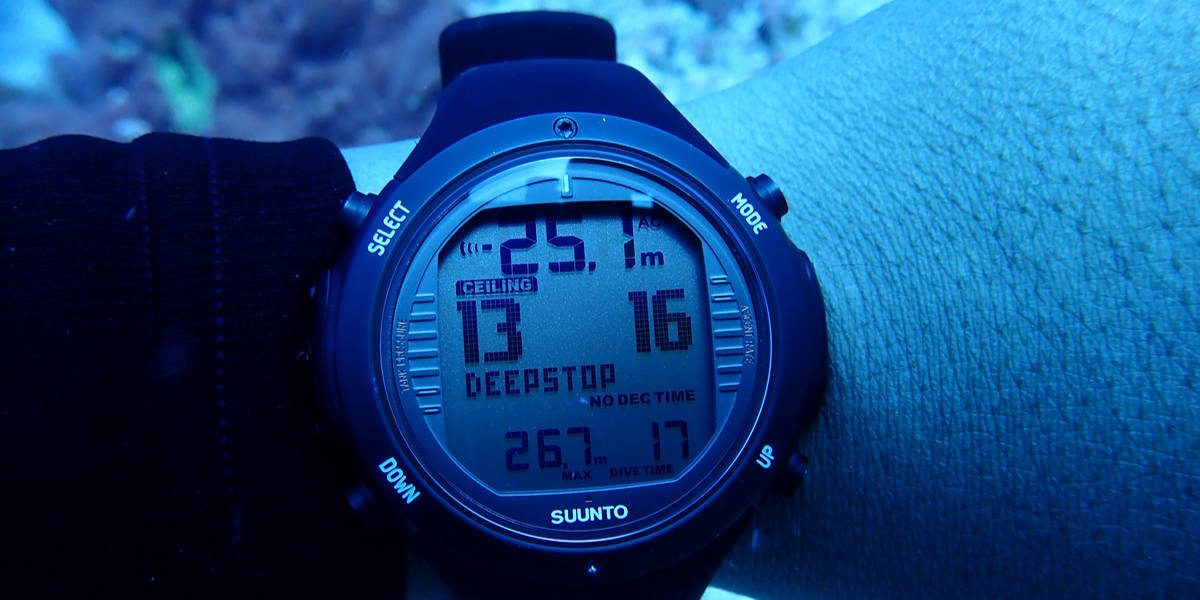
Suunto is a leading manufacturer of sports watches, dive computers, compasses, and precision instruments. Headquartered in Vantaa, Finland, the company was founded in 1936 after Finnish adventurer Tuomas Vohlonen invented the liquid-filled compass with a steadier, more accurate needle.
Since the beginning Suunto has grown into a quality global supplier of reliable precision equipment. Based in Vantaa, Finland, Suunto’s production is centered around its local facility, with a small but highly experienced team leading the way in automation and factory development.
Tapio Leveelahti has been with Suunto for 14 years, leading the manufacturing engineering teams in Finland. His teams work primarily on factory maintenance and automation but also factory development across the EMEA. We sat down with Tapio to learn more about their challenges and how they have used WATS to overcome those challenges.
The Challenge: Limited Test Visibility and Missing Data
For Tapio Leveelahti, who leads Suunto’s manufacturing engineering team, data availability was a growing concern. Its capabilities were limited. In fact, data often went missing and when it was accessible it wasn’t used widely. As their product range became more advanced, these limitations posed a risk to both quality and efficiency.
Sport watches are premium devices that get more advanced each year and are among Suunto’s best selling products. However, given the many delicate functionalities and features, it’s critical to ensure that there are no defects and that everything works flawlessly.
Tapio’s team needed dedicated tools to monitor manufacturing online to see what’s working, where the failed items are, and what the operators are doing. And they needed to determine all of this in real-time quickly. Expanding the existing system would have required heavy internal resources, so this wasn’t a good option. Tapio’s team wanted a solution that was fast to deploy, easy to maintain, and built for scale.
Rapid Implementation: WATS Up and Running in Two Hours
Looking for new tools and solutions to take Suunto’s manufacturing to the next level, Tapio came across WATS through a recommendation from a local WATS partner. After a quick and easy implementation, they launched the first pilot test – using their company’s Ambit sports watch range as their main test subjects. Within hours of the first pilot all data was online, and the new system was fully operational.
For a small, high-performing team, that speed made all the difference.
Real-Time Insight, Less Maintenance
With WATS, Suunto gained full visibility into its test and manufacturing processes. The system now provides real-time monitoring, clear defect tracking, and immediate access to operator-level performance data. Tapio’s team no longer spends time managing the system. Instead, they focus on improving processes and supporting production both internally and across partner sites. Compared to other tools on the market, the team particularly like the ease of maintenance and how little it requires to run. They are also happy with its scalability.
”Compared to other tools, WATS is easy to maintain and just works. We get the insights we need without the overhead
Tapio LeveelahtiHead of the Manufacturing Engineering Team
Scalable Across Suppliers
As database experts, they need an accurate tool that records data and gives them immediate oversight and statistics access. And as a small team, it’s important to stay efficient at all times. Today, Suunto uses WATS across its own facilities and with key electronics manufacturing partners. Mechanical and electronic features are tested directly in the final product, and all data is instantly available for analysis.
The results speak for themselves:
- Higher yield
- Better traceability
- Faster issue resolution
- More efficient use of engineering resources
And when issues arise, or they have missed information they always get quick responses from the WATS support team who are poised to provide help and support when needed.