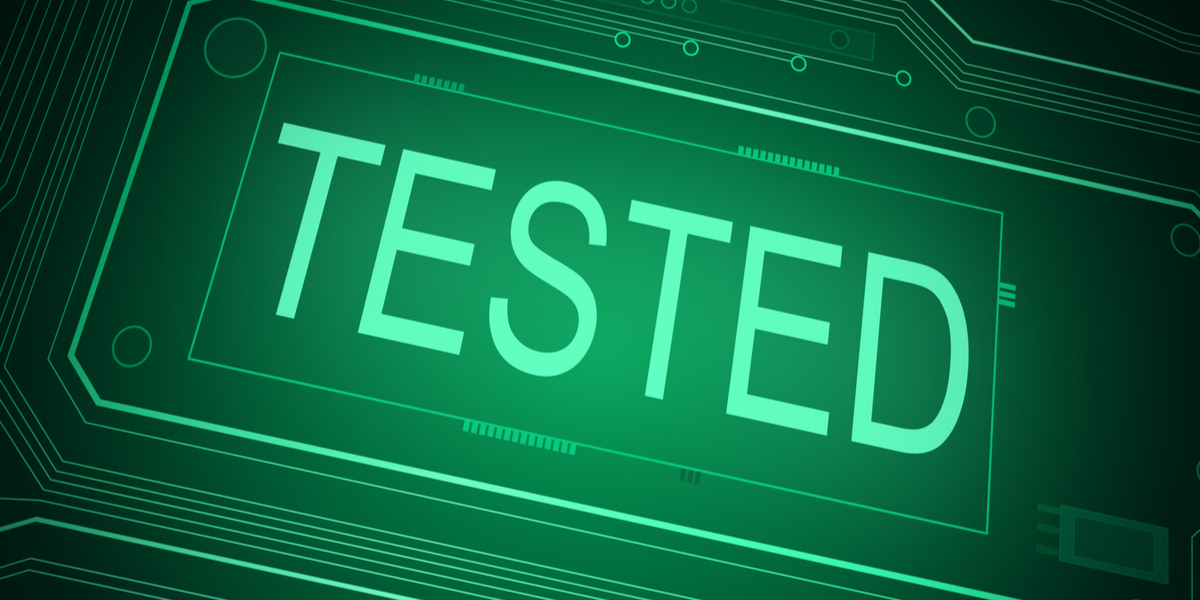
A frequently used phrase in life, and business, is that ‘You can’t be too careful…’. That’s true to an extent, what’s wrong with being cautious, or checking or testing repeatedly?
That said, there comes a point when you have to make a judgement call on where to draw the line. We’ve all heard of ‘analysis paralysis’!
Plan, test, and look for failures – to improve the process
So, how do manufacturers strike the right balance? A number of organizations look at testing as a necessary evil and at a cost. However, if you plan, test, and look for failures you can improve the process. If you store and find data, this can all add up to valuable intelligence that can be shared with colleagues across operations, wherever they are.
Tests are a valuable asset: if you use them in the right way
Tests don’t have to be viewed as problems waiting to happen. If you do it the right way and have a plan and look for the right failures, you’ll be able to improve processes and products over time. Tests are a valuable asset if you use them in the right way.
That’s where automated test data and monitoring systems such as WATS help to make sense of your test data. WATS stores, reports, and follows up the data. Additionally, it provides advanced capabilities to get proactive control of your manufacturing.
Centralize your test-software and unit-firmware distribution with granular control based on products, revisions and locations. Get full control of the distribution of MAC and serial numbers, so that no value gets mistakenly duplicated.
Proactively track and monitor the detailed maintenance status of all your instruments and test interfaces, and avoid loss of performance. And finally, implement advanced alarms and notifications based on the collected test data, to allow for early interventions.
Over testing and under testing: striking the right balance
You have to find the right test for the application. Necessarily, and rightly, all companies think about the costs. The important factor here is weighing up the need and benefit. You have extreme testing for satellites – where repair in operation is not an option. No second chances for a component failure in space!
Then there are commercial products that are unfinished – but can be fixed easily, post production or with software updates, or easily replaced. The potential downside is that this can ruin the customer’s confidence. Take for example, a new car that has to be frequently brought in for repairs. Word gets around and that can seriously dent a brand image and ultimately negatively impact on the bottom line.
Pushing out as fast as possible and fixing it later is a risky strategy that should be avoided at all costs, despite the pressure of investors (seeking ROI), competitors, and the need to generate sales as soon as possible.
For industry, there are two scenarios: over-testing and under-testing. But there is a middle ground. The answer is in striking the right balance. Testing to give customers enough confidence and not replacing that much but gaining a reliable product instead. The middle ground with testing provides a demonstrable increase in quality and saves you money.
It is essential that data is interrogated, informs the process, and insights learned are applied in the next round. Continuous improvement is a net gain all round. If you test and do the same thing over and over, you can deliver better quality, but you can’t increase the level of quality throughput, while decreasing the cost. That’s why you need to have a plan and purpose to improve the production process from start through to shipping.
Testing can be a strategic tool if used proactively
Another benefit of access to test data is the ability to monitor and even integrate with multiple vendors. This allows you to review the quality as needed and explore the entire production process — testing can reveal what’s working and what isn’t — across the value chain.
Companies know how much money they spend on testing. But if there is a difference between vendor A and vendor B and they never look at the underlying data, there is no learning. Continuous improvements need to be a proactive exercise. Testing can be a strategic tool if used proactively, not just a retroactive fix for problems.
Standards and protocols may change depending on where your manufacturing unit is based, and testing can vary wildly across different countries. Some require rigorous tests and others no requirements to test.
Separate the root cause and ensure that something fails less
To give an example; say a large electronics company has multiple sources of products – like PCBs. As a consequence, they may use three different vendors – however, one of them offers lower quality components. But which one? Having a tool that WATS will help you navigate multiple suppliers because you can easily compare them.
Sometimes components in a device are placed close together. But if you use the data in the context of R&D, you can separate the root cause and ensure that something fails less.
Finding problems is meaningless unless the problems can be eliminated. An infrastructure needs to be in place to determine and resolve. That’s where the WATS approach can add value and ensure that data becomes a strategic business tool across the manufacturing value chain.
Emerging requirement for companies to see aggregated test data is absolute
A prime example is the old/current way of working with subcontractors. You received the reports and monthly test results are perfect. All is good, or so it seems. If, however, they use a component that has been tested several times, alarm bells start ringing — it’s clear that there are faults that haven’t been properly resolved. But there needs to be a genuine resolution — a proper test procedure will catch broader errors rather than just ‘pass a test’.
The emerging requirement for companies to see aggregated test data is absolute and will only increase in importance. By leveraging commercial solutions for this data collection and reporting you avoid the trap of assuming a business intelligence framework for your test systems is a trivial development project.
Get more articles like this each month(ish)
Sign up to be the first to know when new articles are published.
Subscribe