Meet Some of Our Customers and Learn from Their Success Stories about How They Use WATS to Succeed and Improve.
Read more”If you took WATS away from us now, we’d have a serious problem. We rely on it every day – for insight, for quality, for customer satisfaction. It’s a core part of how we operate
Steven Van HoutManager Test Engineering at VDL TBP Electronics
Read more”Having easy access and oversight of all test data gives insights that support both production and R&D. It makes us confident about how we analyze limits, performance, and it’s a part of our daily workflow
Petri ReimanTest Specialist and Test Team Manager, Satel
Read more”It’s amazing to have this level of real-time insight into the product testing that’s happening around the world, all from the comfort of my desk.
Heikki HeimonenCapacity Manager, Aidon
Read more”This tool also enables us to remotely understand what is happening much more easily, adjust and verify. We feel much more reassured regarding potential non-conformities reported by clients, as we have access to the entire product history.
Fabien De BarrosTechnical Manager, VOGO
Read more”Being able to see the data in the way we now can helps us see issues we didn’t know we had. The same goes for communicating with component manufacturers because data is a language everyone can speak.
Kenny KreitzerPrincipal Test Engineer, Badger Meter
Read more”WATS has been an integral part of our digital transformation journey within our test environment, and the solution supported Medela in continuing to deliver quality medical devices while driving operational excellence and innovation.
Gaetano GalabreseIndustrialization Engineer, Medela
Read more”When you’re scaling or dreaming of scaling, that’s what WATS helps you do. It’s that simple.
Morten Hessilt KjærAudio Engineer, AceZone
Read more”The whole operation is more complicated than when we started, but WATS simplifies the ways we’re able to analyze data and share it among the whole team. Everyone here always wants more data to improve the quality of our decision-making. WATS gives us that, and it’s totally seamless
Nikolaj Egeskov ØstergaardTeam Leader – Test Systems Engineer, Trackman
Read more”“Looking ahead, WATS isn’t just a tool for us, it’s part of a broader vision. It allows us to collect and analyze data from every stage of our product journey, giving us clarity and control we’ve never had before.
Andy CorteenOperations Director, Adder Technology
Read more”Thanks to WATS, SKIDATA´s production keeps running smoothly – while saving money and increasing product quality.
Gerhard SchwimmerFormer Test Engineer, SKIDATA
Read more”The integration of test data upload has been a significant development that WATS tailored for us, really improving our ability to troubleshoot and understand each test report comprehensively. WATS has removed the manual side of data analysis.
Sahar ChowdhurySenior Photonics Engineer, Envisics
Read more”The support from the WATS side is great and new integrations are being released all the time. From day one to now, it’s totally worked.
Christian WolfManufacturing Test System Architect, SOUNDBOKS
Read more”The WATS solution has been a game-changer for us. It’s streamlined our calibration and testing processes to a level of efficiency we hadn’t experienced before. We’re not just pleased with WATS; we’re deeply impressed by its impact and the exceptional support we’ve received, which has been pivotal in our successful expansion phase.
Tor Magnus BriskoddenProduction Test Lead, Zivid
Read more”I’ve been working at Linn for nearly 30 years, and I don’t ever remember a time before WATS when test information has been so accessible, clear, and customizable.
Matthew RandsQuality Engineering Lead, Linn
Read more”WATS’ support is just totally unmatched. It’s clear that knowledge sharing is a big part of their purpose, and that really shines through when it comes to getting even more value out of the WATS solution.
Aaron GreenyerTest Automation Engineer, EPOS
Read more”For me, the biggest benefit of WATS is being able to easily drill into finding root cause errors. It’s continuously improving. The visibility of data is drastically improved. Before WATS, it was basically impossible to track anything at scale. Now, we put dashboards up on big monitors, enabling everyone to see everything.
Svein Olav HusebySenior Industrialization Engineer, Q-Free
Read more”The diagnostic features and traceable process allows issues to be quickly identified across customer teams and the supply chain.
Magnus NamorkOslo-based senior test engineer for Indra
Read more”As database experts, we need an accurate tool that records data and gives us immediate oversight and statistics access.
Tapio LeveelahtiLeading manufacturing engineering teams, Suunto
Read more”Transparency helps colleagues in production and R&D to communicate with management, illuminating the prospect of nasty surprises or error multiplication.
