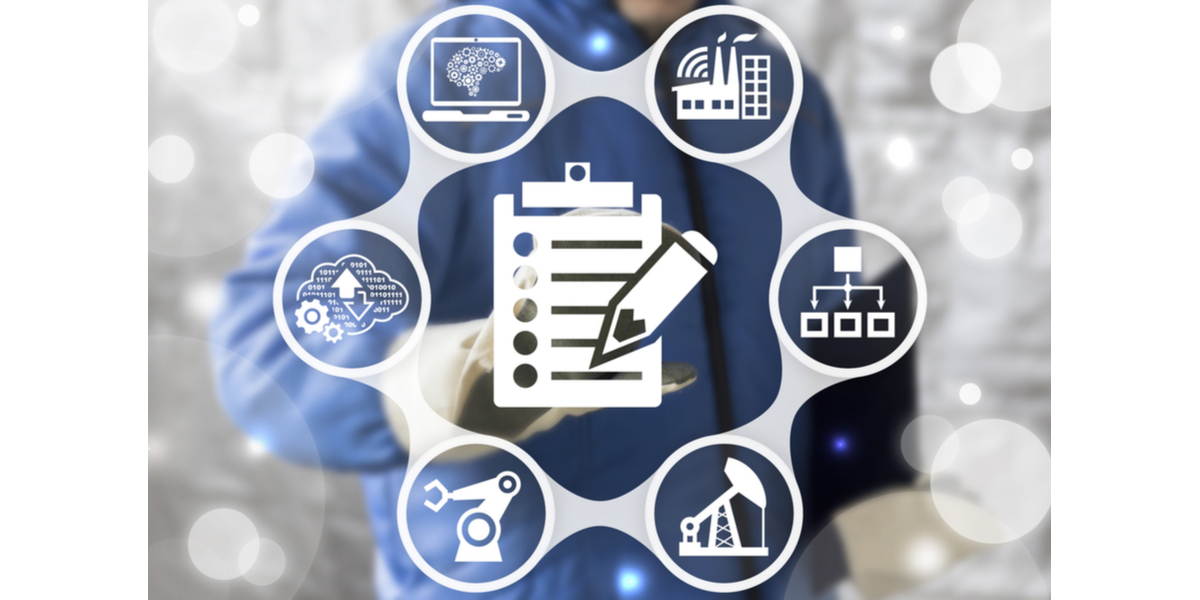
If you’re using manual checklists in manufacturing testing and operations, you’re almost certainly doing it wrong! That’s the stark warning from WATS sales director Vidar Grønås who explains that digital checklists, even for SME manufacturers and fabricators, can prove to be a time saver and add traceability.
There are numerous processes that need to take place in manufacturing or assembly, not just as part of the essential testing of a product, but throughout the production line – from start to finish.
It may be hard to believe, but the majority of companies involved in manufacturing still rely on manual checklists. Not just for specific or minor tasks – but across a range of scenarios, such as:
- Electronics components production
- Fabricating wiring cabinets and other assembly units.
- Visual inspection of a device at the end of production line
- Ensuring that LED displays function correctly
- Establishing all connections work
The (literal and metaphorical) list can go on… and on!
Manual checklists are highly inefficient & provide an opportunity for errors
When you consider the additional data that needs to be tracked in a manufacturing scenario – receipt of items, goods inwards/who received items, inventory, items received in good order etc – a digital checklist seems like a no-brainer.
But, the fact is, many businesses still retain manual records – separately creating a multitude of spreadsheets and dropping them into folders on various machines, or even separately filed paper-based records. Not only is this highly inefficient, it provides an opportunity for errors to creep in and multiply. This causes significant limitations when it comes to an understanding of the performance of these inspections and ensuring traceability.
The answer is to make your manual checklists electronic. This allows users to record directly into a tool specifically designed for this task, such as Manual Inspection, an operating interface where users log in and perform a checklist — any type of manual process such as the end of line inspection.
The operator simply scans a serial number using a computer or tablet allowing them to easily perform checks and report the data centrally – all in real-time. Not all product tests generate an automated test report at the end. Very often, one or more tests that take place during the manufacturing process is manual, where the results are documented on paper, or in a spreadsheet file.
The Manual Inspection Module in WATS features a sequence builder where you can graphically design the test flow, along with a web interface that takes the test operator through all the necessary steps. The resulting report goes directly into the same database as the rest of the test data, and you ensure full unit traceability.
A digital checklist allows questions to be answered immediately
In addition to great efficiency and elimination of errors, another key benefit is traceability – recording the data digitally makes it easy to organize and easy to find, who tested it, previous information.
As referenced previously, a lot of companies have manual checklists on paper – including some advanced global blue chips.
The digital checklist allows questions to be answered immediately, 24/7 across locations, and global operations: How many units were finished, in that week, see by the operator, test stand, location, country, performance, how many per shift. This provides an important added level of control, visibility and traceability on the checklist in the system.
Businesses take their data from a passive to an active state
With paper-based systems, whilst the data will exist, it is rarely or never used – but using a simple digital method you can extract and recall it.
In this way businesses take their data from a passive to an active state, and digitising this information makes it available to use.
This is especially important in assembly and inspecting and can impact warranty claims providing a chain of evidence and proof that the process was correct and error-free.
The paper trail is not traceable, but with the digital checklist as our customers are finding, you can collate, record and analyze the data. This electronic protocol is another step along the way to an automated test sequence.
Get started with WATS Today
Start with the free version.