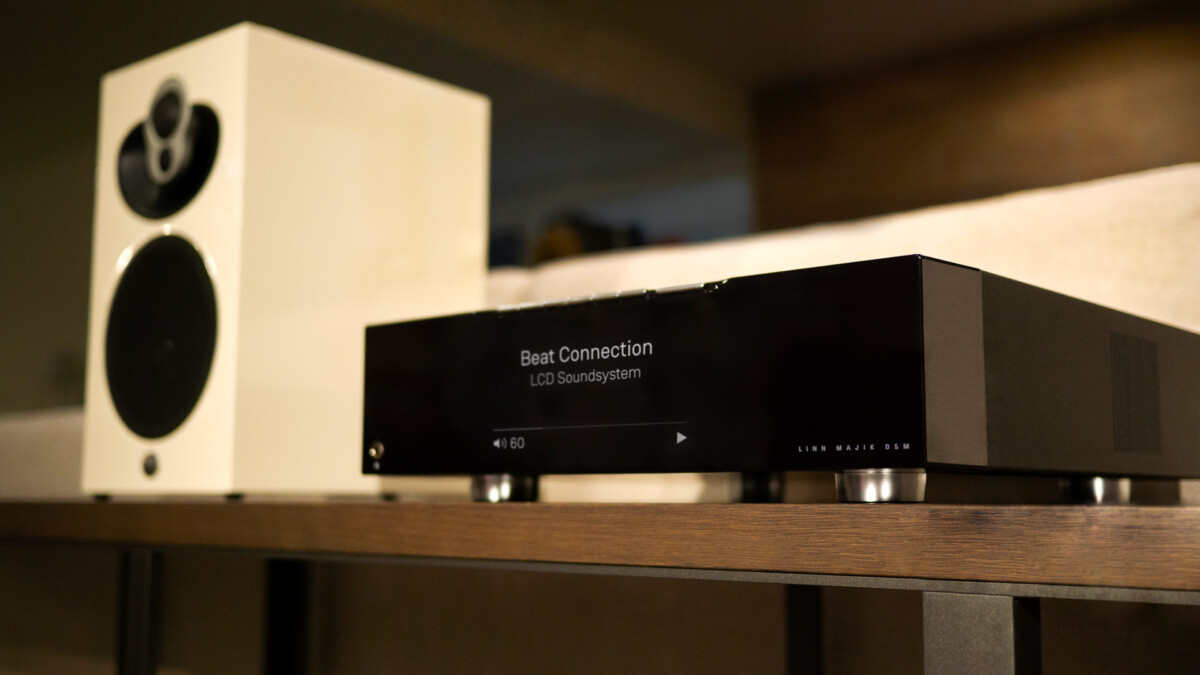
Linn is known for its top-end audio devices including turntables, streamers, speakers, and amps. Manufacturing equipment to the high standards they set requires rigorous testing, and we’re proud to say they run all that test data through WATS. Here’s why.
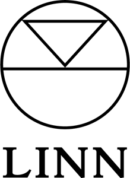
Linn is based just outside of Glasgow, Scotland, and at this site, they manufacture the vast majority of the parts that make up their incredible audio equipment. With a team of around 170 people, along with a wide range of products, their test output is deep and varied, so they picked WATS to connect the dots.
”From a quality perspective, the thing I love about WATS is that it's live. I can see everything. I’ve been working at Linn for nearly 30 years, and I don’t ever remember a time before WATS when test information has been so accessible, clear, and customizable.
Matthew RandsQuality Engineering Lead, Linn
Great Products Need Great Testing
Linn designs and manufactures all of its products in-house, and because of this, there are a huge number of different build and testing processes, across a wide range of manufacturing disciplines that go into creating their product portfolio.
The most complex of these products is the network streamer. In addition to standard optical in in-circuit tests for each board, Linn run a range of tests on assembled products to validate functionality and ensure the highest possible audio performance.
Collecting all their test data is clearly hugely important for Linn, ensuring that each stage is documented so that there is complete traceability of every testing phase. They use an Oracle database to house all their test information. Before WATS, interrogating this data was very difficult because they had to build manual reports in Excel. This was a particular challenge for standardising reports between different teams.

The Sweet Sounding Solution
Now though, WATS bolts on seamlessly to their test platform. It’s able to highlight issues at a component level, so as soon as there is a problem with a batch of components, the Linn quality team are aware of it, they can halt production, find the root cause, and follow up with their component suppliers as necessary. A big part of successful testing is having up-to-date information, and with WATS, Linn can see all of their data in real time.
On top of this, WATS allows Linn to track the data of individual components, seeing trends and part history. Linn are always keen to bring as much of its manufacturing in-house as possible to add value for the customer and improve the quality to their products. Now, when they see particular issues with componentry, it gives them immediate feedback on what potential areas they can begin to look at.
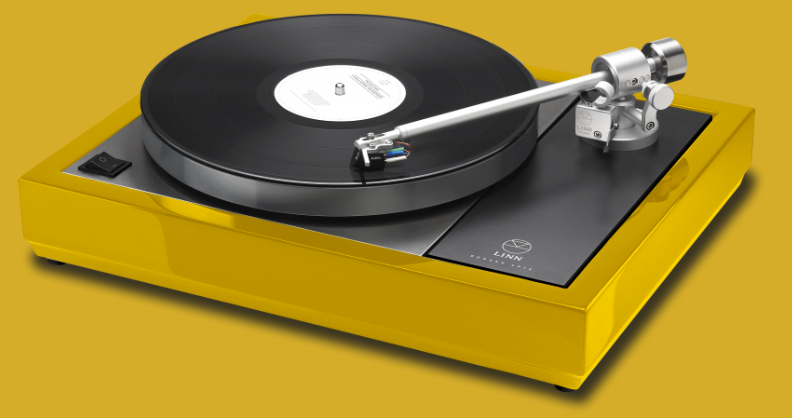
When speaking to Linn as part of writing this piece, we were especially proud to hear that very recently, one of the electronic design team wanted to eliminate harmonic distortion within a product life cycle. The only way they could achieve that was to run the data through WATS. It’s amazing to hear that we might have had not only a positive effect on test data but, even in some small way, an impact on the audio quality of a device.
For Linn, nothing has changed about how they put their test data into a database. WATS simply bolts onto their existing system and gives them visibility on every single part of their manufacturing process. It has helped build on an already great culture of quality because anyone who has the slightest interest in finding anything out can do so at the click of a button.
”We had an in-house system. What we found was it was good at collecting data, but not displaying data. With WATS we can customize reports and easily see everything we need to, quickly drilling down to the root cause of problems.”
Paul CochraneTest Team, Linn
Want to hear about how to best handle your test data? Speak to WATS today.