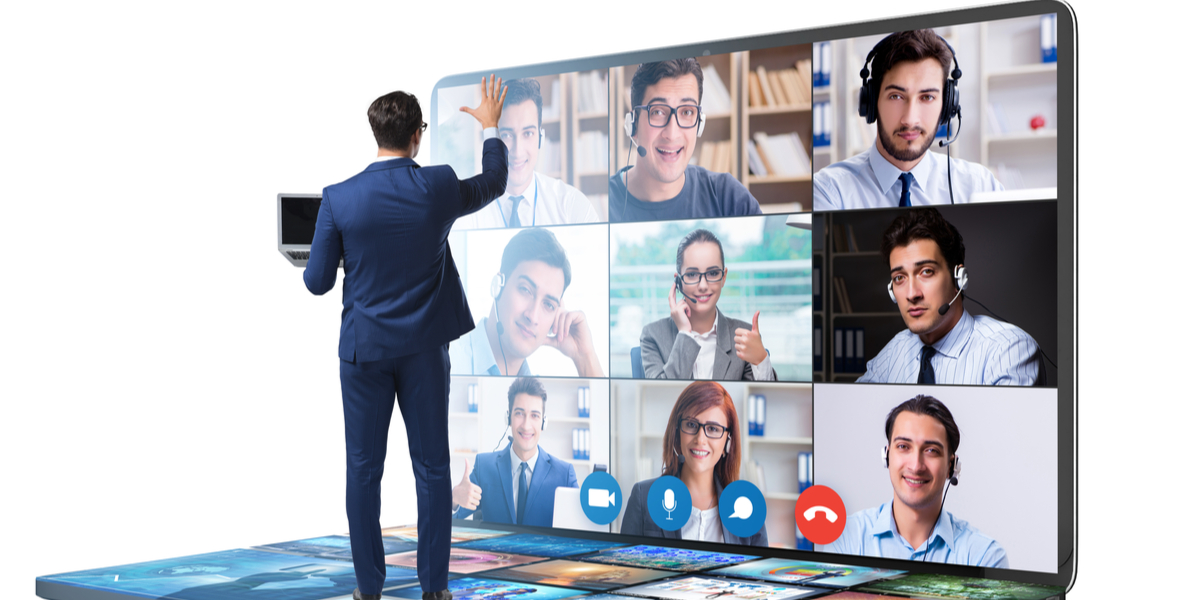
In this candid look to the future, shaped by what is available today, WATS Sales Director Vidar Grønås explains how online collaborative and monitoring tools have helped electronics manufacturers and companies worldwide future-proof their processes and protect from the disruption caused by the pandemic.
How many times have we heard that the world has changed and the COVID-19 pandemic has created a new normal? The answer for most is, ‘constantly’!
For those of us who work in the world of online tools, monitoring, and data collaboration, our methodologies have built a future-proofing resilience for businesses. One thing we can all agree on is that the pandemic has acted as a catalyst for change.
Consequently, this has made individuals and organizations come to terms with wider questions, such as the need for business travel, frequent physical meetings, physical monitoring and inspection. The list goes one…
According to research group Statistica collaboration tools have a central role in enabling remote work. This emphasize the role modern technologies play in enabling different remote work concepts.
Not only are information technology decision makers looking to improve IT infrastructure and work-from-home-capabilities, but employees are generally acknowledging the many different applications and devices that can positively impact their work environment.
The numbers speak for themselves.
REMOTE MARKET
- Share of employees working remotely is now 30%
- Enterprise on cloud infrastructure services $129.5bn
- Microsoft Teams daily active users worldwide: 145m users
SPENDING
- Most increased business software spending amid COVID-19 Web conferencing software
- Collaboration software market size worldwide 12.4bn USD
- End-user spending on cloud based conferencing solutions 4.1bn USD
Against this background many pundits have provided false horizons. No travel. No work places. No physical meetings. We’re not going to be dealing in absolutes for business practice going forwards, but more to creative solutions – hybrids of business travel, important interpersonal time together (trade fairs or corporate meetings), interspersed with online meetings. Clearly, this has disrupted business models many were comfortable with pre-Covid.
Democratizing The Process
So, now people are accustomed to collaboration facilitated through Teams Meetings and other online platforms such as Google Meet, Skype, and a host of innovative cloud-based solutions. Intuitively, and in real terms, this approach dovetails perfectly with the rationale for WATS, because the system is able to integrate any test and repair station, and enable sharing in real time of test data.
It allows users across the world, in different manufacturing units, across supply chains to gain manufacturing insights in real-time, directly through a web browser or mobile device. This truly democratize the process, provides visibility, accountability and empowers organisations to ensure they get it right. If there is a problem, this can be identified quickly and dealt with, potentially saving time, cost, and even the threat of production units delivering flawed components or products.
In terms of meetings – such as online reviews – accessing WATS in real time enables manufacturing, quality, design and engineering teams to review the dashboards, stats and reports ahead of a scheduled meeting. This in turn allows them to make informed decisions and make best use of available time for everyone involved.
If we all have access to the same information, there’s no need for laborious exchanges of data that become out of date as soon as it is received. Real decisions and effective strategies, corrective action and workarounds, need real time data. If you wrap these elements together then you have a highly effective way of meeting.
Finger On The Operational Pulse
It can also be argued that in some respects the digital experience is better than the physical experience. By that I mean visibility, bringing together numerous parties, including geographically disparate, different organizations, controlled through different permissions, accessing the common dashboard. This provides the perfect troubleshooting environment, and allows individuals to truly collaborate, focused on finding and agreeing solutions.
In terms of monitoring, this approach also enables organizations to continuously have their finger on the pulse of their operations, wherever they may be located. Perhaps one of 10 factories is falling behind on yield. The data from others can be shared, and through best practice and analysis of specific problems, that particular unit can benefit and increase productivity.
In times gone by, there would be phone calls, laborious reports and site visits, all taking time and money if investigative teams needed to travel. Through WATS this can be dealt with through access to real time data and analytics. The WATS team can also provide insight where required.
We Might Not Be Time Travelers Yet!
In a use case example: a company in Europe has a manufacturing plant in Brazil. The team at WATS just got a service ticket. There’s something seriously wrong with the process and tests in Brazil. So we all hop on to a Teams call and log on to the WATS system.
The team in Brazil explain the error they have found, we check it from our side and then we meet to help provide a way forward and fix any issues. So, it’s just like a standard way of using WATS. We don’t have to go to Brazil! We don’t spend time travelling; 24 hours to get there.
The cost benefit ratio: 2 hours versus 24+ hours. Moreover, we don’t just provide the customer with a ‘situation report’, we can go into the same system, see data, interrogate, analyse, troubleshoot, see something different, discuss this in an online collaboration meeting and resolve it.
We might not be time travelers yet, but we certainly help organizations manage their time, monitor their systems, and make informed decisions in a cost effective way.
Sign Up Today
for Free
Discover what WATS can do for your testing and manufacturing processes.