Christian BergerZurich-based Project Lead at Zühlke
Read more”It makes for a dynamic culture and an energy that thrives on innovative solutions. WATS helps us – and our customers – to quickly dive into data, identify issues and implement fixes and improvements
Tero LeppänenVP of Testing and Product Verification, Etteplan
Testimonials from our Customers
”Without spending intensive time in manual data preparation and computing, I can get test process analysis easy and quickly.
Matthias StraußProduction Manager Service and Support, Sennheiser
”WATS is a very strong tool. You go on to the site, set up your instance, and just like that, you’re ready to go.
Ole Happle SørensenTeam Manager, Production Test and Device Test automation, Epos
”We are using WATS to effectively harness our test data to be used as a business driving tool.
WATS gives you the potential to base your actions on the actual data. Often the problem is the amount of the data. WATS has the right tools to bring front every essential parameter while preserving the capability to handle full proof audit trail of the device history records.
Lauri AnttilaTest Development Manager, Planmeca
”I have been working intensely with automatic test systems for the last 20 years. As long as I can remember storing test data and analyzing them has always been a challenge. It stopped the moment I started using WATS.
Without spending intensive time in manual data preparation and computing, I can get test process analysis easy and quickly, which offers us an additional boost for our continuous lean activities in production.
Matthias Straußroduction Manager Service and Support, Sennheiser
Fast and easy to integrate
Espotel has integrated WATS into several existing test stations. It has been a pleasure to find out how easy it the commissioning can be done.
WATS has the functionality for analysis and quality improvements. Virinco guys are always listening to the customer and improving the WATS SW based on the feedback collected.
– Tero Leppänen, Etteplan Finland
Quick to set up, easy to integrate, flexible, quick technical support
We’ve used WATS for a while, and we have around five development and production test licenses.
WATS greatly simplifies recording test results from both development testing and production testing. Small tests can quickly be made and modified throughout a product development phase, to record results from e.g. component value variations, variations in temperature/pressure, etc.
With the new WATS solution, small test environments are set up quickly and at a much lower price than earlier.
– Øystein Johnsen / Happy WATS Customer, Bergen, Norway
Versatile, easy to implement, good functionality, processing data instantly
Probably the best test data collection tool in the market.
Our company is outsourcing and insourcing our production. We always implement WATS on the shopfloor to control and improve the testing and the production flow. We have around 200 test machines and collecting 25000 test & repair reports every day into WATS.
WATS makes us confident that we are making the best products for our customers controlled through WATS. WATS is easy to install on the test platforms using NI Teststand. Reports are sent instant and collected in the WATS system, visible in the centralized reporting just seconds after end test.
– Global Test Manager
Norway
Easy implementation, good interface, easy to find the result and trends fast, makes troubleshooting faster
Starts WATS as a first thing every morning to check new test results and trends from production. Test and repair data is collected from more than 200 test machines on different sites. Then we quickly can find challenges and dig into measurements and repairs on products to solve them, and have excellent quality and control. In addition, WATS is fast and easy to implement on test machines.
– Test Engineering Manager / Happy WATS Customer for more than 10 years, Norway
EPOS Secures Improved Yield & Better Product Knowledge With WATS
Ole Happle Sørensen is a Team Manager responsible for Production Test and Device Test automation at audio company, EPOS. Headquartered in Copenhagen, Denmark, EPOS focuses on delivering high-end audio solutions designed for enterprise and gaming use.
Eltek Transforms Field Failures Into Streamlined Production
Mads Dahl is Vice President of R&D Industrialization at Eltek, a Norwegian firm that produces cutting-edge industrial power supply systems for the telecoms industry. During his tenure at Eltek, he’s seen some fascinating improvements in the company’s production process – the result of Eltek’s longstanding collaboration with WATS and its parent company, Virinco, as he explains.
