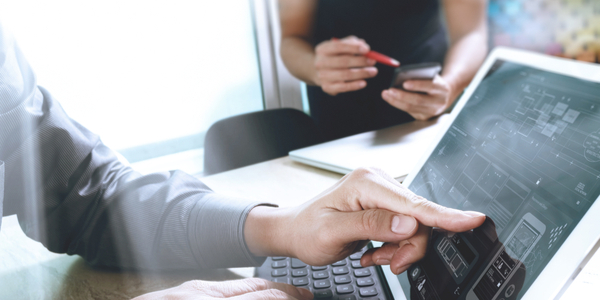
For Frederik, our test developer, WATS’ most valuable asset is the ability to tune sequences and perform yield analysis. As a consultant, he uses data from WATS to develop better test systems.
When you have useful test data, you can improve on theoretical limits and see what kind of stats and parameters you can get. In a testing facility, this is vital. It allows you to steer past limits to secure excellent process capability – helping you spot even the smallest amount of skew.
Fighting False Positives
Testing different tolerances based solely on vague hunches from customers is common. But when putting them to the test in real-world scenarios, the results often don’t add up.
A practical example is testing LED lights to check the hue and brightness. LED lights are renowned for having high variations – something that must be accounted for in testing. If your testing limits are too narrow, any normal variation can cause a false positive. A false-positive result flags satisfactory units as bad units, which decreases your yield in the process.
The opposite can also happen. If your limits are too broad, bad units will go through marked as “good.” To ensure that adequate products pass and the bad ones fail, you need precisely tuned limits – something that will also give you the ability to see drifting in your process.
Increasing Yield With Accuracy
With WATS, you’re up and running instantly after installation – giving you the ability to set extensive and accurate testing limits fast; which you then fine-tune to perfection when more testing data is available. Accurate testing ensures an excellent process capability – allowing you to find as many faults as possible: without false positives wrecking your yield.
Thanks to a complete overview of your production line from the WATS dashboard, you can also set up alarms and receive alert emails if your yield drops below a set threshold – giving you ultimate process control.
With a chronological overview in WATS, you can also see exactly when something changed in your production process. As well as spotting minute changes in third-party components in different batches, you can also catch faults related to environmental factors – like humidity and temperature.
For instance, one factory turned off their air conditioning during lunch, which caused a stream of significant faults in their production line. Without access to the vital data – they had no idea until it was too late. With critical information about the date, time, test station, and operators – you get access to all vital data that would otherwise be lost.
Need more accurate test results in your factory? Want to reduce false positives? Sign up today for a 30-day free trial on register.wats.com.