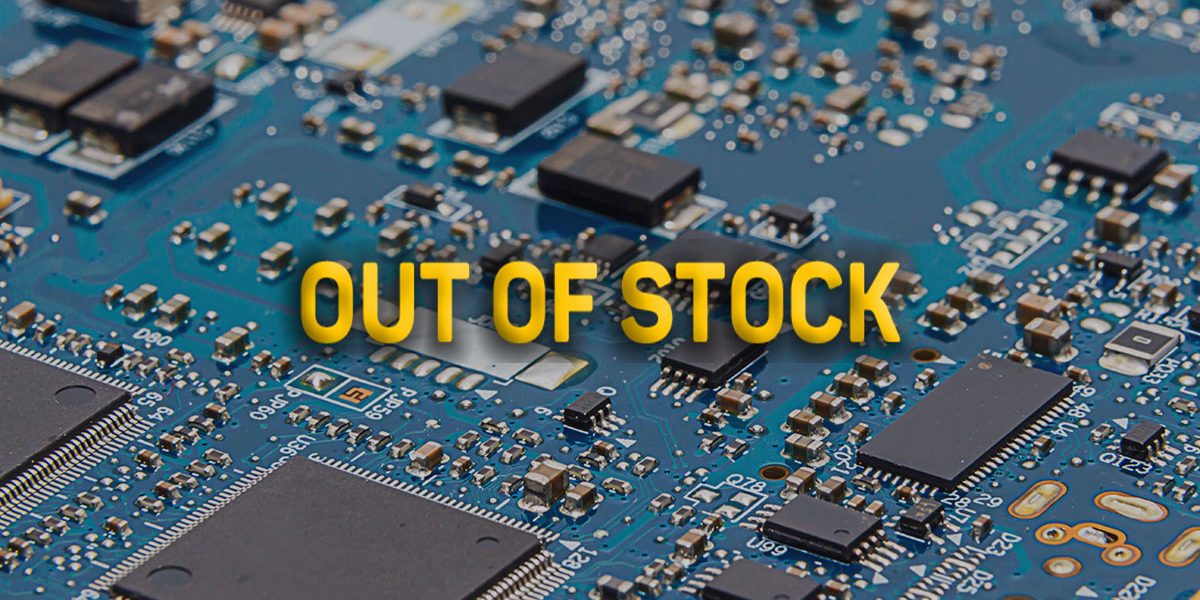
If there’s one thing that the pandemic has taught us then expect the unexpected has to be a top contender. In this blog WATS sales director Vidar Grønås explains that challenges to component supply chains thrown up by COVID-19, and other crises, have placed the spotlight on remote test and monitoring systems.
The world’s electronics industry has had to contend with shortages, not just exacerbated by the pandemic but shortfalls in the production of base metals and, in the high-value sector, the complete disruption of the semiconductor market. It could be said this has produced the perfect storm for disruption!
In turn, this uncertainty has brought into sharp contrast the need for flexible strategies and agile methodologies to minimize the chain of potentially damaging effects: impact on design and build, and therefore quality and disruption to production.
Systems such as WATS have become a lifeline for some businesses
Facing these seemingly unrelenting issues of component shortages, the industry has been forced to source alternatives, and that can lead to challenges, including the need to re-design, potentially making them hostage to fortune.
During these periods of uncertainty, systems offering remote monitoring and control such as WATS have come into their own. They have become a lifeline for some businesses. As we tentatively look to approach a return to normal (or as near as we can), then lessons learned of the efficiencies and safeguards from remote systems are destined to transform the electronics, and other manufacturing industries.
At these times of component shortages, manufacturers struggle to find exact or dependable replacements. This forces them to turn to re-design. At the best of times, this can present challenges including issues such as replicating exact dimensions, apart from delays in re-tooling or configuring test stations and assembly processes.
Redesign of components significantly adds to the risk factor
It is precisely in situations such as these that WATS is the perfect solution. These remote systems enable detection of failures where they are introduced, highlighted by the 10x Cost Rule of Manufacturing that tells us the cost of fixing an early failure grows exponentially for each step it is allowed to pass in the manufacturing process. Redesign of components significantly adds to the risk factor, often producing components that are less stable or with different characteristics than the original component.
When new components or re-designs are introduced there is a need to revalidate, and a root cause analysis needs to be conducted. Say, for example, the factory can’t deliver a key component for your PCB. That means you have to source another one. But, that’s just the start: you may also have to change other things on the board, you may have another capacitor or a different resistor, and this has to match the performance of the original component. You can see how this list of challenges can quickly grow!
Industry needs to remain nimble and agile to survive
In this case, when you try to mass-produce this new board with these new characteristics there will be problems and you need to find out what those problems are. WATS has been really valuable in helping figure out issues such as this. There has been a combined benefit. Remote access to data during a time where we have experienced travel restrictions has been a life-saver for some businesses. In tandem, when alternative components have been introduced, and resulting changes have been made to the product, then this ability to remotely diagnose has not just changed the way that the electronics manufacturing industry works, but provided process safeguards that ultimately protect the bottom line, at such a volatile time.
A key lesson learned is that industry needs to remain nimble and agile to survive. That strategy, enabled by remote systems, helps to protect businesses across the manufacturing chain from texting to production.
That approach spells the world of difference between managing through a crisis and forever reacting, and as a result, being constantly behind the curve.
Book a Demo to see WATS in action
Subscribe our Newsletters
Get updates on Test Data Management for Electronics Manufacturing.