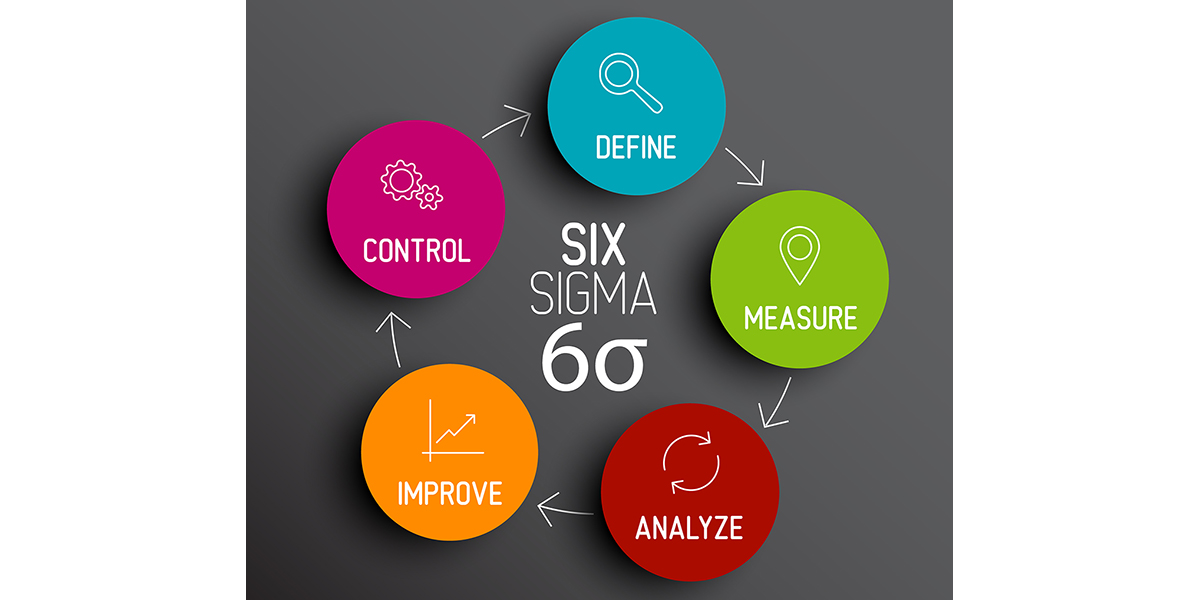
The rapid speed of innovation in manufacturing has introduced automation and a spectrum of production efficiencies.
Mads Dahl, a Six Sigma black belt and Chief Operating Officer of Virinco, the company behind WATS, explains how the system is completely consistent with the Six Sigma principles.
Perfect Score
Many businesses are fusing manufacturing operations with back office functions and introducing digitalization and a cohort of technology improvements, but still need to chase that elusive perfect score.
That’s where lean processes and the discipline of Six Sigma come into play. Six Sigma has an impressive manufacturing pedigree. Introduced by American engineer Bill Smith while working at Motorola in 1986, then famously Jack Welch made it central to his business strategy at General Electric in 1995. Since then, it has become the de facto basis for advanced manufacturing and continuous improvement protocols.
It’s worth reviewing how the problem-solving process of DMAIC (Define, Measure, Analyse, Improve and Control) – the encapsulation of Six Sigma process – works and integrates with WATS. Not only providing data links but providing proof points and shortcuts to analysis and continuous improvement.
DMAIC refers to a data-driven improvement cycle used for improving, optimizing, and stabilizing business processes and designs. The five-phase DMAIC improvement cycle is the core tool used to drive Six Sigma projects.
Contrary to some of the information about Lean Six Sigma, the practice is simple and easily understood – practitioners are graded similar to the martial arts colored belt system. Since the practice is based upon clear principles, it can be implemented in any organisation, across any industry and in businesses from small to large.
As with any other process or practice, leadership in the organisation must be committed to a climate of never ending improvement.
Troubleshooting Tools
WATS and Six Sigma go hand in hand and essentially provide the all in one troubleshooting tools that any organisation would need to identify issues, solve problems and optimize systems, production or production quality.
It helps to first break down the DMAIC process by element from start to finish, although with continuous improvement you are never really finished.
D: Define
The problem comes from the test phase, production as a yield, repair or product quality issue. Here you define the problem. In essence you will only describe the problems, without pointing towards the solution. This is established by understanding data from measurement and analysis. In this way problems will be prioritized and through WATS data and results will be provided from testing.
M: Measure
No need for additional tools. In WATS, the measurement is already conducted. Fast and easy. The data is in the tool and can now be viewed and taken from the WATS reports.
A: Analyse
In WATS, the analysis is prepared in the tool. You just need to understand the analysis. By using this analysis, it is relatively easy to decide where the problem originates and you can start to understand how the problem can be fixed in the Improve phase. It is important to isolate the root cause.
I: Improve
With solid data from WATS and the analysis complete, the next phase is improvement. You may need to change the hardware or software in the test or the product to speed up the production. Alternatively there may be a need to remove the identified quality issues.
Hardware can take longer than software to improve and this phase will often benefit from collaborating with experts and colleagues to figure out the approach to fix first. Some solutions will necessarily be short term, others longer term.
That said, every improvement needs to effect positive change, demands examination of feedback and an understanding of how to move this along. This may start with a small batch test, followed by further analysis and refinement.
C: Control
Use WATS to see the results after the improvement. Dig into the analysis and see the improvement in production. If the improvement did not work fully and you need to adjust more, just take a new DMAIC cycle, this is also easy in the WATS environment.
Think Lean, Think WATS
The WATS Manufacturing Intelligence platform helps you put all of your manufacturing test and repair data to work. WATS lets you see your data as one: in real-time, directly in your web browser. This allows for an unrivaled ability to transform data into actionable insight – through statistical and qualitative analysis.
Your test and repair data holds indisputable stories about electronics design flaws, manufacturing weaknesses, waste, quality issues, operator mishandling and much much more — stories about lost profits. But without unrestricted access to your test and repair data, these stories can never be told.
WATS is the foundation for continuous improvement for any serious electronics design and manufacturing company. So next time you think lean, think Six Sigma and WATS to ensure you attain as near as possible to the perfect score!
Sign Up Today for your free trial
Discover what WATS can do for your testing and manufacturing processes.