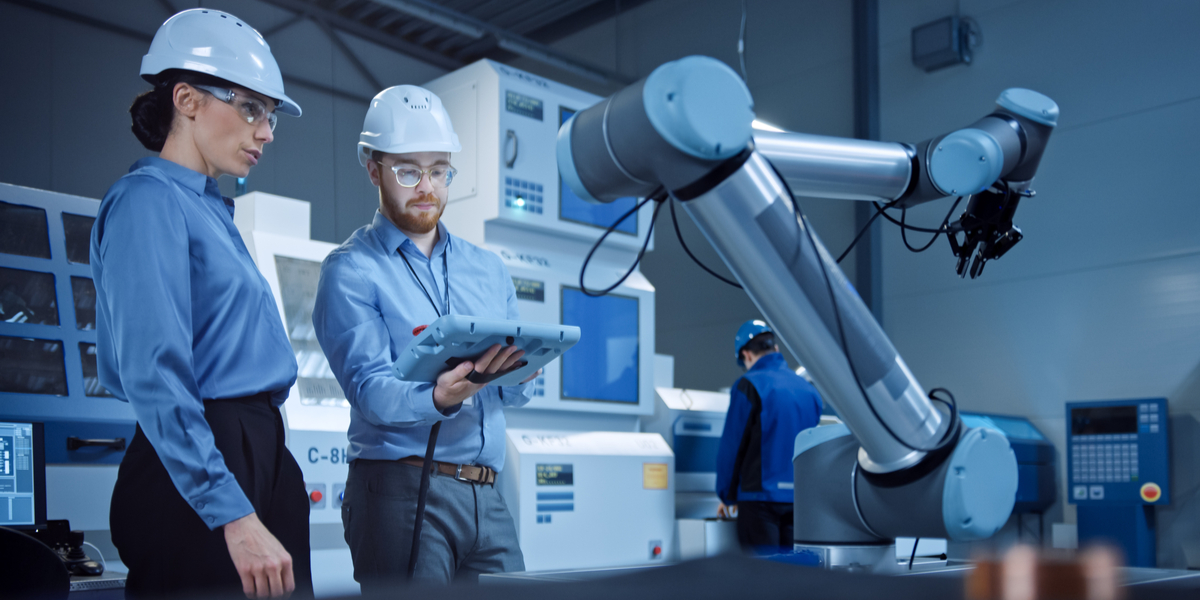
Industrial-scale digitalization started to make ripples worldwide a few years ago. Now a tidal wave, this era of technology innovation is presenting companies with a sea change in how they work – from product development and quality assurance to volume production and coordination of global resources.
One of the pivotal players at the forefront of engineering process innovation for industry is Finnish-based global engineering consultancy company Etteplan, providing digitalization services, embedded solutions, industrial equipment, plant engineering and technical documentation solutions to the world’s leading companies in the manufacturing industry. Test and measurement solutions for various industries are an essential part of Etteplan’s offering.
Customer list includes world engineering giants
Etteplan’s software and embedded solutions service area helps customers to develop and bring intelligence to devices, machines and digital services. The service portfolio extends from product development and connectivity to digital services and analytics.
Etteplan’s professionals design electronics, mechanics, embedded software, connectivity and digital services needed for the end user in close cooperation with the customers. Etteplan’s personnel aid in defining the product features, assist in creating a suitable architecture, implement the prototypes, automate and cover testing during the R&D and provide test machines into production.
The expertise needed to bring the services into use and devices into production are the core strengths of the company. Etteplan keeps maintaining usability, compliance and security of delivered solutions for as long as it is needed.
Established in 1983, Etteplan now employs 3,300 people based out of 85 offices worldwide.
Tapping into global demand
Fast forward to the present day, and the company continues to pioneer innovative solutions for customers and has become a standard bearer for Industry 4.0 – the era of digitalization of industry and automation of processes.
The consultancy is tapping into the global demand for engineering and design services that is growing globally. Meanwhile digitalization – in parallel with a world coping with the COVID-19 pandemic – and the lack of skilled employees presents potential obstacles to the growth of companies that fail to integrate automation.
