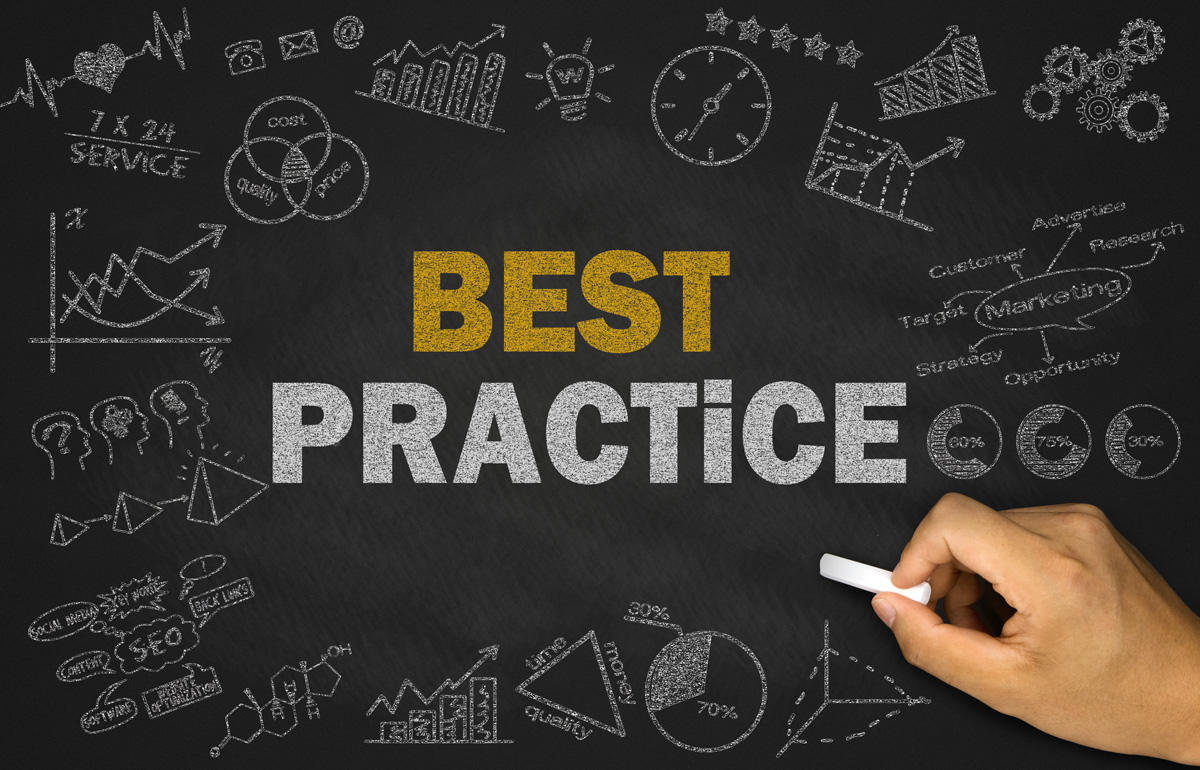
Manufacturing electronic components and goods is an extremely complex process that requires a high level of precision and accuracy – particularly at scale. There are best practice techniques for every single element of the entire manufacturing chain, but today we’re looking at some of the practices surrounding data management in an electronics manufacturing environment.
Data management is one of the most critical aspects of electronics manufacturing, and it plays a crucial role in ensuring that manufactured goods meet the required quality standards. In this blog, we’re going to explore the best practice of data management control in electronics manufacturing, with a particular focus on yield, limit values, and retesting.
Key Best Practice Areas
Yield, limit values, and retesting are three key areas where data management can have a significant impact on the quality of the final product. By implementing best practice controls in these areas, manufacturers can improve the efficiency and effectiveness of the production process and deliver high-quality products to their customers more consistently – saving them time and money.
Yield
Yield is one of the most crucial metrics in electronics manufacturing. A high yield is an indication of the efficiency and effectiveness of the manufacturing process. In electronics manufacturing, yield is often calculated at different stages of the production process to identify any potential issues and improve the overall yield rate. But the most important part of this is true first-pass yield.
