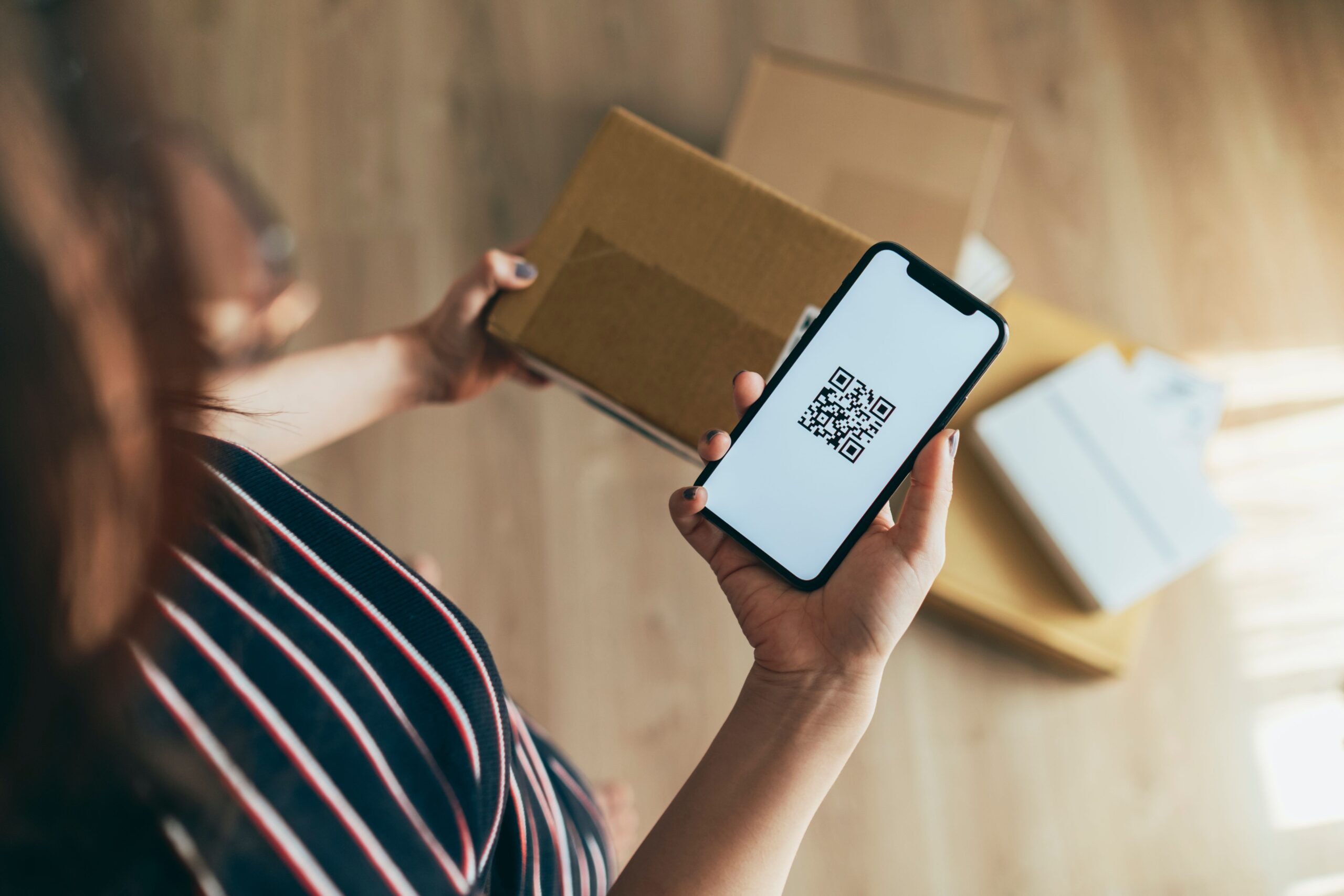
The typical view of Return Merchant Authorizations (RMAs) is that it’s a labor-intensive process that doesn’t return much value. But with WATS, things are a bit different. Our test data management platform is renowned for handling seas of test data and delivering actionable insights to test engineers all over the world. But what if we told you it’s also pretty great for handling return and repair data too?
Send It Back
We do concede that the RMA process can be costly, particularly if you have a global customer base but a centralized point of manufacturing. It means you’ll have to coordinate returns from your distributors back to your HQ, which is no mean feat. But if you’re going to all the trouble of getting faulty goods back to base, then surely you should aim to get as much value from the process as possible – while also streamlining it to reduce that cost?
What value can be gained from bringing faulty goods back and either repairing or replacing them? Well, aside from fulfilling what your customers probably expect of you, there is a great deal of real-world use that those products have been through that can help you improve in the future. While a lot of the reasons for product failures can be traced back to improper usage, the end user isn’t always to blame – often there is a pattern to be found.
Origin Story
That pattern is best sought out in its origins. Products that fail due to quality issues will share a history, and in those records will be the root cause of the failure. It could be the combination of a particular component and a specific firmware version, or conversely, there could be a testing issue, where they were all signed off on a single test station, which could mean your limits or tolerances are out.
By the way, if you’re already managing your testing in WATS, then you’ll have a complete history of that product ready to pair with the return and repair data – which is pretty handy. Using the Serial Number History feature, you can get instant access to the full history of a product, along with statistics informing about the most frequent historical repair types for the failed test steps.
RMA Is A Part of Broader Improvement
Continuous improvement is always a popular subject for manufacturers – which makes sense. After all, what business wouldn’t want to fix issues in the future and reduce production bottlenecks?
If continuous improvement is on your radar, have you considered how useful RMA can be? It’s not just even production that can benefit from learning about product failures – you’ll quickly start making friends in marketing and sales if you can make your product more reliable.
There are a lot of definitions of ‘brand’ out there, but many believe that it is the meeting point of what you say you do and what you actually do. If your reputation hinges on the reliability of your goods, then effectively reviewing returns and finding root causes of failures is going to do wonders for your image.
Clearly you’re not going to be making operational decisions based purely on optics, but they are an important consideration. Whatever the true motivation to make production better in a manufacturing environment, RMA offers a rare goldmine of info that if you don’t try to tap into, you’re missing out on.
Learn how you can do RMA the right way with the WATS Repair Module.