
Yield, and First Pass Yield, in particular, is common terminology within the electronics industry today. Although many still lag far behind when it comes to collecting data to consistently track theirs.
Despite these terminologies becoming common, there is no standard. The definitions of First Pass Yield vary a lot from company to company.
A standard definition that is getting more and more traction is what some refer to as True First Pass Yield. In this article, we will look closer into this definition.
In general, True First Pass Yield is
- Based on ALL test results, and includes even trivial test failures
- Unique to each test operation your product goes through
- Not something you can manage through Microsoft Excel
We’ll discuss the benefits for companies to consistently track and optimize True FPY. Plus look at the premises needed to ensure that this is not only used as a selective “vanity” metric. But a metric that helps guide informed continuous improvement.
Content covered includes:
- Different types of yield metrics used in electronics manufacturing
- How True First Pass Yield helps weed out inefficiencies
- Excessive retesting as an example of such a problem
- The need to optimize test coverage when working with First Pass Yield
- Why First Pass Yield is not a metric to optimize product quality
- How True First Pass Yield provides transparency and fosters accountability
What are some different variations of Yield that are used?
Broadly speaking, there are three types of yield that are used in electronics manufacturing.
- Output Yield
- Rework Yield
- (True) First Pass Yield
- “Batch Yield”
The difference between these lies in when a failure is first recognized.
With Output Yield you only consider the failures that causes you to scrap a unit. This type of yield can easily run close to 100%.
The Rework Yield metric is traditionally more common. Here you recognize a failure when the unit goes to rework or repair. Part of the reason why this is a common approach is that most EMS companies adopted MES software technology early on. And repair documentation is a core feature of these. With repair information, and production quantities already in the MES system, this metric becomes very simple to calculate. The Repair Yield can also easily trend high, often in higher range of the 10th percentile.
Both Rework Yield and Output Yield are often referred to as First Pass Yield. But this is incorrect. In reality, First Pass Yield in the context of electronics manufacturing is a test-centric metric.
That means your Yield recognition should come from the results of the test stations. And include any and all scenarios where the test sequencer flags the test as failing. Without having this view your relative results when compared to a company actively managing True First Pass Yield will fall short when it comes to
- Transparency, internal and across your supply chain
- Accountability for different groups and people that contributes to building products
- Productivity
- Product quality
- Profitability
In any and all scenarios we are also including trivial test failures. Such as the operator forgetting to power on an instrument or similar. If these things happen often enough to have the statistical significance they should definitely be on your radar.
There is also a variant of First Pass Yield, which it is based on batch ID rather than serial numbers. This is most common very early in the build process when the unit has still not been assigned a unique serial number. Because the serial number that you need for a unit-centric yield calculation is either static (NOVALUE) or random (a random number for each test run, including retests) your ability to extract actionable information from the First Pass Yield metric is significantly limited. Either all failures except one will belong to test runs later than the first attempt, or all will be counted as first-attempt failures.
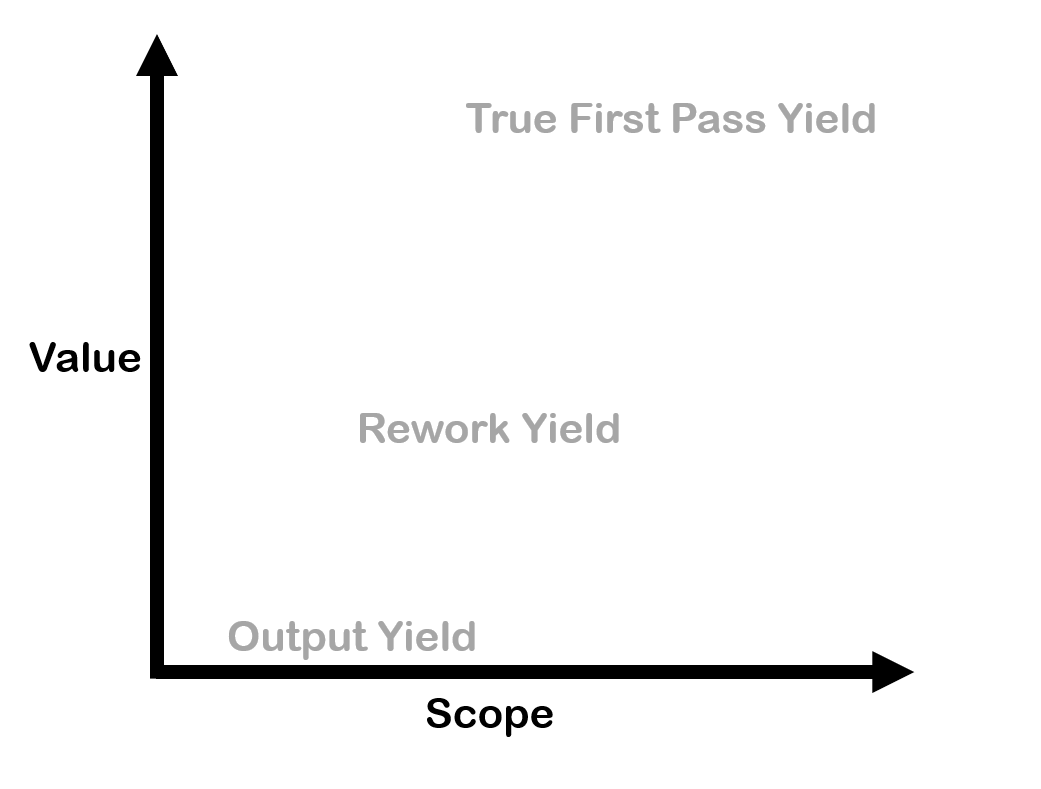
Types of inefficiencies detected by True First Pass Yield
Your company might follow methodologies such as Lean Six Sigma or Total Quality Management. Or it could be that none of these formalized methodologies are used.
