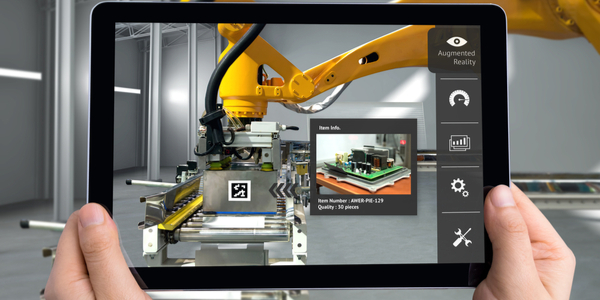
As COVID-19 causes economic chaos across the globe, modern supply chains face unprecedented challenges.
Even before the crisis hit, trade tensions were rising with the US and China imposing tariffs on hundreds of billions of dollars worth of one another’s goods. But with global demand for cheap manufacturing goods still thriving, China remains the supplier of choice.
However, to maintain a competitive edge, manufacturing businesses need to explore new ways to move towards ‘Supply Chain 4.0’ – in order to become faster, more flexible, accurate, and efficient. Doing this relies on having the right data from the right sources.
But when there’s so much of it, and with so many parties within a single supply chain using it in different ways, getting a straightforward picture of the data ‘status quo’ can be very difficult.
Optimizing Data To See The Bigger Picture
In order for manufacturers to get an accurate view of their potential issues impacting their production lines, data analysts and test engineers often spend hours rigorously number-crunching data sources.
Using tools such as Microsoft Excel, they often build algorithms and formulas exploring different situations across the supply chain – accuracy is wholly dependent on finding the right data and metrics.
When it comes to quality assurance, there’s also no guarantee data is 100% accurate as the metrics can quickly become blinkered – as they’re entirely dependent on one person’s analysis of the datasets. This can send a business in a completely different direction. Plus cumbersome processes can result in analysts having to make assumptions to save time.
Accurate Data Rather Than A ‘Best Guess’
Manufacturers should be able to take a democratic approach to reviewing data across the whole organisational supply chain – from product design, development, and R&D to customer service and maintenance. They need a pragmatic view of the entire company.
Rather than having statistical models provide a ‘best guess’, what manufacturers need is raw data – from across the entire supply chain. This will not only help them address ‘real’ problems when they arise, it’ll also help them make more accurate predictions – to stop future issues using trusted, unfiltered data from each stage in the manufacturing process.
Data Helps Redistribute Costs
This is where a solution like WATS can really add value. WATS contains detailed information on any failure that occurs during the entire manufacturing process. This gives manufacturers what they need to better understand opportunities, issues, and failures across the whole line – allowing them to get to the heart of the issues instead of focusing on one specific area.
WATS’ data is all symptom-based. And because all related datasets are linked together, manufacturers can see the whole picture instead of one specific insight. This allows them to monitor a range of different stages.
Right now, many manufacturers still rely on single production facilities or contract manufacturers, so while a return to regional supply chains presents an incredibly complex challenge, it might be seen as an easier option.
Regardless of the options at hand, structured and standardized data formats and visual data interfaces offer companies maximum flexibility. It also reduces structural dependencies on single operational partners, and increases the ability to react to unanticipated events.
Overall, given the uncertainty of travel, shipping, and other issues facing supply chains in a post-COVID world, using the right data will help manufacturers make fully-formed, more accurate decisions – data-supported decisions that have the potential to radically improve the profitability of your company.