottom in a business. It’s a big goal, and most companies struggle to get started, let alone make it a success. What are they missing? In a word – data.
Making a quality fix by luck rather than judgment should never satisfy a true quality professional, and so information needs to be central in decision-making within a business – including each and every manufacturing process and test. Data holds the key to unlocking quality and making continuous improvement a reality.
What You Need To Improve Already Exists
Kaizen is a quality management system born of American and Japanese expertise – made famous by the legendary manufacturer Toyota. Its key aims are to eliminate wastage and redundancies – two things every manufacturer wants. Because of its now famous name, Kaizen is today more of a buzzword in businesses rather than a framework to foster continuous improvement.
Why should you care though? Well, let’s be clear, if quality issues keep coming up, then there’s a good chance, at the very least, that you’re going to get some pretty bad press, and at worst you could go out of business. There is a solution though.
Data is the way out, it is the key to unlocking quality throughout your manufacturing, and your wider business. If you don’t know where a problem is coming from, or even know a problem exists, then you can’t fix it. Making visible connections between products and their testing processes is the key step in beginning to improve the ways in which you are operating.
Seeing Is Believing
In every area of our lives, we’ve never had as much access to data as we do right now. Throughout history, technology has helped to improve how we live and work, and that’s as true now as it has ever been. With WATS, you can surface your testing data, get to grips with it, and put it to work.
A big part of continuous improvement is that it should be shared throughout your business. That means the operators you have on production lines need to care about quality. You might already be lucky enough to have built that culture, but if you’re in a spot where your production line is more concerned with output than anything else, you need to develop it.
The best way to do that is to show them exactly what problems the business is facing with products, testing, or subcontractors, and make it clear that you’re all going to have to work together to solve them. The data is critical to this because without it, you’ll never be able to properly demonstrate issues and then improvements, and you’ll never be able to show your people that what they’re doing has an impact.
The more data you have, and the more connected it is, the better and broader a picture you can create. WATS enables cultural change in manufacturing environments and is a tool that can help facilitate continuous improvement. If you want to get better, start with data.
Is continuous improvement on your radar? WATS can play a part in making it a reality, contact us today.
“From a quality perspective, the thing I love about WATS is that it’s live. I can see everything. I’ve been working at Linn for nearly 30 years, and I don’t ever remember a time before WATS when test information has been so accessible, clear, and customizable.”
Matthew RandsQuality Engineering Lead, Linn