Regardless, there are probably many wasteful activities and inefficiencies that are causing damage to your productivity and profitability.
At your company, and in your supply chain.
These waste activities are many and varied. But a common factor is human error. Behaviors that does not help your company prosper. Very often, manufacturing uses product centric KPIs to monitor how well they are doing. For example, efficiency output on a power electronics unit. But these metrics often occurs very late in the process flow. And although they touch on the most important performance metrics of your product, they are not the only determinants if a product will fail in the field or not.
To get the full potential value, you need a solution that has a sufficiently wide scope to capture all inefficiencies and trivial failures. To capture them where they really originate. And proactively managing True First Pass Yield offers exactly that.
True First Pass Yield is an effectiveness metric
Metrics and visibility that are efficiency- and effectiveness-centric gives you much better possibilities to intervene early on. And they provide proper guidance to your factory and engineering staff. A design related decision might cause the unit under test to be difficult to properly connect to the test system, with frequent failures because of this. It does not go to rework. It will pass the test eventually. It is an efficiency issue, not a product issue.
But regardless of the type, it IS an issue, and you must attend to it.
Does your data reveal this scenario?
Why lack of data causes retesting to be a problem
A very common damage of this kind is excessive retesting of your products. A product fails a test and is tested over again. Once or twice is probably ok, but when a test is redone 10 times it is clearly an issue at hand.
It does not have to be that this specific retest poses a quality concern.
Often the product could still be flawless, but the weakness be in the test system itself. Perhaps the test interface board, that the operator solves by wiggling the cables a bit. When the product passes on the 11th attempt, this mentality is allowed to manifest itself.
But imagine that the next time you have an issue with the product itself. Poor connectivity between a PCB and an antenna input. The operator reruns the test over and over. Perhaps he applies some pressure on the connector on the 6th attempt. That again unintentionally gives better connectivity between the two components. Test passed; unit shipped.
How can True First Pass Yield deal with human error?
But what if your “Northstar” was True First Pass Yield?
With full visibility into the underlying failures, their measurements, associated repair operations and perhaps even warranty cases, this problematic behavior would never get to infect your operations. It would die out. And it would give you the full picture on what technical changes you need to make sure that your test operators perform at their best.
If the test operator from the example above, with a flawed test system, by default sent the unit to repair the story could be very different. The repair statistics would show No Failure Found, and you could use that to flag a potential issue with the test itself.
Optimizing test coverage
It is extremely important to acknowledge that your First Pass Yield Metric only is an indicator. And that it has an inverse relationship of your current test coverage. If your test coverage goes down, you detect less failures, and the yield metric will improve.
But you want the First Pass Yield metric to be representative of the actual reality. Very often that requires you to optimize the test coverage. The best time is during the New Product Introduction (NPI) phase, but it is never too late for good initiatives.
Process Capability Analysis is a good tool for this exercise. When combined with measurement trend visualization it is easy to prioritize. To differentiate between the tests that have the potential to be problematic and those that in reality allows faulty products to leave the factory.
At one time, we experienced that a Quality Assurance Manager in a factory turned off the monitors that displayed their real-time yield metrics. Because they were consistently below his targets. This mindset is a direct threat to data-driven continuous improvement, where his focus was solely on his own metrics, rather than what was good for the company.
First Pass Yield is not about improving quality
If you take all factors into account, yield improvements and improved test coverage is generally not done to improve the quality of your products. But rather to make sure that you have the right quality.
