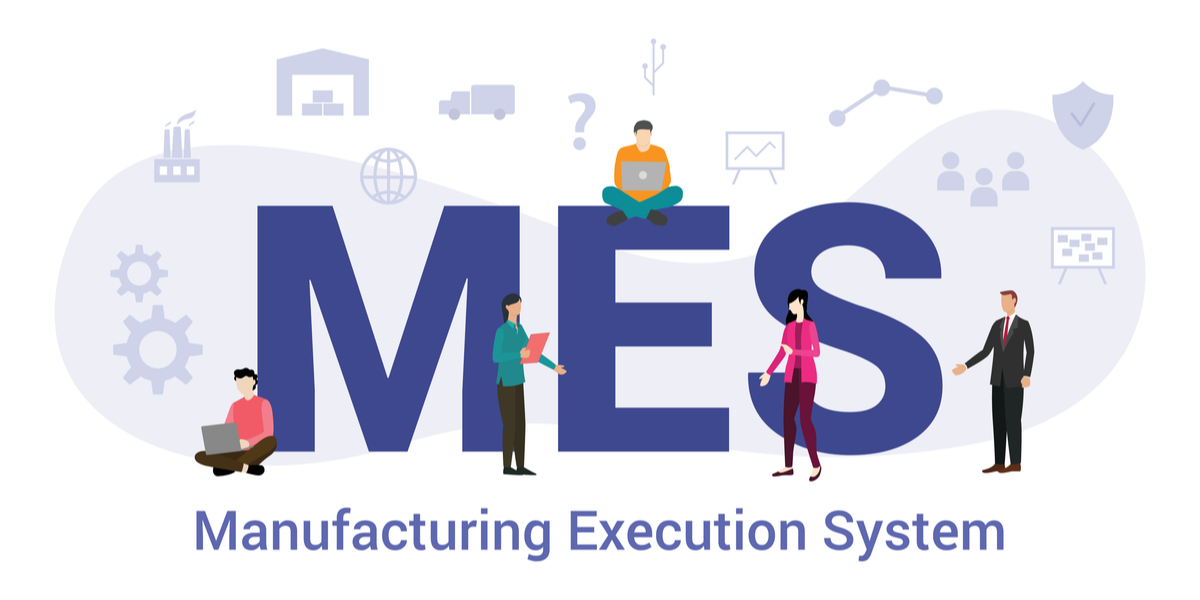
Identifying issues and troubleshooting are critical to the efficient running of manufacturing operations. However, many organizations’ approach to achieving this can be overly complicated – as well as rigid, costly, and counter-productive. In this blog WATS sales director Vidar Grønås explains that real time access to data lies at the heart of effective and error-free manufacturing.
Identifying issues and troubleshooting are critical to the efficient running of manufacturing operations. However, many organizations’ approach to achieving this can be overly complicated – as well as rigid, costly, and counter-productive. WATS Sales Director Vidar Grønås explains why real time access to data lies at the heart of effective and error-free manufacturing.
Traditional MES approach in effect puts brakes on the Production System
The conventional wisdom for many manufacturing businesses has focused on methodologies dictated by Manufacturing Execution Systems – incorporating software solutions built into the manufacturing process and proactively and systematically enforced. However, these systems can be extremely expensive to integrate; across multiple sites and software systems.
Moreover, the traditional MES approach in effect puts brakes on the production system from the get-go. In this stop-start methodology, for companies such as electronics manufacturers – from OEMs to integrators and assembly operations – test and measurement operations can become bottlenecks. The upfront system alarms become obstacles, and can potentially impose serious production delays and time penalties.
But it doesn’t have to be like that. There are options for more agile methodologies such as that offered by WATS that integrates any test and repair station across the entire supply chain. Quickly identify production yield issues, frequent test or product failures, poor test coverage or other performance problems – in real-time, directly through your web browser or mobile device.
Empowered to be more cost efficient and to speedily react to abnormalities
This web-enabled system provides real time views, across manufacturing sites worldwide. Through a top down approach that can identify which failures may occur on an ‘as needed’ basis, users are empowered to be more cost-efficient and can speedily react to abnormalities – rather than implementing rigid control mechanisms – through features such as:
- Dashboards (to enable at a glance summaries of key metrics); giving users real-time visibility of products they are building, and important KPIs, what is failing and where, as well as individual measurements
- Integration with other systems: Repair, Data Analysis, visualization tools, ERP etc
- Real time alarming: which ensures ‘as and when’ access to issues, enabling timely problem-solving and avoiding upfront
- Control software distribution
- Control Serial numbers and MAC addresses (to avoid duplication)
- The ability to read which state the product is in, without controlling or stopping the flow
- Changes to the state as products flow, instead of building complex rules that need to be maintained
What if you could achieve this instantly? Use the information to build up rules sets and troubleshoot abnormalities?
Add flexibility and remove rigid control systems; and a lot of programming is needed with process and protocol in MES methodologies.
Continuous improvement through access to instant data
The WATS approach is less rigid, post-processing retrospective information, as opposed to pre-processing. Here, users are able to slash implementation times from half a year to working immediately. This allows you to become more agile as a business.
Looking ahead to future developments, this framework can build on what it learns through the testing, such as circuit tests and PCBA (PCB Assembly) tests. This iterative learning approach extends to the final function test. Allowing the system to learn and adapt, enables it to demonstrate continuous improvement through access to instant data, decision making and effective and efficient corrective action.
The investment by electronics manufacturers in MES is often huge, and not restricted to those involved in production of high value products. It can become a massive drain on resources, and in effect dictate the pace of manufacturing. The WATS alternative, in effect, provides instant results. What’s not to like?