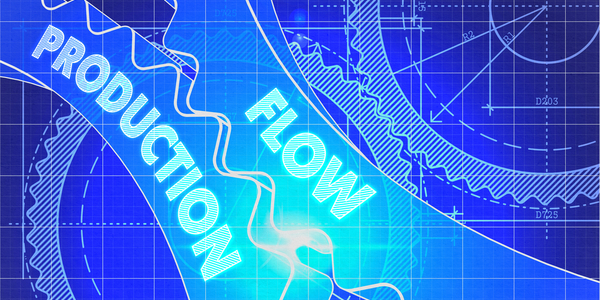
With thousands of tested and manufactured products in your supply chain, unveiling your real bottlenecks is tough.
Product tests might be performed in the wrong order or too many times – running up costs and wasting precious first pass yield. Or sometimes there’s an issue with how things are carried out in production.
In some cases, it’s the operators that make mistakes. Without a proper framework in place, workers freewheel – paving the way for errors and faulty processes in your operations.
But what if you could create a flawless workflow for manufacturing and testing?
An Error-Free Workflow
With the ability to control how things are done in each step, you can stop operator- and testing mistakes before they happen. By knowing what’s going on, you can remove anything which doesn’t provide value. With robust data backing up your workflow, you can nix all the errors – embedding a new, optimised workflow that no one can deviate from.
You know how things should be in your factory. But methods, machines, and processes always need tweaking. With a workflow tool that supports scaling up and continuous change, you can adapt with complete governance.
To uncover where your bottlenecks lie, you need a reliable monitoring tool and complete oversight of your production line and test facilities. In addition, having access to a tool with the ability to control the workflow in your operations enables you to decide how testing and production is carried out centrally.
Complete Production History
In many cases, subparts are used in many different products. You need to know that the top-level consists of the right components, that all subparts are complete, and that your product has completed functional testing.
WATS gives you a complete history of all the major parts involved in making your products – including subparts. With an ability to thoroughly monitor production, you can verify each step down to a single unit. This precision gives you accurate data that you rely on – no more guesswork.
Impeccable Testing
The WATS testing system workflow also removes any possibility of running tests in the wrong order. With full monitoring capabilities, you can see how many retests have been done for each product. For example, if you only decide to allow three retests of a unit, you can determine whether it should be repaired, put back, or scrapped. WATS makes sure that the end products have passed all steps in the correct order.
In the dashboard, you can see your production yield, divided into three stages – first pass, second pass, and third or last pass. For your processes to be fully optimised, a high first-pass yield is essential. With WATS, you will always know where you’re at – making sure you can see where problems lie in retesting.
Furthermore, with the ability to search for serial numbers of parts, you can track each unit’s precise state, location, and status.
Need to optimise your production and testing workflow in your manufacturing processes? Contact us today.