We’ve spoken about this metric at length on a number of occasions because we see so many companies getting it wrong. An accurate understanding of yield is essential if you want to improve production and testing processes. We really can’t overstate its importance, and if you have an in-house system that is currently calculating yield, you need to be certain it’s true first-pass. WATS has first-pass yield covered, so you can always check that out to figure out if you’re doing it right yourself.
Limit Values
Limit values are another critical aspect of data management in electronics manufacturing. A limit value is the maximum or minimum acceptable value for a specific parameter or process variable. In electronics manufacturing, limit values are used to ensure that the final product meets the required quality standards, based on testing requirements.
For example, the resistance of a specific component in an electronic circuit may have an upper limit value of 100 ohms and a lower limit value of 96 ohms. Anything outside of these parameters is considered a failure. However, there are tests that can be impacted by a huge number of external factors – including atmospheric conditions, measurement equipment, and connectivity – to name just a few. Therefore, limit values need to be created to match the testing environment and specifications. The only way to do that is to track failure trends and measurements over time. The only effective way to do that is with a test data management platform.
Retesting
Unwanted retesting can be huge cost sync for businesses. Not only are there time and money considerations involved in retesting, but it can also impact overall throughput if you’re dedicating testing resources to a product that has already been tested, potentially causing delays elsewhere. Also, if products are repeatedly failing tests then it is going to raise quality concerns – and rightly so.
Many manufacturers suffer from issues with their testing practices that actually flag failures unnecessarily or even worse provide the wrong root cause. This creates retesting that isn’t needed. The best thing an electronics manufacturer can do in this scenario is implement a system that monitors failures accurately and reports on them in an actionable way to save wasted time and money, and ensuring quality is properly controlled.
WATS offers completely customizable dashboards to give you a complete picture of your production testing environment. With visualizations you can build for your own business you can instantly review measurement data, upper and lower limits, as well as failure rates. It is the test data management tool built for electronics manufacturing.
Want to take your electronic manufacturing to the next level? You need to get the most value from your test data. That starts with WATS, so contact us today.
Keep Reading:
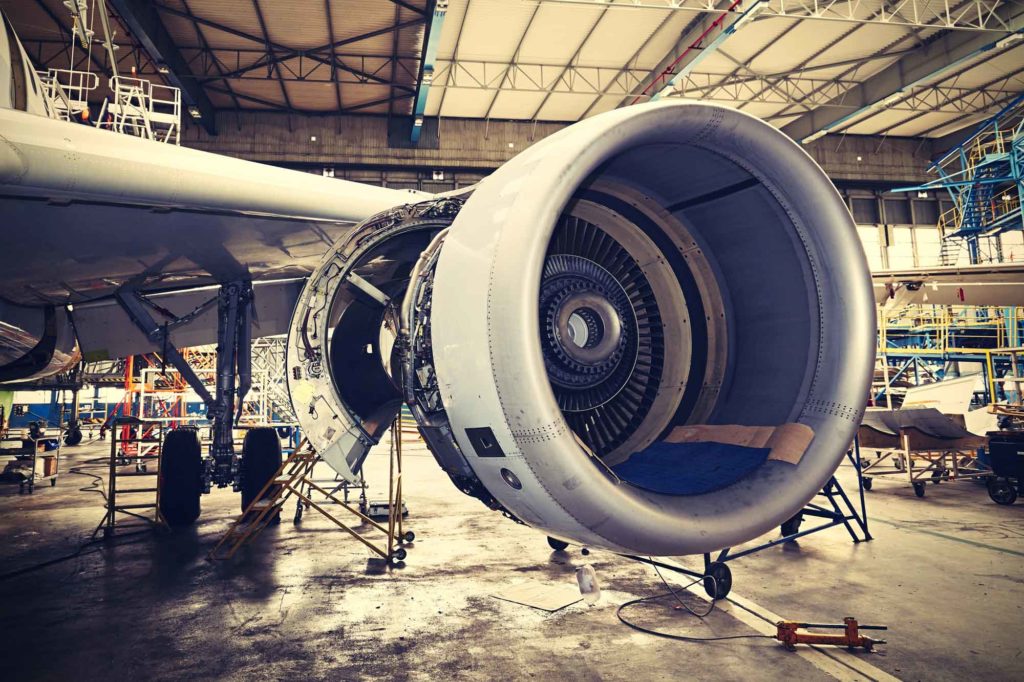
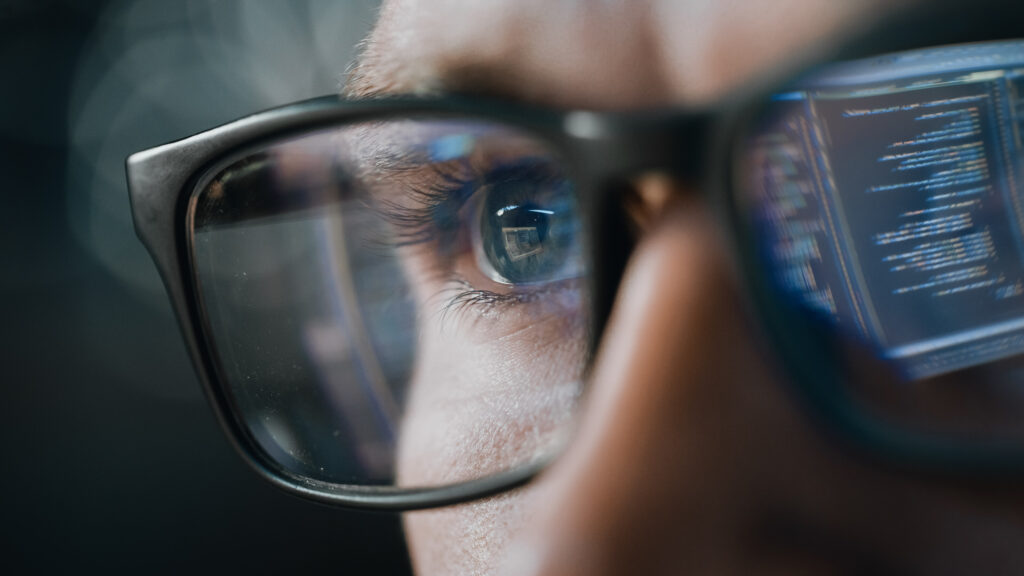
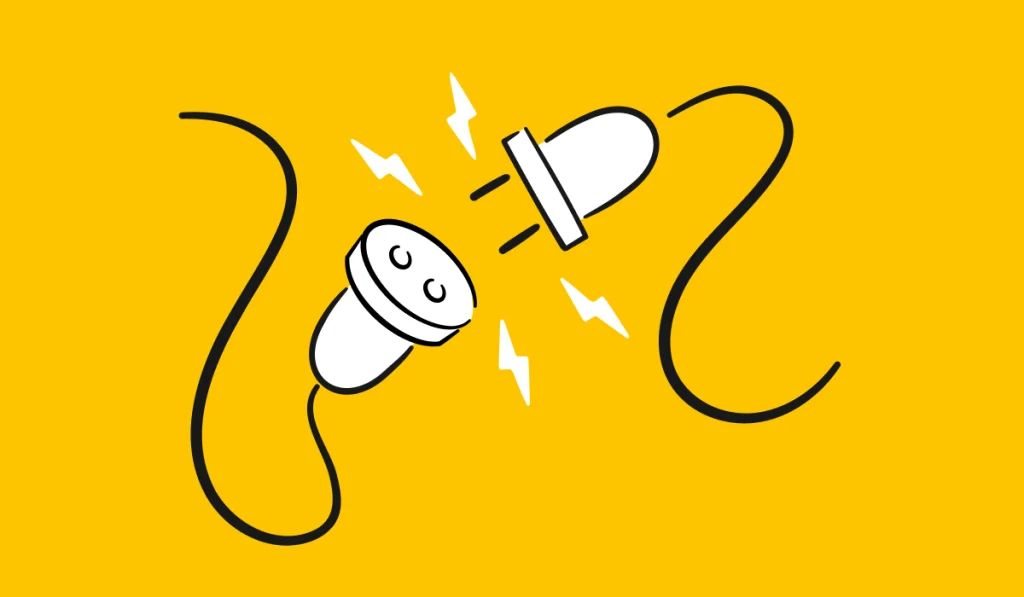