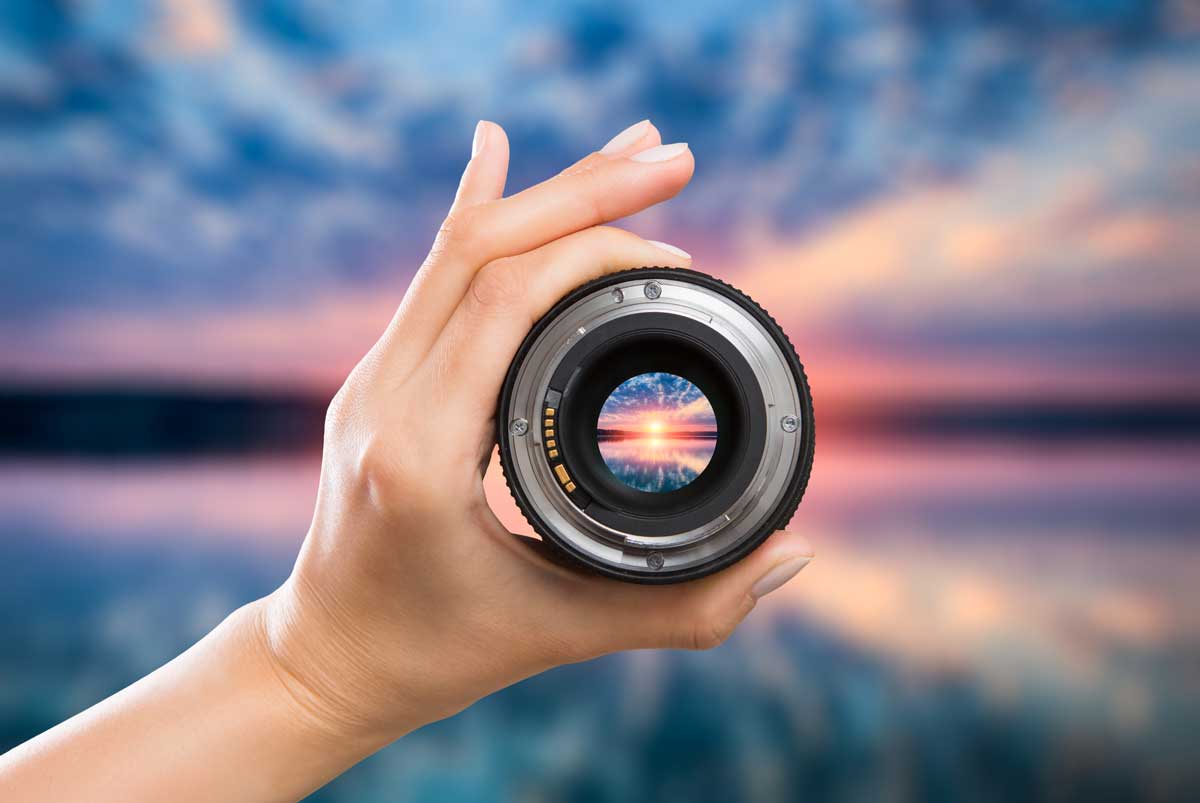
Electronics manufacturing has never been ‘easy’, but it’s definitely getting harder. Despite all the technological advancements created to make life easier, the pressures of more demanding delivery schedules, paired with global economic issues, make your job harder than it’s ever been. You need to look ahead to escape that pressure.
But we appreciate that’s easier said than done. With so many different parts of your manufacturing environment to manage, how can you possibly find the time to plan, let alone make those plans a reality? We won’t solve all your problems today, but we can help you with that one.
Constant Fire Fighting
If you’ve never experienced what we’re about to describe next, we’d be very surprised. The parts you got in from a trusted supplier for your urgent production run are late. Not only are they late, but the parts also aren’t the ones you received in the last batch, and now your assembly doesn’t work properly. Now, you’ve got sales breathing down your neck to get the right parts in – quicker than ever before. Otherwise, the customer is taking their order somewhere else.
Sound familiar?
Of course, it’s a vague example, but these are trends that we see throughout the manufacturing space – particularly when it comes to electrical manufacturing.
Problems in manufacturing will never completely disappear, but surely there is a better way to work than constantly putting out the same type of fire every day of the work week, no matter the project?
While firefighting is sometimes needed, a better way to operate is proactively, spotting issues on the horizon way before they fall into your lap. That sort of vision takes data from across every part of your testing operation.
Using Data To Get Manufacturing Under Control
That’s right, the majority of your firefighting can be solved with data. Just lots of information on its own isn’t useful: that’s likely to blur the picture even further. But a well-connected dataset that brings together your supplier’s testing and your own testing is critical for putting together a plan of action.
Many production managers use their gut instinct to make decisions. While there is, of course, a great value in experience and being able to draw from what you’ve seen before to positively impact a situation. But the truth is, your instinct can’t hold a candle to real, live data. Sure, how you implement changes to accommodate for late parts, or off-spec components can be driven by your experience, but you should always be led by up-to-date, accurate information. That’s what WATS does best. It gives you visibility in every part of your testing, whether that’s in-house or off-site.
There are so many problems you aren’t going to be able to fix – just look at the various conflicts across the globe right now or the looming financial crisis. But you can control the data you see and use it to make better decisions – so start today.
Tired of always dealing with the same problems? Speak to WATS – get your manufacturing under control.