Some of our Customers
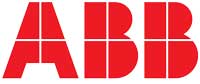
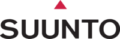
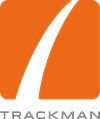
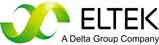
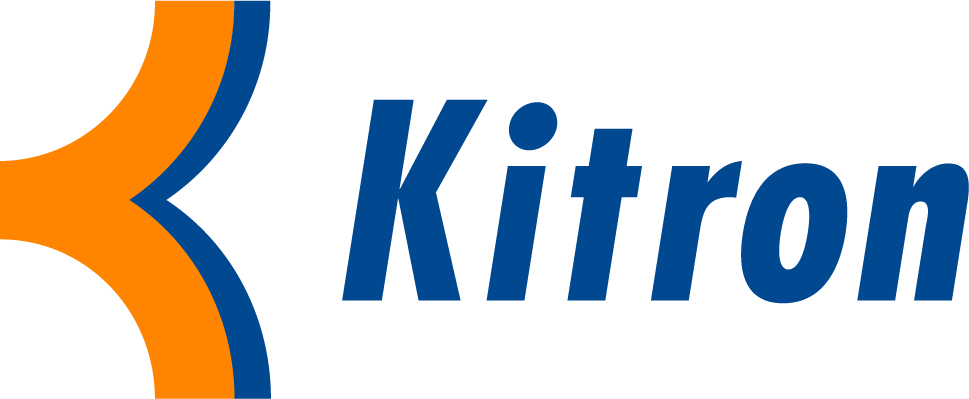
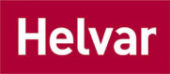


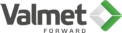

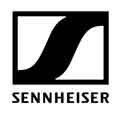

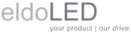

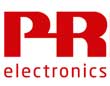