To give an example; imagine that you have infinite resources at hand. You could then probably deploy QA initiatives to make sure that no flawed products left the factory. Perform rigorous testing, and hire the best and brightest big-data engineers from Google employees to deal with analytics. But the process of getting there would obviously be very expensive, more so than the money saved from reducing warranty claims.
In general, if you go from 90% First Pass Yield to 100%, at some point the marginal profit will go negative. You added quality improvements becomes to expensive. At this point you should move from improving yield and coverage to maintaining it.
So rather than being about improving quality, it is about optimizing quality. Finding the test coverage and yield target that is right for your company. That is right for your industry. And the quality expected by your customers.
Rolled Throughput Yield vs First Pass Yield
Most likely your product goes through several processes, with different tests for each. This can be tests for subcomponents, PCB / PCBA tests, In-Circuit-Test, burn-in testing, final function test, to name a few. Each of these have their own First Pass Yield, as this is a metric that relates to the individual test processes.
Rolled Throughput Yield tells you how big a percentage of your products goes through all if their processes without failing. And here lies another problem. One that affects almost all companies, and it related to supply chains and outsourced manufacturing.
Even if you have standardized on True First Pass Yield as your Northstar, what if your PCB suppliers uses Finalized Yield? Sure, perhaps they operate less efficient than you (but who pays the bills at the end of the day?). But how can you know that the same quality issues from poor test coverage and retesting is not transferred on to you?
The answer is that you can’t. You need to centralize and uniform the data, with one portal and one philosophy governing it all.
Transparency in the First Pass Yield metric
Since the yield is only indicative, you need transparency into the underlying data. You need to be able to slice and dice it as you wish and understand the contextual relationships at play.
What products have the most failures? Which revisions? How does test station A compare to B, or how do factories compare? What were the common trends during manufacturing for a batch of units returned under warranty?
This transparency and visibility help to foster accountability in your organization. Accountability in your supply chain.
It is not difficult to see why Microsoft Excel will fall short when it comes to transparency.
Sure, it can calculate a yield percentage number to show you. Even track it over time.
But what informed decisions will you extract from this percentage?
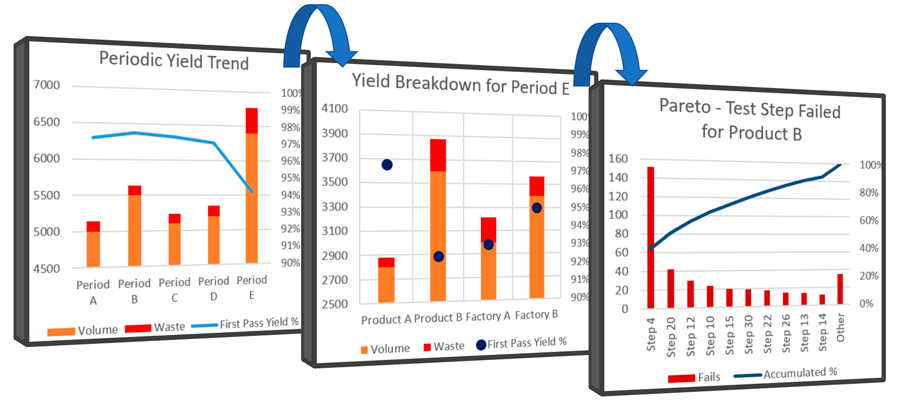
Artificial Intelligence in electronics manufacturing
Many view AI as an exciting area that can help them sort out all their manufacturing challenges. Unfortunately this is currently only theoretical.
The problem in the real world is that the dynamics of the different dimensions that affects production results are extremely difficult and costly to model. And you need a data model to compare your actual performance against. The result is that you reserve these modelling projects only for components that has very high costs or ultra-high volumes. And where the relevant parameters are very static. At the current stage, only a few subsets of a few industries where this applies. Primarily semiconductor and some types of products within the Automotive industry.
And the information purely relates to product quality, to reduce expensive scrap and to a certain extent to reduce warranty claims.
Not the overall efficiency of your product introduction processes.
WATS provide you with an operational advantage for managing your First Pass Yield
WATS is a Test Data Management solution for the unique challenges in electronics manufacturing. A solution built around the premise that a representative True First Pass Yield is the most important metric an electronics manufacturing company can have.
It was built to solve, among others, the challenges discussed in this article.
The architecture makes the centralization of data from outsourced manufacturing seamless. It fosters collaboration throughout the supply chain to benefit all stakeholders from your suppliers through to your customers. WATS provides you with full transparency into the underlying data to fully understand the different test and repair failures that represent your First Pass Yield metric. The result is an unrivalled ability to reduce warranty costs, internal scrap, production labour costs, and data management activities.