WATS has everything we needed and is totally Scalable
Tero Leppänen, VP of Testing and Product Verification at Etteplan, is responsible for testing related services, such as software testing, production of testing machines,, product verification, including compliance and accredited product testing, market access and various safety and environmental testing services. “We provide these testing services to your customers during the product development and manufacturing of their products” he explains. “That places a huge responsibility on us to ensure we get it right from the start”.
“In production testing, it was apparent that many organizations struggle in gaining the best return on their investment from data and we were early adopters of processes to unlock that data. Within our customer-base there was a need for test data collection and analysis. At first we started to develop our own software for that purpose, but soon it was found out that creating such a system and especially maintaining it is a huge task. After some research, we got introduced with WATS, which has everything we needed and is totally scalable,” continued Tero, whose involvement with WATS stretches back to 2015.
Quickly dive into data, identify issues and implement fixes
Tero’s teams are organized based on competencies and expertise depending on the needs of the customer. “It makes for a dynamic culture and an energy that thrives on innovative solutions. WATS helps us – and our customers – to quickly dive into data, identify issues and implement fixes and improvements.”
So, what does a typical project look like? Manufacturing setup of a modern electronics product has several phases, which could be divided between several factories. Often printed circuit board assemblies are manufactured in a separate factory, while the final assembly of the product is made elsewhere. After each manufacturing phase, products shall be tested, especially in case, where the products are then transferred to the another factory.
After the final assembly of the product, the testing of functionality and safety is obvious before delivering products to the end user.
Etteplan’s services are needed to build the test machines which are then used in the production facilities to test that everything is operating and working fully, from one product to an entire family of products.
Difference between success or failure in the marketplace
Tero adds: “We help customers to specify how to test those products, we design and build the test machines, deliver them to the factories and maintain test machines during production phase. On the software side, we use WATS to collect test results and to monitor that the test machines are working properly, customers will have access and real-time visibility to test data via WATS. It helps to create a quality circle at the start of the NPI (new product introduction) development cycle. During the production phase, WATS enables continuous improvement in the production process and helps to recognize potential bottle-necks in manufacturing”
Customers are able to gain the immediate value
Tero points to the fact that Etteplan has integrated WATS into its solutions, and works alongside Virinco, in customer meetings, webinars and exhibitions, “WATS is a standard part of the test machines, which is a very good way to demonstrate the WATS value for the customers. Not only do we integrate WATS in test machines we build, but also we integrate it into existing test machines already in use.”
Interestingly, customers are often surprised at how WATS is easy to use and that they can have a instantaneous visibility to test results, further analysis based on results and key performance indicators of the production. Because it is so intuitive, after an hour’s demo, they can pretty much use the software immediately.
“Customers are able to gain the immediate value once WATS is put into use even in a single test machine. Gradually the usage of software can be increased within the tester fleet, creating more and more value. Since it’s integrated with our test machine, whenever we deliver machines the customer is able to monitor production statistics in real-time via WATS.”
Enhances our customer experience, providing more customer satisfaction
In terms of initial trial – most of the customers continue to use WATS afterwards.
“For Etteplan, it’s important that when we deliver a test machine to the factory we would like to make sure that it performs as planned. For us tester supplier it is important see that production start is happening in schedule and that there are no unexpected issues with test machines – if there are issues, it’s good to be able to see them immediately, analyze and fix them.
“WATS gives real-time visibility into the machines and enhances our customer experience, providing more customer value and satisfaction” adds Tero.
In some cases, testing time is a critical parameter. WATS is a perfect tool for optimization of test times and minimizing unnecessary delays in testing process. “When there is room for optimization WATS provides easy way to track it: not just the test results but the test machines.”
Successful customers and partners will keep developing products
Without proper test data management, customers are unable to access the full predictive value of test machines. “You waste the possibilities to extract maximum benefit — but by getting the data you can change the investment to improve the efficiency in production”
According to Tero this could perhaps be achieved manually or by using Excel spreadsheets or other tools, but that would require a lot of manual work, become quite a big task and hard to make it reusable. “With WATS we don’t have to build tables and calculate the data — WATS gives analysis results directly to us and it just works! There is no need for heavy configuration or setup for each project.”
Looking ahead, Tero believes that successful customers and partners will keep developing products further and due to the good relationship Etteplan looks forward to consuming feedback and helping to improve the WATS platform.
Sign Up Today for your free trial
Discover what WATS can do for your testing and manufacturing processes.