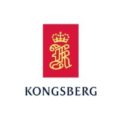
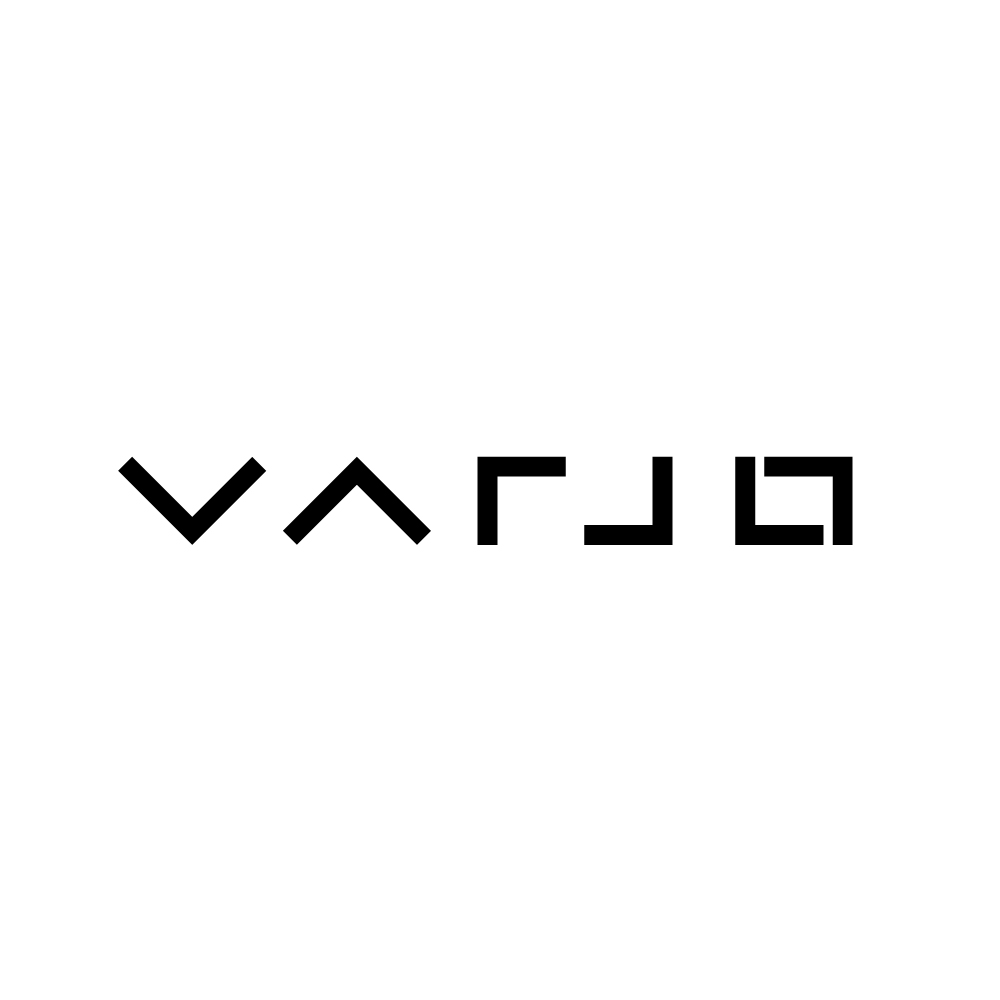
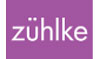
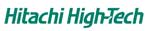
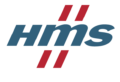
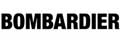
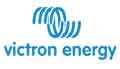

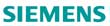
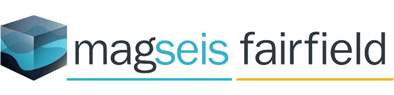

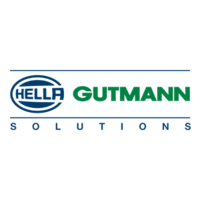
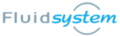
