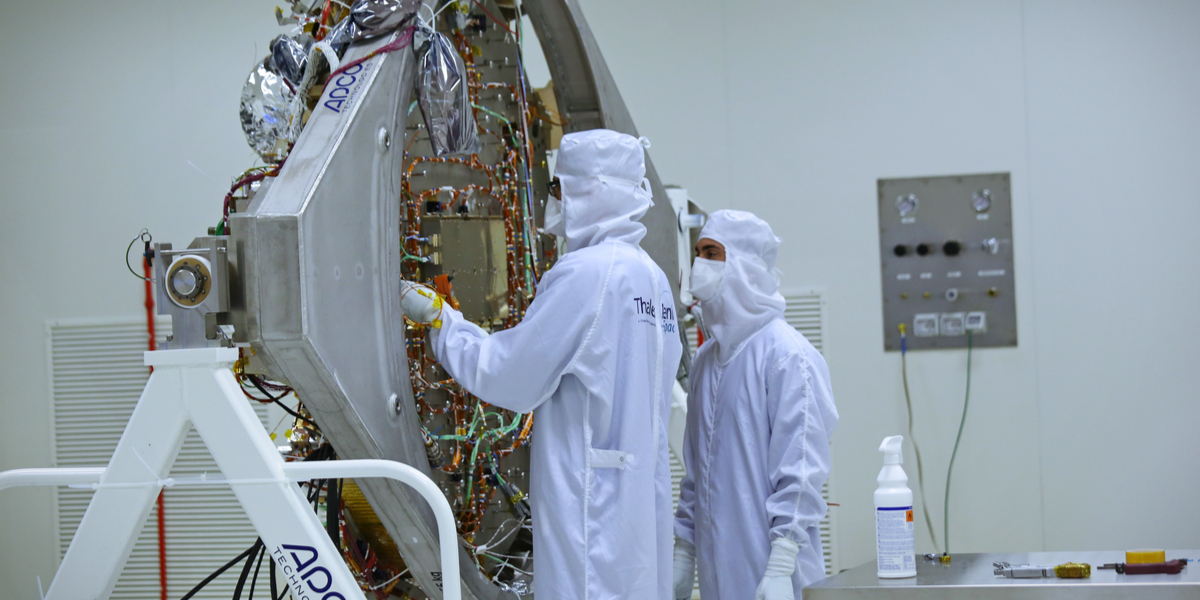
Telexsus have been supporting companies developing & manufacturing electronic hardware and systems in the UK and Ireland for over 10 years. The company, that has recently become a distributor for WATS, selects their range of specialist development, verification and test products bench-marked against industry-leading capabilities and the advantages they provide to clients. Their customers are across a spectrum of high value manufacturing sectors including: Aerospace, Telecoms, Semiconductor, Defense, and Scientific Instrumentation.
Driving down costs and boosting efficiency
Established in 2010, the company’s engineering background provides an in-depth knowledge of all the products it provides and can fully explore and understand clients’ technical requirements. This allows the team to deploy the appropriate tools and methodologies, and introduce new approaches and technologies which enable better product design, verification, and testing.
The company is now offering WATS as an integral part of testing protocols for a range of design, manufacturing and contract manufacturing clients, a solution that also plays a significant role in helping to drive down costs and boost efficiency, even in the high value and complex electronics hardware sectors such as satellites, aerospace and defense.
Establishing domestic resilience
The high value electronic manufacturing industry has not just weathered the economic uncertainty ushered in by the pandemic, but in the case of the semiconductor sector, has experienced massive hikes in demand, outstripping supply and consequently inflating costs across the supply chain. Political considerations have added to the volatility of the sector and shaken up the traditional centers of global manufacturing.
Against that backdrop, manufacturers in the UK and Ireland, alongside Europe, North America and Japan are establishing domestic resilience through supply chains embracing contract manufacturers and OEMs, closer to home. Just focusing on one sector, the UK’s space industry has seen unprecedented growth. With more than 80 leading space companies, headquartered across Scotland alone, focusing largely on satellite technology – the value of the sector is expected to rocket across the next 12 months, and exceed £4 billion by 2030.
So, how does this big picture affect individual manufacturers? What has that got to do with testing and product quality?
With increased opportunities, together with innovations in manufacturing including digitization, automation, IOT and 3-D printing, the need to understand processes and monitor data, even for low volume batches is paramount.
The days of ring binders have thankfully mostly been left behind, but it is staggering to see how many test and production engineers still rely on spreadsheets, and hard to access disparate records.
Businesses that fail to understand this rarely get a second chance
Conventional wisdom, in some low volume, high value sectors – for example, satellites or aerospace – provides a false sense of security. The logic dictates that low volume, complex assemblies are front-loaded with testing in-situ in the lab. The assumption being the prototype becomes the production model and therefore the quality template, with little or no need to worry about defects or errors. Apparently, one board in one hundred is an acceptable loss.
This thinking on the face of it may be understandable. However, it is hugely flawed and poses a potential threat to the electronics manufacturer. For example, they may not track analog measurements or drift, which would help them track gradual changes in their processes. Future-proofing, resilience and agility are not ‘nice to have’ concepts but real and pressing demands for a successful manufacturer. Businesses that fail to understand this rarely get a second chance.
Immediate access to data
A system such as WATS, provides traceability, and when you think of the stringent requirements of high value products from defense to medical devices, you then begin to understand that the old ways of working are no longer fit for purpose. Moreover, they potentially pose a threat to product integrity and customer confidence. Is it really worth the risk?
In modern electronics manufacturing, the processes at play are incredibly dynamic such as:
- Component changes
- Test system maintenance
- Environmental factors
- Different test operators
- Unit firmware
These are just a few that translate into a huge range of potential causes of a product of reduced quality. The modern KPI toolbox for Quality Assurance must facilitate full transparency into all of these, alongside a well-balanced ability for early intervention.
The investment in automated and remote systems such as WATS, not only provides real time analysis and transparency of process, but provides complete consistency of records and access to data, wherever you are, across remote plants worldwide. It also importantly links the CEM with the manufacturer, providing immediate access to data and forestalls any nasty surprises on delivery!
The sometimes used excuse that high value electronics manufacturers can afford to absorb component failures no longer holds true, especially in today’s dynamic and competitive market where reputation is everything and contracts can be lost faster than they are won.
Myth of high value electronics only relying on manual processes needs to be forgotten
As with any process or analytical tool, you need to use it to gain the benefit. When customers gain an appreciation through working demonstrations, they often wonder how they were able to survive using the old ‘tried and trusted’ spreadsheets and notepads. The wake-up call of asking where the records are from three years ago and finding that the sole keeper of that knowledge has retired can be solved through the smart deployment of remote systems. In the case of WATS, the data can be accessed through mobile phones or tablets, and that can support the most sophisticated electronics product manufacturing programs.
The myth of high value electronics only relying on manual processes needs to be quickly forgotten, if you are serious about winning in today’s increasingly demanding market. Manufacturers need an introspective view of what they are doing and recognize the potential for improvement. No one, and no product, is perfect!
Book a Demo to see WATS in action
Subscribe our Newsletters
Get updates on Test Data Management for Electronics Manufacturing.