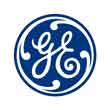
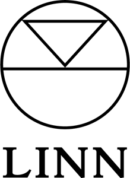
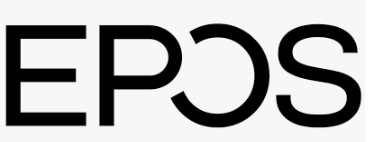
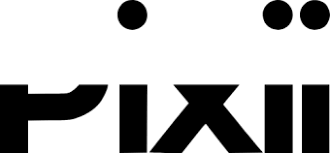
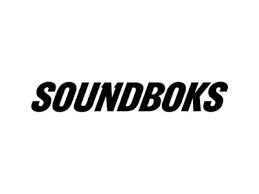
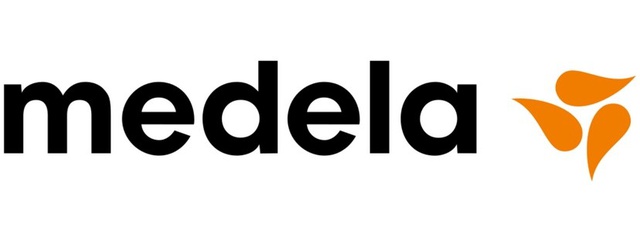
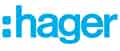
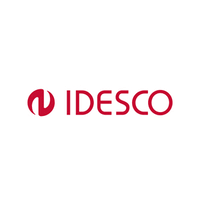
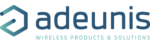
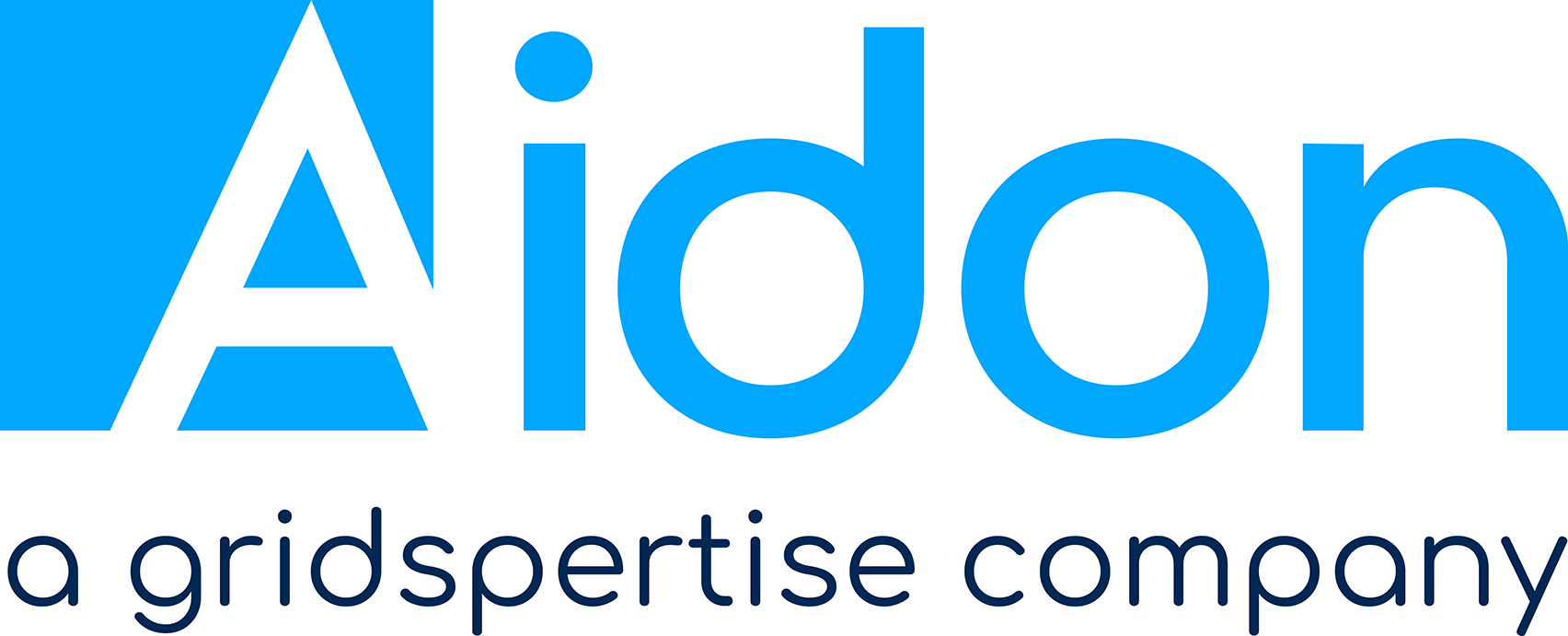

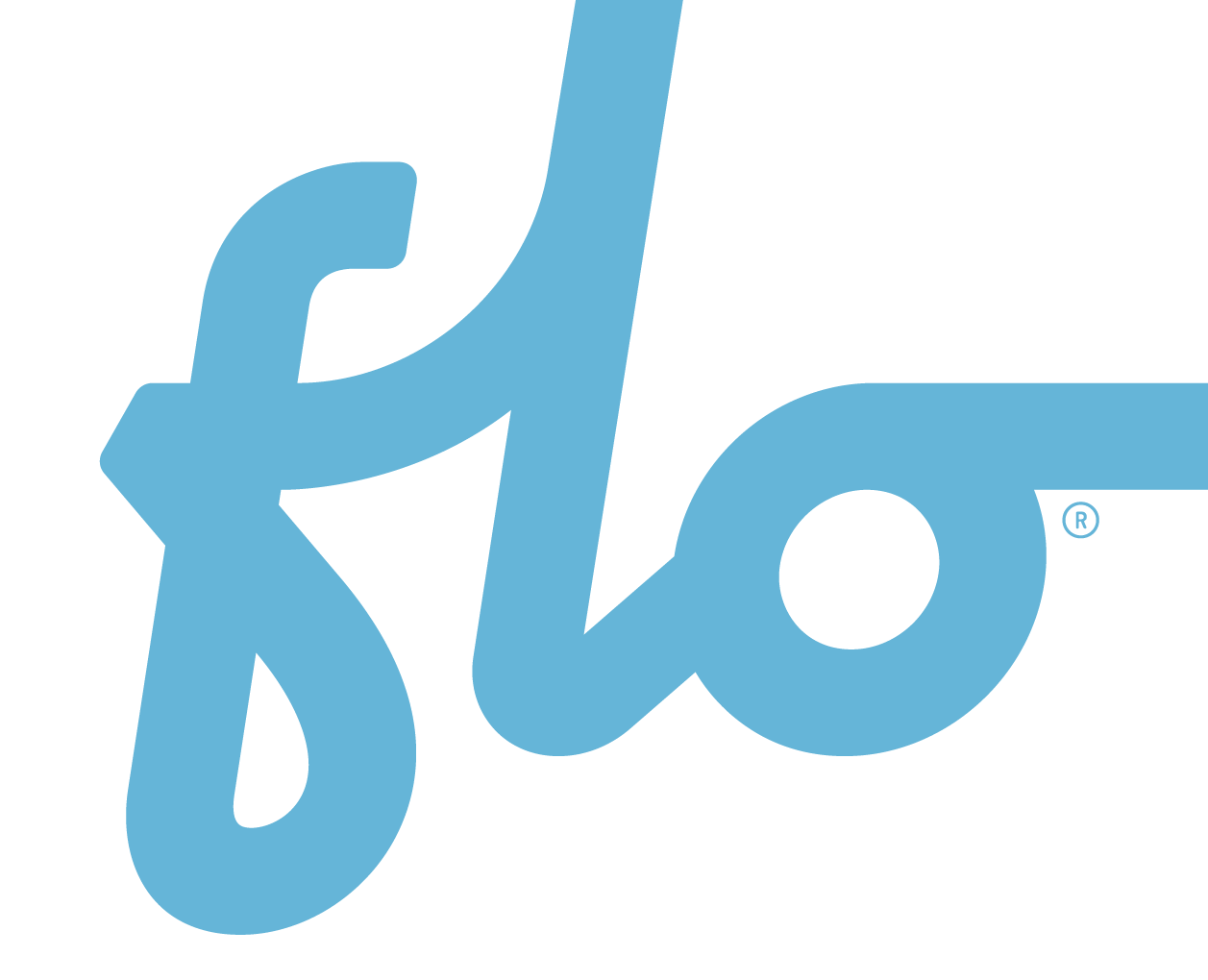